The continued lightweighting of plastic water bottles and caps has led to the development of new machines that can produce lighter weight products more quickly.
Engel introduced new all-electric e-cap injection molding machines in sizes 220, 280, 380 and 420, with clamping forces ranging from about 250 tons to 470 tons, to meet the need for lightweight plastic bottle caps. All machine sizes are available worldwide, the company said.
Engel introduced the first all-electric e-cap injection molding machine at K 2010. At that time, water bottle caps weighed 1.1 to 1.2 grams, the company said. Before 2010, hydraulic machines used accumulators for the injection movement to produce caps.
“Since 2010, the requirements for beverage caps have changed substantially,” said Friedrich Mairhofer, Engel’s product manager for all-electric injection molding machines. “For still water, caps with a weight of significantly less than 1 gram are produced today. As a result, the cooling and cycle times have continued to drop. Where the cycle times 10 years ago were 2.5 seconds, today’s cap machines need to be able to produce at 2-second intervals and faster.”
The e-cap 380 can achieve dry cycle times of 1.3 seconds and cycle times of less than 2 seconds, the company said.
The new e-cap machines feature faster mold opening and closing movements; a more stable machine bed for more frequent load cycles; a reinforced frame and reinforced mold-mounting platens for improved stability; a new cap ejection unit with a hydraulic booster; and a redesigned plasticizing unit with more torque.
The redesigned plasticizing unit includes a new screw and a wear-resistant, sliding-ring non-return valve. These components can better handle new resins that now are routinely used by processors to make lightweight caps. They also help achieve the plasticizing rates that are needed for very short cycle times.
The new plasticizing unit processes highly viscous HDPE “in a particularly gentle way” despite high throughput levels, the company said. This allows for a good melting rate and homogeneity of the melt, which improves process stability and machine repeatability.
The machine’s all-electric drive contributes significantly to its energy efficiency. For example, the e-cap 380 operates at high speeds while using only 0.37 kilowatt-hour per kilogram of resin pellets processed, the company said.
The machine’s braking energy is recuperated, which also contributes to its energy efficiency.
“Every time the mold movement is decelerating, energy is recuperated and saved in the kinetic buffering system,” Mairhofer said. “That happens two times each cycle — deceleration before the mold is closed and deceleration before the mold is completely opened. The recuperated energy is used for mold acceleration, which also happens two times each cycle.”
This function has been available on Engel e-cap machines with clamping forces of 380 tons and more for three years, the company said. It is now available on all sizes of the new machine. All these improvements make the new e-cap the most energy-efficient bottle cap machine on the market, Engel said.
The company offers the e-cap machine with two different ejector drives. Hydraulic ejectors are standard and servo-electric drives are available as an option.
A new feature is that the standard hydraulic ejectors can be made stronger by a switchable hydraulic booster on demand. This feature ensures that the machine operates at peak efficiency during start-up and normal production. At machine start-up or after a production interruption, caps that have cooled in the mold might require more force to eject, the company said. The switchable hydraulic booster will do that. But during normal production when the caps don’t have the chance to cool in the mold, it’s more efficient to eject them using an optional servo-hydraulic drive, which uses approximately 10 percent less energy than the hydraulic ejectors.
Despite the use of standard hydraulic ejectors, Engel classifies the e-cap as an all-electric injection molding machine because the three main movements — mold, injection and plasticizing — are servo-electric driven.
The e-cap features an encapsulated toggle lever and a clean linear guide of the moving platen to meet the strict production requirements for cleanliness demanded by the food industry.
While all-electric presses are more expensive than hydraulic machines, they offer improved operating efficiencies over time. Engel said that due to its energy efficiency, the all-electric e-cap offers a return on investment of less than two years.
Engel has demonstrated its new e-cap 380 model producing standard 29/25 caps from HDPE in a 96-cavity mold made by Plastisud. With a shot weight of 1.3 grams per cavity, the cycle time was less than 2 seconds. The manufacturing cell was equipped with an IMDvista visual inspection system and an Eisbär dryer.
Bruce Adams, senior staff reporter
Contact
Engel Machinery Inc., York, Pa., 717-764-6818, www.engelglobal.com
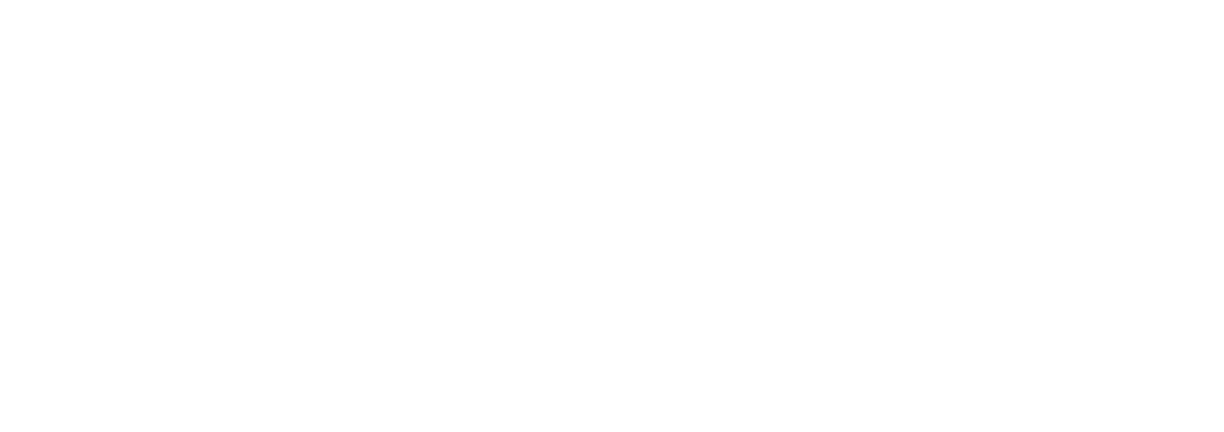