Plastics processors can turn to a variety of dryer technologies for removing moisture from resin prior to manufacturing plastic parts.
Too much moisture can cause cosmetic problems, like streaks, or harm mechanical properties.
One of the principal considerations when selecting a dryer is the types of resin that need to be dried, according to Conair, a dryer manufacturer.
There are two major classes of polymers: non-hygroscopic and hygroscopic.
Non-hygroscopic resins do not tend to absorb moisture. When exposed to moist conditions, non-hygroscopic resins tend to accumulate only surface moisture, which is not a concern for most applications. Drying needs are minimal, and even the simplest type of dryer technology, such as hot-air drying, may be sufficient.
On the other hand, hygroscopic resins are far more difficult to dry and typically need a more efficient drying technology, such as desiccant drying.
Hygroscopic resins require a dryer that heats each pellet completely, breaks the moisture-polymer bonds, drives the moisture to the pellet surface and carries away the moisture.
Dryer types
Processors can choose from six major technologies: hot-air dryers, twin-tower desiccant dryers, wheel-type desiccant dryers, compressed-air dryers, infrared dryers and vacuum dryers.
Hot-air dryers are the most basic. They heat ambient air and blow it to the bottom of a drying hopper. The air rises through the plastic pellets in the hopper, and surface moisture evaporates into the air and is carried away. Hot-air dryers are generally used for drying non-hygroscopic resins. They are not as reliable as other technologies for drying hygroscopic resins to the level required for processing, according to Conair. The performance of hot-air dryers varies depending on ambient relative humidity.
Twin-tower desiccant dryers remove water molecules by passing air through a molecular-sieve desiccant that reduces the dew point to a very low level. Today, the industry standard is a dew point of minus 40 degrees Fahrenheit, Conair said. Next, the low-dew-point air is heated to a drying temperature specified by the resin manufacturer (usually between 150 degrees and 375 degrees Fahrenheit), which further increases the desiccant’s moisture-absorbing capacity. With twin-tower desiccant dryers, both towers contain desiccant. One tower is used to dry the resin, while the other tower is regenerating — drying out the desiccant for the next cycle.
Wheel-type desiccant dryers rely on a continuously rotating wheel made of a fiberglass substrate impregnated with desiccant. Thousands of small air channels allow process and regeneration air to flow past the desiccant. While most of the wheel is used to dry the process air, the rest of the surface is undergoing regeneration and cooling. Desiccant-wheel dryers offer superior, repeatable performance in a more energy-efficient fashion, Conair said. Regeneration temperatures can be significantly less than those required for tower dryers, and their lower mass of desiccant reacts more quickly, allowing for fast startups and precise dew-point control.
Compressed-air dryers are less complex and easier to maintain than desiccant dryers. They use a conventional drying hopper, but instead of recirculating the drying air in a closed loop, they use compressed air in an open loop. A plant compressor compresses ambient air to about 100 psi, which condenses some water vapor out of the air. The effectiveness depends on the humidity in the ambient air. Optional membrane filters can be added to physically remove water molecules from the compressed air before it flows into the hopper. A system that includes membrane filters typically can produce a dew point of minus 40 degrees Fahrenheit or lower.
Infrared dryers are less common because of their relatively high cost. However, they have distinct advantages in certain applications, such as drying PET regrind that will be used to produce sheet or bottles. Infrared heat dries and crystallizes the resin at the same time, and it does so in a fraction of the time it takes a conventional desiccant dryer and separate crystallizer, Conair said.
Infrared dryers have a large, horizontal rotating drum that is fitted with infrared lamps that heat the resin and drive off the moisture as pellets flow through the drum. Ambient air flowing through the drying chamber carries away the moisture and dust coming off the pellets.
Vacuum dryers extract air from a sealed container to draw moisture out of resin pellets. The main attraction of vacuum dryers is speed. Material cycles through a vacuum-drying process in about 40 minutes.
Vacuum dryers use small canisters that rotate through three positions. In the first position, heated ambient air warms the resin for about 20 minutes. In the second position, a vacuum draws moisture out of the pellets. The third position is for retention of the dried material.
The effectiveness of vacuum dryers depends on the moisture level of the ambient air. For example, on a humid summer day, resin would be more effectively dried in an air-conditioned plant than in a non-air-conditioned plant.
Bruce Geiselman, senior staff reporter
Contact:
Conair Group Cranberry Township, Pa., 724-584-5500,
Bruce Geiselman
Senior Staff Reporter Bruce Geiselman covers extrusion, blow molding, additive manufacturing, automation and end markets including automotive and packaging. He also writes features, including In Other Words and Problem Solved, for Plastics Machinery & Manufacturing, Plastics Recycling and The Journal of Blow Molding. He has extensive experience in daily and magazine journalism.
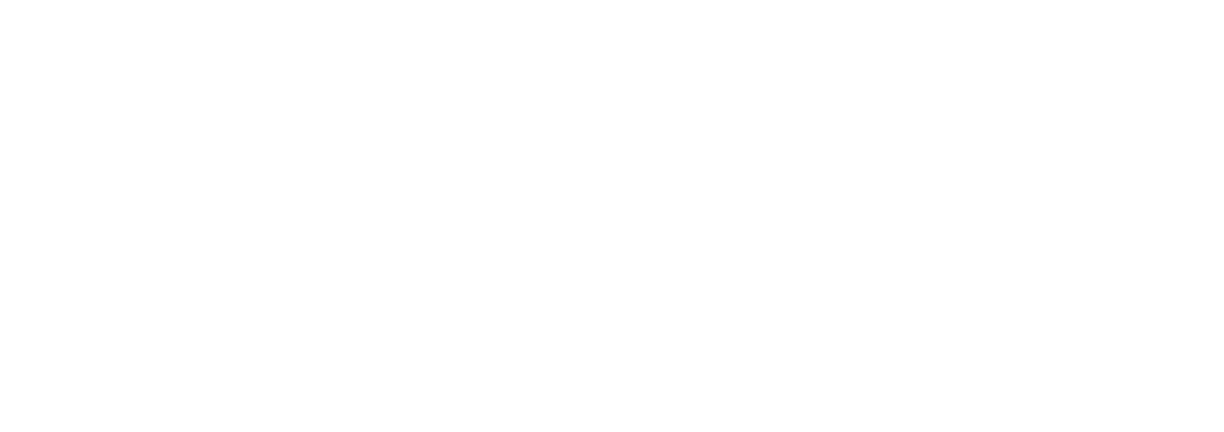