The systems will hit the world market next month at K 2019 in Düsseldorf, Germany. Each autonomous dryer has its own hopper and Industry 4.0-capable PLC capable of storing up to 200 drying recipes. Depending on desired throughput and other user requirements, the individual modules can be combined into an interconnected system with a central display and controller.
As standard, the RDF modules dry resins at temperatures ranging from 140 degrees Fahrenheit to 284 degrees Fahrenheit. However, an optional upgrade allows them to dry high-temperature resins at temperatures of up to 356 degrees Fahrenheit.
The modules are available with hopper volumes ranging from 50 liters to 400 liters.
The modules’ compact design makes installation simple and saves space, the company said. In addition, compared with a central drying system, the RDF system does not require extensive supply- and return-air piping. If requirements change, modules can simply be added or removed.
The dryers use desiccant to remove moisture from the resin. Drying air volume is automatically adjusted to accommodate the actual resin throughput, while regeneration cycles are controlled based on the water content of the pellets and desiccant.
“The special design of this single-tower desiccant allows very short regeneration times (less than 15 minutes), and under full capacity, it is only necessary to make one regeneration cycle per hour,” said Manfred Horsch, ProTec’s head of sales. “Together, with a system that will calculate the water content inside the desiccant material, it will only regenerate when the water content is within an optimum level. The cycles of regeneration will be adapted to the initial water content of the polymer.”
Because each drying module generates its own dry air, it can operate independently and not rely on one big unit to generate the air for distribution to the single hoppers.
“That means if there is a breakdown of the central air generator [in a typical central drying system], all linked units will stop operation,” Horsch said. “This will not happen with the new RDF.”
In addition, since each RDF module generates only the air that is required for a particular application, it can save on energy costs.
“There will be significant energy savings compared to huge single-unit air generators,” Horsch said.
Bruce Geiselman, senior staff reporter
Contact:
ProTec Polymer Processing GmbH Bensheim, Germany, 49-6251-77061-0,
Bruce Geiselman
Senior Staff Reporter Bruce Geiselman covers extrusion, blow molding, additive manufacturing, automation and end markets including automotive and packaging. He also writes features, including In Other Words and Problem Solved, for Plastics Machinery & Manufacturing, Plastics Recycling and The Journal of Blow Molding. He has extensive experience in daily and magazine journalism.
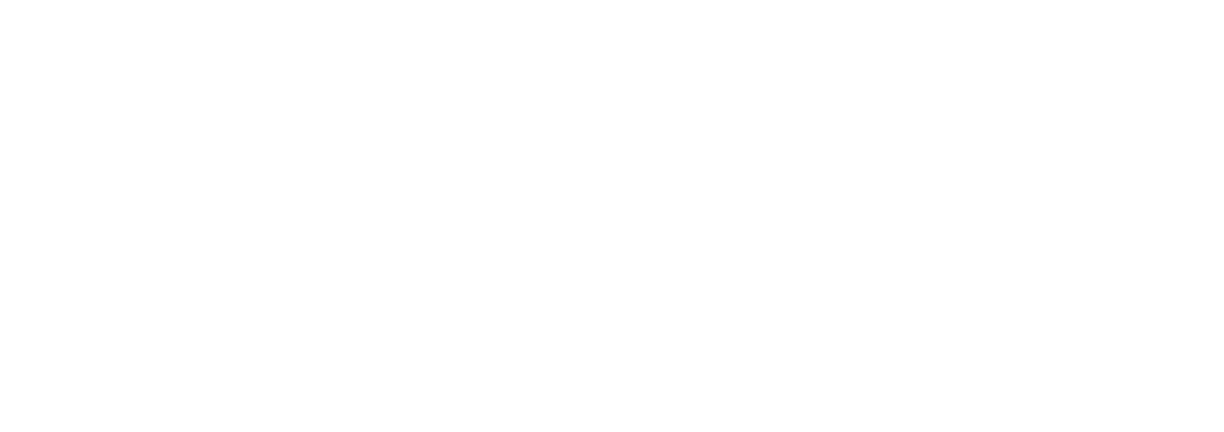