Part 2 of a series on optimizing control systems.
Milacron is focused on enhancing control systems that turn data into information that can guide the company's injection molding machine users to more efficient processes.
It continues to upgrade M-Powered, a networked, IIOT suite of observational, analytical and support services that’s tailored to individual users. The company offers an optional new sensor package that provides base-level monitoring of machines in its Cincinnati line of presses. In addition, the company recently integrated iMFLUX control software into its own controller for use with M-Powered.
Related stories: Usability, artificial intelligence guide Engel's controller developments; Arburg control features optimize molding process; Sumitomo emphasizes user-friendliness; Haitian targets Industry 4.0; Training helps Nissei customers maximize potential; Wittmann Battenfeld's B8 limits downtime, improves quality
M-Powered increases uptime and saves energy.
Through M-Powered services, users have access to sophisticated analytics and data scientists that can turn raw data into meaningful and actionable information. Some data refining can be done at the machine while other portions of the job require high processing power and must be done remotely.
The sensors reduce the time needed to diagnose issues, said Andy Stirn, director of new product development, applications and product management. They work in real-time to provide health assessments on crucial components such as hydraulic pumps, feed screws, screw tip assemblies and heater bands. With them, operators can head off poor performance and premature wear of components.
“These sensors are enabled through M-Powered and are compatible across many control systems. By maintaining a connection with the machine’s control, intentional actions can be recommended on frequent wear-and-tear parts, that often are the root causes for quality escapes,” Jump said. “Rather than detecting a point failure, we quantify wear and tear and allow operators to make smart decisions. The dashboards notify operators and managers to order new parts when these components begin to impact the bottom line through excess energy use or quality escapes.”
According to Hogan, the director of engineering, the company works with its customers and tries to match its expertise to customers’ growing needs.
“Sometimes this means working side-by-side with our customers to understand their hurdles and other times this means introducing our customers to new technologies,” he said. “The goal that drives our innovation passion is to address our customers’ pain points that hold them back from being more successful. Any competitive manufacturing company focuses on safety, quality, delivery and cost. Our customers are no different. Our exclusive partnership with iMFLUX is one great example of how we deliver solutions for our customers.”
“These complex processes are maintained through auto viscosity adjustments that take the stress off the operator,” Stirn said. “IMFLUX integration stabilizes and optimizes processing, while maintaining optimal cycle times, part weights, dimensional stability. It also reduces warpage, molded-in stress, tonnage, injection pressures — leading to overall repeatability and consistency.”
Hogan said Milacron strives to introduce new capabilities while decreasing user complexity.
“Just like our smartphones, we are moving more towards screen-based or contextual-based information,” Hogan said. “This is not revolutionary, but rather evolutionary design migration. Of course, we aren’t looking at turning the user interface into a big smartphone. Some features need to be always available and not only present under certain contexts. This is a customer-centric perspective that is focused on ease of use.”
The company’s diagnostic capabilities also are evolving.
“More capability also means more opportunities for the system to provide feedback,” Hogan said. “Therefore, machine faults and alarms must be simpler to understand, more geared toward the user, and offer the user some guidance on how to resolve the issue.”
Future improvements will focus on part quality; more meaningful and actionable data; higher levels of “smart cell” integration; and ease of use, Stirn said.
Bruce Adams, senior staff reporter
Contact:
Milacron LLC, Batavia, Ohio, 513-536-2000, www.milacron.com
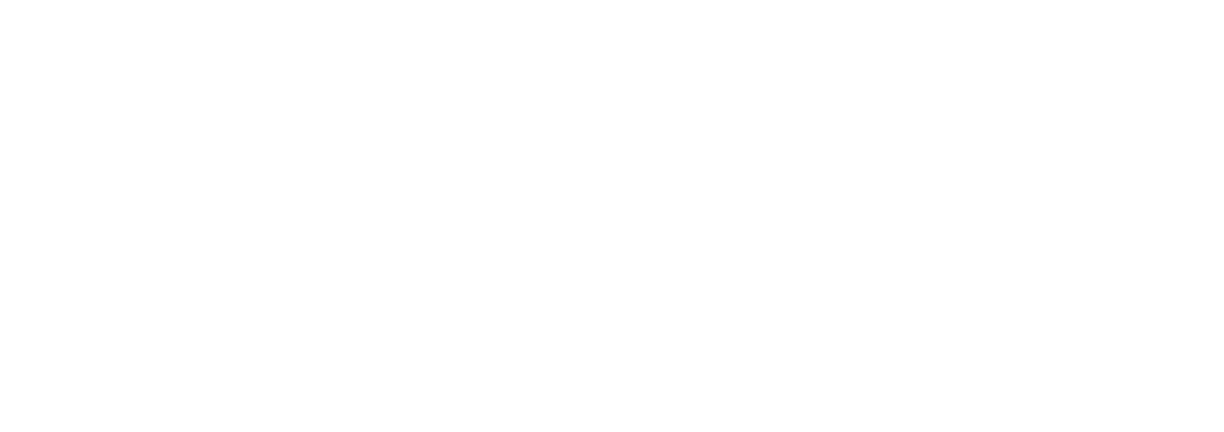