Problem: An injection molder’s dryers weren’t optimal for the company’s growing emphasis on micro-sized parts.
Solution: The company installed 20 Conair MicroWheel units to more efficiently handle the task of drying small batches of the many different engineering grade resins that it processes.
Standardizing equipment and operations is a key objective for David Moyak, GM of Matrix Tool Inc., a full-service tooling and injection molding company that serves a wide range of markets, including the automotive, computer, electronics, medical and pharmaceutical industries. The company, located in Fairview, Pa., started as a mold making shop in 1972 and moved into injection molding.
The company’s business producing micro-molded parts grew so much that it purchased seven Sodick injection molding machines — one each year from 2013 to 2019. The six 20-ton machines and one 60-ton machine are equipped with special controls and features designed for micro-part production. Those purchases increased Matrix Tool’s arsenal of presses to 37, including 24 with 90 tons of clamping force or less. Moyak said he intends to buy more Sodick machines as the company’s business grows and as older machines need to be replaced.
As business grew, it became apparent that the company’s dryers were not suited to a growing product line of thin-walled, micro-electronic and high-speed data connection parts used in circuit boards, telecommunications equipment, computers, cell phones and consumer electronics.
“Our product line was continuing to get smaller, so we were looking to standardize our drying equipment with a space-saving, more energy-efficient dryer,” Moyak said. “As we trialed and evaluated a few different dryers across OEMs, the Conair MicroWheel dryer stood out for its compact size, user-friendly controller and integrated technology. Specifically, the MicroWheel not requiring compressed air, cooling water or frequently replaced desiccant weighed heavily in our decision-making process to select Conair as a long-term partner.”
The company purchased 20 MicroWheel dryers during a three-year period starting in June 2015.
“In addition to saving valuable floor space, the ease of operational upkeep and energy savings were additional advantages,” Moyak said. “Our MicroWheel dryer purchases have saved a significant amount of utility cost. We calculated that the MicroWheels use 50 percent to 80 percent less energy per year than its non-Conair predecessors, which is substantial. If we simply look at the energy savings, our return on investment per unit is under five years in most cases.”
Equipment standardization is important to Moyak because it simplifies training personnel, the manufacturing process and maintaining equipment, he said. That’s especially important because Matrix Tool uses a wide variety of specialty resins to make many different parts.
“We have over 75 unique SKUs within our engineering-grade resin portfolio that we consistently process, often in small quantities, and we needed a small-capacity dryer with advanced capabilities to handle them. In our fast-paced production environment, it is not uncommon to start up and complete more than a dozen sample or production orders per shift of each workday. We pride ourselves on our ability to process a large number of orders per day. This sudden service poses challenges, especially when you consider the number of materials we handle daily.”
Matrix operates 24/5 and on weekends as needed to meet customer demand.
The MicroWheel dryers have advanced technology that allows them to dry the wide range of resins that Matrix uses, according to A.J. Zambanini, drying products manager at Conair.
“Most other dryers that handle these small throughputs are not very advanced. They are usually simple equipment,” Zambanini said. “This is a very advanced dryer that has a Smart Mode that adjusts its temperature and its airflow, so it does not overdry the material. If you are running a nylon or a resin that is susceptible to overdrying, the dryer takes that problem out of your hands and maintains good product.”
Overdrying can occur during production delays when the dryer continues to run. It could damage resin and make it unusable.
“Smart Mode is a very useful feature, especially when you consider all of the various engineering grades of resin we process in both a sampling and short-order production mode,” Moyak said. “It protects our material and the drying process by reducing the dryer temperature if it senses material is not being used.”
MicroWheel dryers use a solid desiccant wheel rather than loose desiccant beads as the drying medium, which offers several advantages, Zambanini said.
“There are very few dryers on the market that are desiccant wheel, and even fewer that are this small,” Zambanini said. “No bead changes are required with a desiccant wheel dryer because there is no breakdown of the desiccant material.
“Desiccant in bead form is bound in clay. It is not a straight desiccant bead thrown into the tanks. Over time, as you heat and cool the clay, it becomes brittle and breaks down, so you need to change it every year or two. It is another maintenance cost and it causes changes in your dryer performance over time.”
The clay dust in bead desiccant can break down, migrate into the airstream and get into parts being produced, which can cause surface defects, according to Zambanini.
“When it is in wheel form, it is like a fiberglass substrate; it looks like a honeycomb if you hold it up the light,” Zambanini said. “That desiccant is impregnated into the fiberglass substrate, so there is no clay binder, so we can heat and cool continuously without any breakdown of the desiccant media.”
The desiccant wheel dryers have saved Matrix money and improved operations, according to Moyak.
“This is a much more cost-effective approach as we have yet to replace a desiccant wheel, and there are no desiccant beads to replace on a periodic basis,” Moyak said. “We clean our desiccant wheels on an ERP-driven [preventive maintenance] schedule for re-use so the MicroWheel desiccant wheels have become a nearly maintenance-free item, and we are no longer spending large sums of money on replacement desiccant every year. The honeycomb desiccant wheel is much cleaner than beads, which is a source of dust, which is important in our environment.”
The MicroWheel dryers are air-cooled, portable and easy to use, and require only electricity to operate, Moyak said.
“There are no water hookups required and it is highly portable,” he said. “When you move or relocate a MicroWheel dryer from one press to another, there’s no need to disconnect, drain and move water lines. That’s been a key item and a huge timesaver. They have a user-friendly, intuitive interface that is simple to operate. These dryers are easily cleaned, allowing our personnel to quickly work through sample and production orders that require different resins.”
Most similar-sized dryers are water-cooled, which is inconvenient for some users, according to Zambanini. “If you don’t have water available at each machine, you would have to plumb in new lines. These dryers are totally air-cooled, so as long as there is an electrical outlet, you can plug it in anywhere and move it from spot to spot.”
Each dryer has its own cart. An embedded controller can be operated by a remote control that mounts magnetically to each dryer.
“Conair designed and built a portable cart for us. It was designed for ease of portability and includes a material wand holder,” Moyak said. “The cart’s footprint is slightly larger than the dryer, so it protects the dryer at all times during transport.”
Moyak said he is pleased with his working relationship with Conair and with the company’s desiccant wheel dryers. “In addition to future MicroWheel purchases, we also anticipate adding Conair’s Carousel Plus desiccant wheel dryers to serve our larger-tonnage presses.”
Bruce Adams, senior staff reporter
Contact: Conair Group, Cranberry Township, Pa., 724-584-5500, www.conairgroup.com
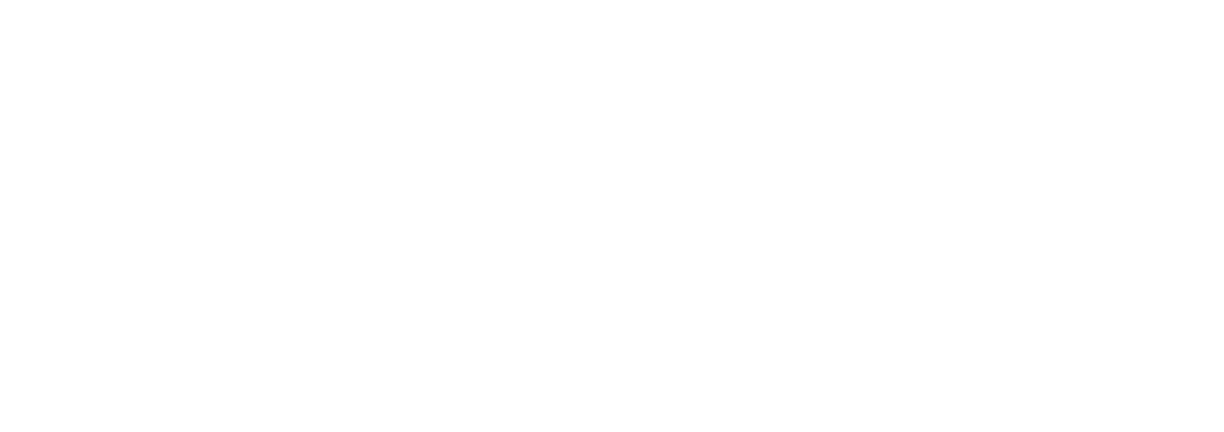