Problem: Inadequate purging resulted in too many scrap products for an injection molder with frequent material changes.
Solution: An olefin-based mechanical purging compound reduced waste at the beginning of production runs.
Cleaning injection molding machines between production runs has long been a vexing challenge. Machine downtime is costly. And if a purging compound doesn’t clean efficiently, it leads to more downtime to remove machine components for cleaning or an increase in scrapped parts.
Beaumont Advanced Processing addressed this challenge by using Barrel Blitz Universal (BBU), a mechanical purging compound designed to deep clean the screw, barrel and related parts. The product is made by Aquapurge Ltd., Hayes, England, out of a stable polymer and a proprietary scrubber concentrate, according to Kevin Durina, an engineering and sales consultant with Md Plastics, which is the exclusive U.S. distributor of BBU.
Md Plastics designs, engineers, manufactures and sells components such as screws, screw tips, barrels, nozzles, end caps, nozzle adapters and heater bands. The company became aware of BBU through one of its product distributors in Ireland.
“Barrel Blitz is a mechanical scrubber that is olefin-based,” Durina said. “The olefin melts but the proprietary part is the scrubber, which is almost like sand. The cleaning is mechanical vs. chemical, because there is no chemical reaction. A lot of processors use chemicals that they have to let sit and then purge out. With Barrel Blitz, the force of the machine applies the mechanical pressure to clean the screw. It will clean 90 percent of the resins used by injection molders.”
BBU was designed to be used between product color changes, resin changes and to clear carbon — degraded materials and plate-out from pigments or additives — from the screw, barrel and nozzle. It is effective in temperatures ranging from 320 degrees to 644 degrees Fahrenheit. It can be used to clean higher-temperature materials if the purging temperature is reduced to 644 degrees or less.
Beaumont Advanced Processing started using BBU about a year ago, according to Rylan Smith, production manager. The company started operations in 2012 and occupies 12,000 square feet of manufacturing space in Erie, Pa. It operates more than 12 injection molding machines with clamping forces ranging from 3 tons to 330 tons and has a Class 8 clean room. It’s part of the Beaumont family of companies, which include Beaumont Technologies, Beaumont Development and the American Injection Molding Institute.
“A colleague of mine received a free sample of BBU and we tried it in a couple of different situations, and we were impressed with how it performed,” Smith said. “When we run nasty materials, it gets everything cleaned out. It is very versatile with a temperature range up to 644 degrees and we can use it on a wide range of materials. Some other purging compounds aren’t rated that high.”
Most of the materials the company runs fall within the useable temperature range of BBU, but when the company uses materials that exceed that temperature, it uses a different purging compound, he said.
“We focus on low-volume production runs,” Smith said. “We are constantly changing materials and we run everything under the sun, material-wise. Some jobs are set up, run for two hours and we change materials.”
The company recently started molding automotive parts and BBU has been helpful with its lens product line, which is unforgiving when it comes to material imperfections.
“Some of our automotive parts are lenses,” Smith said. “If we purge the machine out good with Barrel Blitz, there is less run time before we are making good parts. We scrap fewer parts at the beginning of the run.”
An effective purging job is critical when the company switches from molding a black, higher-temperature material to a lower-temperature resin that is white or clear, he said.
“It’s important to get all the contaminants out of the screw, check ring and nozzle,” Smith said.
The process for using BBU is no different than purging with similar mechanical compounds.
“We raise the back pressure and increase the screw RPM so the screw is fully forward and we are augering material in an attempt to flush the system out,” Smith said. “It scrubs the screw and gets the prior material out of the system. How long we run depends on the material we are trying to clean. You can see the Barrel Blitz when it comes out of the nozzle, so you know when it starts to become clean.”
BBU is available in 44.1-pound plastic buckets. It is not designed to clean hot runners, but it can be used to clean extruders.
Bruce Adams, senior staff reporter
Contact:
Md Plastics, Columbiana, Ohio, 330-482-5100, www.mdplastics.com
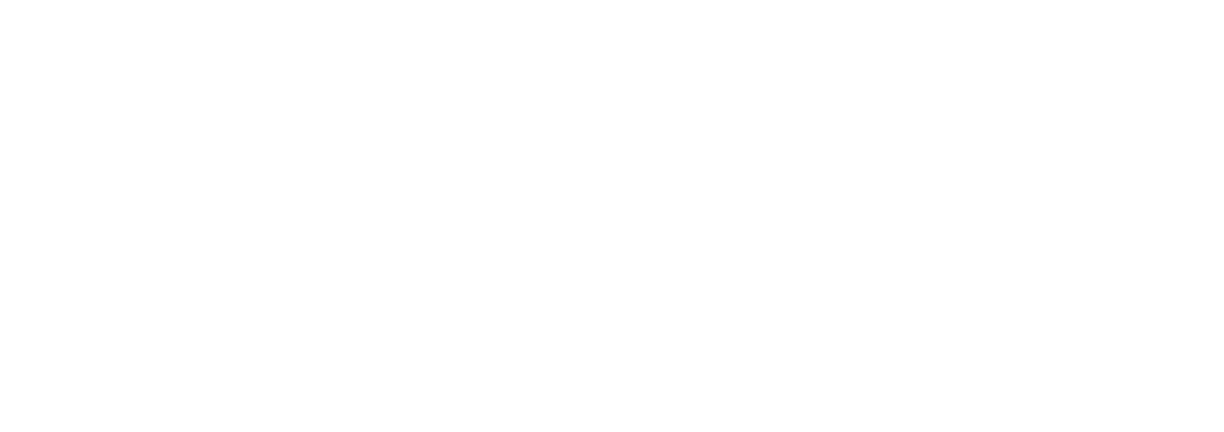