A California injection molder that has for 30 years specialized in manufacturing equipment used in testing laboratories is rushing to keep up with demand caused by the COVID-19 pandemic.
“We have been slammed by work related to the coronavirus and are shipping testing product all around the globe as fast as we can make it,” said Anthony McCracken, VP of product development at Scientific Specialties Inc. (SSI) in Lodi, Calif.
Since mid-February, in response to the demand, SSI has:
- Purchased seven new Arburg injection molding machines;
- Purchased Conair auxiliary equipment;
- Purchased five Sepro robots;
- Commissioned five new molds;
- Worked around the clock to expand its Class 100,000 clean room by 2,600 square feet to a total of 42,400 square feet to accommodate the new equipment.
Plenty of plastics processors started making personal protective equipment with equipment and material already on hand, but SSI has ramped up production of its core products at a dizzying speed. So far, SSI has invested more than $3 million, and the number is growing every day.
“We have always maintained a level of production capacity that has historically allowed us to quickly meet any large increases in demand for our products; but increases in demand due to this pandemic have required over a tenfold increase in our throughput of certain products,” said Peter Hovatter, VP of operations. “We are now running at max capacity in many product lines and still have a growing backorder.”
How has the company managed this explosive COVID-19-related growth?
“We knew we needed to fulfill the drastic surge of global demand as fast as possible, so we early on increased production considerably, running all available key presses as often as possible,” Hovatter said. “At the same time, we started to evaluate where we needed to increase long-term production capacity the most and prioritized where the greatest urgency exists. During this period, we have been utilizing our current staff as much as possible and, through various avenues, have been expanding our workforce.”
SSI manufactures a wide range of consumable racks, tubes, pipette tips and containers used in research laboratories. Many of its products are designed for polymerase chain reaction (PCR) testing, a process to make millions to billions of copies of a specific DNA sample, which allows scientists to take a very small sample of DNA and increase its volume to study it in detail.
SSI’s products are in high demand now because its test tubes are used to hold possible COVID-19 samples and reagents, and its pipette tips help transfer the samples and reagents to PCR plates and tubes, which are in turn processed in specialized equipment that can detect the virus.
The need to make products that are not contaminated by human DNA guides much of SSI’s manufacturing process. More than half of the company’s 64 injection molding machines are in a clean room, and production is heavily automated to eliminate the possibility of humans touching the products.
“Our main goal is to eliminate DNA contamination,” McCracken said. “We do a lot of DNA-testing products, so one of the most important things for us is to use automation in a way that the required labor input is separated from the physical product as best as we can.”
SSI’s products are primarily used by drug companies, universities and other research laboratories. They are not used in forensic DNA testing, which requires an additional level of sterilization.
About 70 percent of SSI’s products are branded for distributors and the other 30 percent carry one of SSI’s trademarked brands.
“We put a lot of emphasis into quality and consistency, not changing things, not changing the material, not changing the process, not changing the molds,” McCracken said. “We really focus on the lack of change, which is very good from the laboratories’ point of view, because they don’t want change.”
He said that laboratories do not want to jeopardize lengthy, expensive tests with surprises in their lab equipment.
SSI owns all its molds, does not sub-contract work to outside vendors and, with very few exceptions — such as O-rings — does not buy outside parts. “I would say 99.9 percent of the plastic product we sell is manufactured here at this one facility where we can control the quality,” McCracken said.
There are 64 molding machines in SSI’s 122,000-square-foot factory, including the seven purchased since the pandemic started. Some 59 of the 64 are Arburg presses, ranging from 50 tons of clamping force to 200 tons of clamping force. The other five are from Negri Bossi in the same general size range.
No molding machine is more than 12 years old. Older series Arburgs are often sold after 15 million to 20 million cycles. The newer H series Arburg presses are running through 25 million cycles, and may go even further, McCracken said.
“When we see 20 million cycles coming up on the clock, we find they are very sellable on the used equipment market because they haven’t broken down yet,” he said. “We maintain the equipment in really good condition, so a machine we have been running at a 6-second cycle goes off to a custom molder who runs a 30-second cycle, he’s basically getting a new machine for four or five years. And he hasn’t paid a lot of money for it.”
SSI uses its five Negri Bossi machines around the clock to mold containers for pipette tip products. “The Negri Bossi is a fine machine for this type of molding, being very reliable and more economical than the Arburgs both in price and running costs,” McCracken said. “Also, the process engineers like the control system.”
The size of SSI’s molding machines is shifting upward as business grows. “The 120-ton machine is more of our normal machine than what used to be at the 80-ton level because, as we have increased sales, the easiest way to keep up with that is just adding cavities. Some of our molds now, instead of being eight cavities, are at 16, 24 or 32 cavities. That requires a larger machine.”
Prior to purchasing the new machines to meet COVID-19 demand, SSI used about half its injection molding machines inside its clean room and half outside. Now slightly more than half will be inside the enlarged clean room.
Outside the clean room, SSI manufactures more labor-intensive products such as racks, grids and lids.
The company owns a variety of different Arburg models. “We don’t buy the same series of machines,” McCracken said. “We buy the series that matches the product we expect to be making on it. If you understand Arburg’s machine structure, you will understand how we have different types of Arburgs in different types of roles.”
SSI’s machine inventory currently includes six presses for two-shot molding, and the company plans to add more.
It also has one Jomar blow molding machine it uses to manufacture small tubes.
Automation is a key to SSI’s success, and the company has 12 full-time employees in its automation group.
“We have a programmer, and we actually build and modify our own automation,” McCracken said. “We are probably more versed in the automation than we are in tooling now.” San Joaquin Delta College in nearby Stockton has an industrial automation program, and SSI has hired graduates and used the college for training its automation staff.
“These guys with us now, they love it here. We have a lot of automation for them to figure out,” he said.
Sepro is SSI’s robot manufacturer of choice. SSI has been moving into Sepro’s six-axis robots. “Instead of the traditional beam robots, we’ve done several programs where we are using six-axis robots that have more flexibility,” McCracken said. “We are finding they can handle changeovers and different products much better than the traditional beam-mounted robots.”
“Automation is definitely a labor-saver,” McCracken said. “But that is not our reason for automation. We do use the money saved from labor to partially pay for the automation.
“We try not to over-automate,” he said. “We haven’t gone to the point where we can replace all the operators. We don’t automatically pop the products into boxes. We don’t automatically do a lot of the packaging end. I would say that we have used automation in a very focused method and not necessarily for total labor savings.”
Part of the automation philosophy is driven by SSI’s product mix. “Our model is smaller runs, lots of special setups, special products, special labeling — all of that means shorter runs and that tends not to be automation’s bread and butter.”
One interesting piece of automation is a machine that weighs bags of small parts to make sure the correct number is inside before the bag is sealed. The machine, built by Yamato Corp., was designed to weigh bags of fruit and nuts but was adapted by SSI for plastic parts packaged inside the clean room.
Conair supplied most of SSI’s auxiliary equipment, and Advantage Engineering supplied the water-handling system. Mold-Masters is the preferred hot-runner supplier and hot-runner controllers are from Gammaflux.
Most of the tooling comes from two domestic suppliers. SSI does not build its own molds but maintains a staff of eight — including three journeymen toolmakers — to maintain and repair its molds.
The company typically makes three to four mold changes per day.
It installed a manufacturing execution system from Syscon PlantStar about a year ago.
McCracken said standardization of processing equipment makes the operation more efficient and gives SSI a competitive advantage. “We have two suppliers of injection molding machines,” he said. “What we do not have is 12 different brands on the floor. We think it is important from the user’s point of view, the processing people.
“It’s bad enough that Arburg changes the control system every 10 years but having lots of different ones would be very difficult. We at least keep it to two brands of programming. A process engineer’s life is difficult enough without him having to know different control systems. You can’t get the best from someone if you’ve got all those variables out there on the floor.
“The same goes for automation,” he said.
SSI uses training products from Paulson Training Programs and has recently begun training its employees using Paulson’s online programs. “All our operators, process people and material handlers go through the training modules based on their job,” McCracken said. Individual training is completed during work hours.
“This area is not big in injection molding, so our people don’t come in knowing injection molding,” he said. “That’s a really nice system that Paulson has developed. It’s a good eye-opener for our people. It helps them realize that this is a serious industry.”
Arburg and Sepro also provide training support.
Approximately 80 percent of SSI’s products are made from PP, with the rest from PE, PC, silicone and TPE. Most have to go through radiation sterilization before they are shipped. Two silos hold 60,000 pounds each of virgin resin.
Scrap is shredded and sold because it cannot be reused to make laboratory equipment. Many of SSI’s products have a 5-year shelf life, so any products that stays in the supply chain for an extended period also must be shredded.
Ron Shinn, editor
Contact:
Scientific Specialties Inc., Lodi, Calif., 209-333-2120, www.ssibio.com
Just the facts:
Company: Scientific Specialties Inc.
Founded: 1990
Owner: Kenneth Hovatter
Location: Lodi, Calif.
Total workforce: 270
Injection presses: 64
Primary products: Plastic products such as racks, tubes, pipettes and containers used in research laboratories.
Ron Shinn | Editor
Editor Ron Shinn is a co-founder of Plastics Machinery & Manufacturing and has been covering the plastics industry for more than 35 years. He leads the editorial team, directs coverage and sets the editorial calendar. He also writes features, including the Talking Points column and On the Factory Floor, and covers recycling and sustainability for PMM and Plastics Recycling.
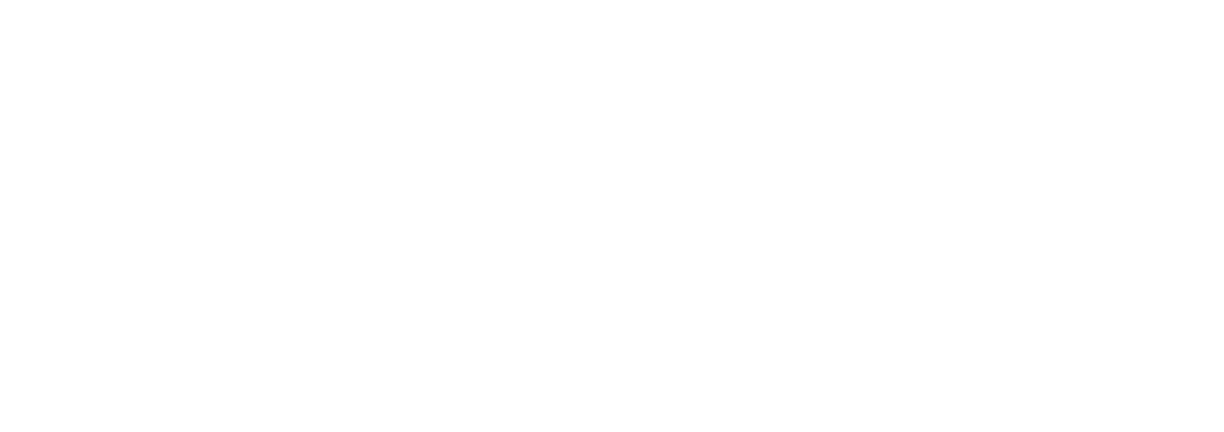