Bin picking has always been a vexing problem for plastics processors, who often have been forced to use human hands because robots were too costly to buy and program for such complex tasks.
Universal Robots has developed a system called ActiNav Autonomous Bin Picking, which some processors may find to be a game-changer. The ActiNav kit contains an Autonomous Motion Module (AMM), ActiNav URCap user-interface software and a choice of 3-D sensors.
The system works on Universal Robots’ UR5e and UR10e series collaborative robots, which are designed for lighter payloads. ActiNav handles parts with dimensions that range from 0.5 inch to 5 inches.
Separately, Universal Robots has also launched a new interface option that easily connects its e-Series cobots to any injection molding machine.
ActiNav was developed as a simple solution for machine-tending applications in which plastic or metal parts need to be picked out of a deep bin and inserted into a molding machine or CNC machine. The AMM, with input from the high-resolution 3-D sensor and CAD matching, determines the best way to pick up the part, then controls the robot to pick it up, orient it and place it in a fixture.
Universal Robots said the autonomous motion control enables ActiNav to reach deep inside a bin that holds more parts, a task that stand-alone bin picking vision systems have trouble doing.
Deploying the system does not require costly and time-consuming vision or robotic programming. It is based on a teach-by-demonstration technique using a six-step, wizard-guided set-up process integrated into the cobot’s teach pendant.
“With ActiNav, manufacturers have the possibility to automate a machining application that was not really open to them before,” said Eric Anderson, Universal Robots product manager, during a recent virtual press conference. “For around $100,000, you can quickly and easily deploy bin picking with a return on investment of less than 18 months for a two-shift operation.”
“Injection molding machines have many inputs and outputs to manage the complexities of the molding process,” said Joe Campbell, senior manager of applications development at Universal Robots. “Standardized interfaces allow for ease of integration and exchangeability.”
The IMM module is installed in the UR cobot’s control box. A 6-foot ribbon cable connects to the expansion bus slot on the control box. It can be ordered for any e-Series UR cobot built this year.
Ron Shinn, editor For more information Universal Robots USA Inc., Ann Arbor, Mich., 844-462-6268, www.universal-robots.comRon Shinn | Editor
Editor Ron Shinn is a co-founder of Plastics Machinery & Manufacturing and has been covering the plastics industry for more than 35 years. He leads the editorial team, directs coverage and sets the editorial calendar. He also writes features, including the Talking Points column and On the Factory Floor, and covers recycling and sustainability for PMM and Plastics Recycling.
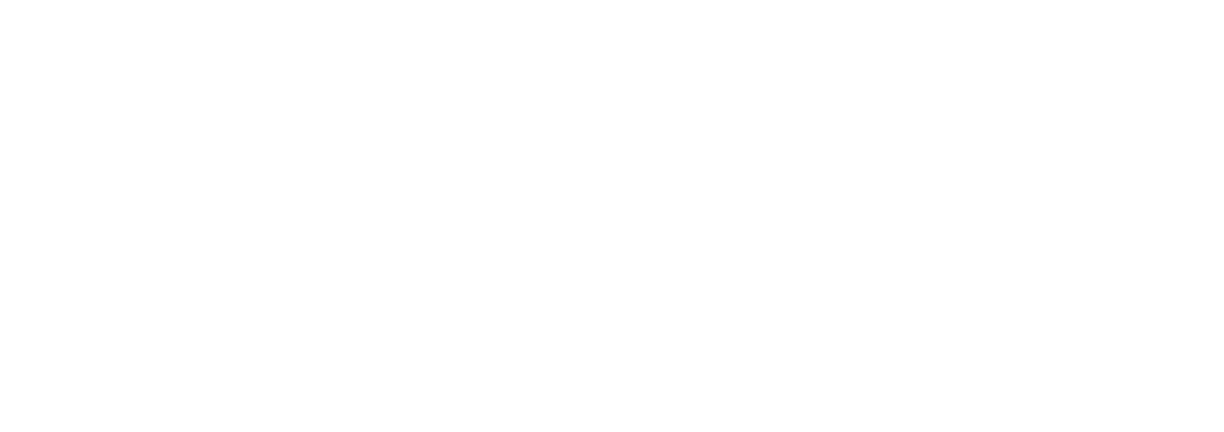