By Bruce Geiselman
As an example of what can be achieved today with chemical foaming agents, a representative of iD Additives, which sells chemical foaming agents, cited the company’s success with an automotive customer. Together, they achieved weight reduction of as much as 50 percent by using chemical foaming agents in the manufacture of an extrusion blow molded part.
“I think the biggest thing that’s changed over the years … from my perspective … is the process has gotten a lot better in optimizing the foaming agents to achieve better density reductions that in the past haven’t been achieved,” said Ron Bishop, an iD Additives technical manager. “Aesthetics that were extremely difficult to achieve in the past, to me, [have] gotten much better with [the] understanding of how to control the foaming agent or the bubbles to achieve [Class] A surfaces.”
While the process has been around for decades, it has improved over the past few years, said Bishop, who has observed interest in chemical foaming growing recently. The introduction of iD Additives’ Micro Fine Cell (MFC) foaming agents about five years ago is one of the developments that has led to improved aesthetic properties in thin-walled applications, he said.
“This product produces extremely small bubbles that can be used for Class A surfaces and can be seen in wall thicknesses as low as 25/1,000 [of an inch] and up.”
One of the reasons for improved weight reduction is a growing understanding of how to optimize the plasticizing process for lightweighting parts with chemical foaming agents. For example, barrel temperatures are crucial to the process to optimize the foaming agent, he said. Precise temperatures are necessary to control the chemical reaction throughout the barrel.
If the process is optimized, and the chemical reaction is controlled, the cellular structure will be very tight and extremely small, he said. If the temperatures are too hot, the chemical reaction is difficult to control, and using too much chemical foam will make achieving the required part appearance difficult.
If aesthetics aren’t an issue, producing more foam will produce greater weight reductions.
Unlike physical foaming processes, which inject a gas at high pressures near the end of the plasticizing process, chemical foaming agents are introduced as pellets or a liquid into the throat of the barrel of an injection molding machine or extruder early in the plasticizing process. This early introduction of the foaming agent offers an advantage because the foaming agents reduce the viscosity of the melt as it makes its way through the barrel, Bishop said.
As bubbles are produced in the barrel, the viscosity of the material changes and it “flows like butter,” he said. The reduced viscosity typically translates into the need for less heat in the barrel, which cuts energy consumption by 10 percent to 18 percent, according to trials conducted by iD Additives.
Using chemical foaming agents also can be simpler than physical foaming, Bishop said. If, in an effort to reduce weight, gas is injected into a melt at too high of a pressure, it can create voids in a part, he said.
“I have not seen voids created by using higher levels of chemical foaming agent,” he said.
Foaming agents today also can produce more aesthetically appealing parts than in the past, he said. While many foaming agents and applications involve producing a foamed inner layer with non-foamed outer layers for aesthetics, for certain applications, a chemically foamed product can feature an aesthetically appealing surface that doesn’t require its encapsulation between two non-foamed layers.
The MFC foaming agents, used primarily in extrusion sheet, extrusion profile and injection molding applications, produce small, tightly packed bubbles.
“You know the bubbles are there, but to see the actual bubble, you would need a jeweler’s loupe,” Bishop said. “I think that is amazing.”
Demand for chemical foaming has grown as processors have reached the limits of other processes.
“We feel like the demand is actually getting bigger, especially for aesthetic parts because years ago, nobody could have done it,” Bishop said. “No one did it, and now, we’re doing a lot of it and there’s a lot of interest in it.”
iD Additives Inc., La Grange, Ill., 708-588-0081, www.idadditives.com
Bruce Geiselman
Senior Staff Reporter Bruce Geiselman covers extrusion, blow molding, additive manufacturing, automation and end markets including automotive and packaging. He also writes features, including In Other Words and Problem Solved, for Plastics Machinery & Manufacturing, Plastics Recycling and The Journal of Blow Molding. He has extensive experience in daily and magazine journalism.
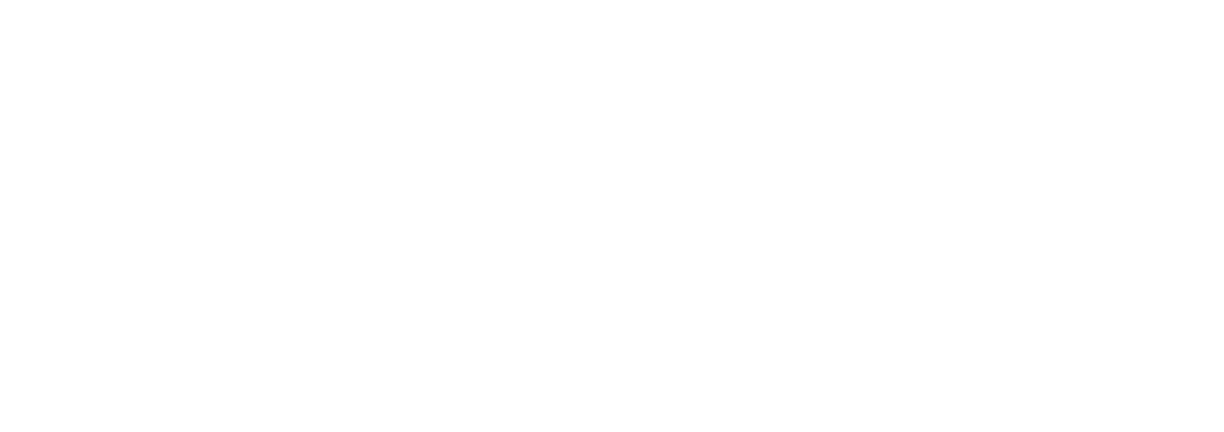