FF-N SERIES
The company’s new FF-N series of servo-electric presses includes seven new models with clamping forces ranging from 135 tons to 500 tons and shot sizes ranging from 2 ounces to 80 ounces. All machines include a small, fully integrated servo-hydraulic power pack to manage mold cores, ejectors and mold carriage movements.
“Our FE series went up to 290 tons, so the FF-N series will expand our offering through 500 tons, and it will have an integrated servo-hydraulic power unit for core and ejector operation,” said Bill Duff, GM of sales and marketing for Yizumi- HPM. “About 90 percent of our customers who buy our electric machines are asking for a power unit to power the cores. It is a separate piece that we put on or next to the machine to operate the cores.”
The FF-N-series power unit consists of a servo-motor drive and a gear pump.
“It is an on-demand system, so it doesn’t waste energy,” Duff said. “It provides the right amount of oil needed to set or pull the core or do the eject function.”
The FF-N series targets applications that require high levels of repeatability and a faster motion to run the clamp and injection unit simultaneously, he said.
“You can run the screw as you open and close the clamp to reduce the cycle time,” Duff said. “We refer to this as overlapping the cycle. The part’s wall thickness dictates if you can do that.”
Machines in the series operate at high speeds and manufacture parts, such as medical devices, that require thin walls.
“It injects at close to 500mm per second, which is a high-speed fill; it has a new-design clamp module, which is a negative-angle clamp; there are no tie-bar bushings; and it runs on linear guides,” he said. “The clamp is a lot faster than our previous models, so the open-and-close speeds are much quicker, which also improves cycle time.”
PAC-K-N SERIES
The PAC-K-N series for packaging consists of models with clamping forces of 275 tons, 385 tons and 500 tons. The machines can handle shot sizes from 7 ounces to 24 ounces. All the models deliver injection speeds of up to 23 inches per second.
“These machines will let us enter into the packaging market in North America,” Duff said. “They are designed for thin-wall packaging, such as containers for yogurt, cottage cheese and butter. We teamed up with an automation company that does in-mold labeling, so we can do the automation also.”
Customers in this segment of the food packaging industry want a multi-functional machine, he said.
“They want a machine that can do automation and the packaging,” Duff said. “They want a system with a robot and in-mold labeling, so, when it comes out of the machine, it is ready to be filled.”
DP-N MULTI-PRO SERIES
The DP-N Multi-Pro series of two-platen machines can mold multi-material parts with a wide variety of possible material combinations. Different injection units can be combined to inject different materials.
“The Multi-Pro is our term for multi-material machinery, where the material refers to the resin,” Duff said. “It is also known as multi-shot or multi-color. It has multiple injection units. One primary injection unit does a substrate, and a secondary unit will overmold that.”
These machines manufacture products that feature both hard and soft features, such as drill handles, toothbrushes and automotive lenses.
“There are lots of applications for this, and many of them are in the automotive sector,” Duff said. “We won’t hold inventory on this machine. It will be a custom-built product, due to all the combinations of injection units and barrel screws that can be configured.”
As an option, machines can be configured with a turntable. Using servo-direct control, the servo-electric-driven turntable rotates quickly, smoothly and accurately, with a repeatability to within 0.005 degree.
YR-SERIES ROBOTS
“The YR series was introduced in Asia by our parent company a couple of years ago,” Duff said. “They refined and redesigned it to meet the CE and ANSI North American safety standards. We will be able to offer what we call a five-axis robot on any of our machines. Each axis has its own servo drive and motor that continually monitors position, forces and speed. Some robot manufacturers share a drive, but we don’t.”
All the robots use a fully closed-loop control system designed to ensure the accuracy and reliability of movements. They feature intuitive free programming, which allows operators to move an axis by hand to a point and enter that value as a data point of entry, Duff said. A color touch screen with a multi-language menu interface is standard.
“If one of our customers likes the robot and has other branded machines and needs a robot for those machines, we will supply them,” Duff said. “This is being introduced as a complement to our machines, and we will go from there.”
Bruce Adams, senior staff reporter
Contact:
Yizumi-HPM Corp. Iberia, Ohio, 740-382-5600
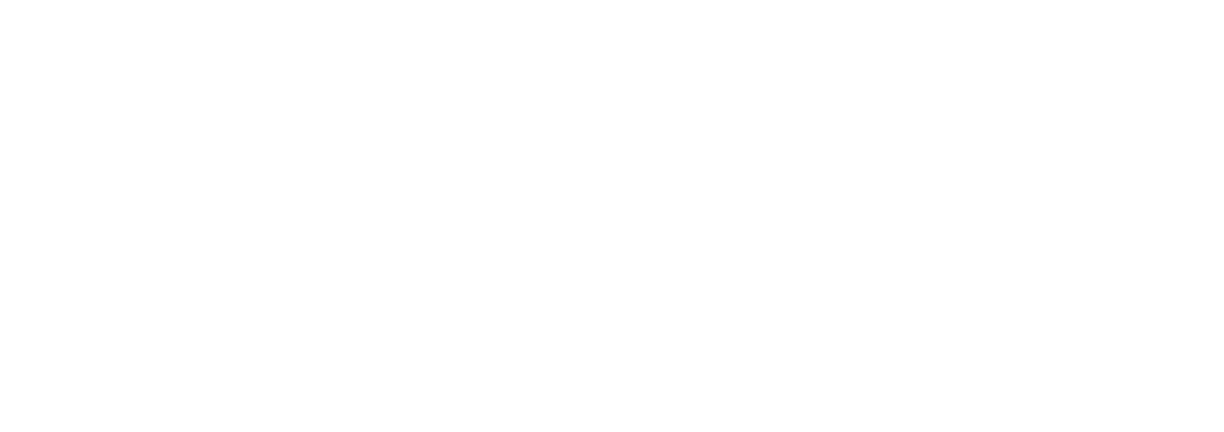