Do you ever think about what your plant floor will look like 10 years from now? It is not very far away when you consider that nearly every injection molding machine purchased this year will still be operating at the end of the decade. Most extruders will barely be at the halfway point of their usefulness.
Certainly, the Internet of Things will continue to change the way machines are connected and control systems will get more sophisticated, but neither of those things will change the way the plant floor looks.
But here is something that might: ABI Research predicts that in 2030, three out of every four industrial robots will be mobile instead of fixed systems.
Today, mobile robots are used mostly in warehouses, although I have seen a couple in plastics processing plants. But when you go to any plastics-related or robotics trade show, you’ll see plenty of new mobile robots. These range from automated forklifts and wheeled platforms (AGVs) that can carry more than 2,000 pounds without human intervention to cobots mounted on a mobile platform. ABI Research predicts sales of automated forklifts will increase from 4,000 units this year to 455,000 in 2030.
Robot sales are strong, and strong sales means more research and development, which in turn will give us robots with more capabilities and at lower prices.
I don’t think the ubiquitous pick-and-place robots we see atop many injection molding machines will disappear anytime soon. They do the jobs they are designed to do very well.
Mobile robots might develop to the point they can do the jobs fixed robots do, plus much more, with very little programming expertise required. The switch to mobile robots could make good business sense in less than 10 years.
ABI Research’s report, “Commercial and Industrial Robots,” predicts that sales of mobile robots will start to overtake traditional robots by 2022. The report also predicts mobile robots will be sold into every sector of the economy.
Mobile robots can communicate with each other, cooperate with each other or humans, perform sequential tasks and move products in or out of the work cell.
The industry witnessed a giant advance when robots came out from behind cages. We are still in the early stages of cobots working side by side with humans, but plenty of plastics processors are interested in how they can use cobots.
Robots that move around the plant from task to task are the next obvious evolution.
Swiss manufacturer Stäubli drew plenty of attention at K 2019 with its fully autonomous HelMo mobile robot system. The HelMo looks like a robotic arm on top of a 55-gallon drum with wheels. Stäubli showed how it can navigate around a plant to gather the items it needs, bring them to an assembly or production area, perform complex tasks that include interacting with humans and deal with finished products. The demonstration ran all day with no human intervention.
Mobile Industrial Robots (MiR), of Denmark, last year showed its new Mir1000 at Pack Expo. With a payload of 2,200 pounds, it can automatically pick up, transport and deliver pallets and other heavy loads in environments that change frequently. It is marketed as a safe alternative to forklifts.
Also at Pack Expo, Japanese manufacturer Omron showed a new model that marries the company’s TM cobot arm to its self-navigating LD mobile robot. It can move wherever the cobot needs to be.
Kuka, another well-known German manufacturer, has mounted its lightweight robot on a mobile, flexible platform. The company said the robot adapts to different manufacturing functions and can communicate and work with other robots.
Universal Robots presents another interesting but lower-tech solution. The company has mounted a cobot to a mobile workstation. A person can move the unit in a way that’s similar to pulling a rolling suitcase. EasyRobotics, which like Universal Robots is based in Denmark, sells the setup for applications where space is limited.
Robots could have a bigger impact than anything else on the way your plant floor looks in the future. It might be a good idea to pay attention to new robots and think about how they could navigate your plant. When the next generation of a HelMo knocks on your door, you may want to invite it in.
Ron Shinn, editor
Ron Shinn | Editor
Editor Ron Shinn is a co-founder of Plastics Machinery & Manufacturing and has been covering the plastics industry for more than 35 years. He leads the editorial team, directs coverage and sets the editorial calendar. He also writes features, including the Talking Points column and On the Factory Floor, and covers recycling and sustainability for PMM and Plastics Recycling.
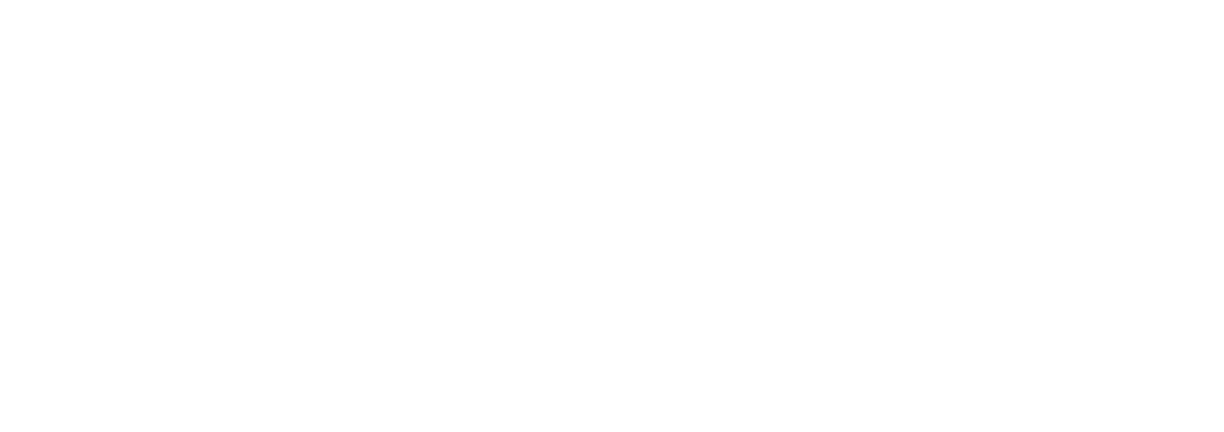