Since its introduction at NPE2018, Syscon International has upgraded its PlantStar 4.0 manufacturing execution system (MES) software. The company added features to help integrate the MES with other software its customers may be using to improve manufacturing efficiency and product quality, and to reduce waste and costs.
“We have long been recognized as having the most processing power on the floor of any of the traditional suppliers through our data-collection module [DCM],” said Gary Benedix, VP of sales for Syscon. “The DCM has the ability to gather production and process data from any device on the factory floor, as well as from central water and drying systems and the overall molding environment, such as ambient temperature and humidity levels.”
The DCMs — industrial computers that capture cycle information from thermocouples, transducers and other sensors embedded in manufacturing equipment — are installed to send information to PlantStar 4.0 software for monitoring production and optimizing output. However, recent developments in the software allow for better sharing of that information with other types of manufacturing software.
“We are expanding our role as the central hub for factory data to feed other enterprise systems,” such as computerized maintenance management systems (CMMS), enterprise resource planning (ERP) systems, quality management systems (QMS), product life cycle management systems and warehouse management system software, Benedix said. “We now have the ability to push data to those systems in real time at the conclusion of each cycle of the machine. This enables those systems to update in real time and provide operational management up-to-date information on material inventories, part quality data, maintenance and warehouse details and more.”
Syscon recently implemented this type of real-time data sharing with a JD Edwards ERP system for a major customer that wanted real-time ERP information from about 1,000 machines in its manufacturing operation, Benedix said.
“Our expectation is it will allow customers to purchase resin, bags and boxes on a more [just-in-time] basis,” he said.
Syscon also is developing a means by which other software systems will be able to pull data directly from data-control modules using the OPC-UA communication protocol.
“This is a big asset for real-time big-data analytics for trend analysis and machine learning,” Benedix said. “Additionally, our new release of software includes many utilities for management to create their own KPI [key performance indicator] charts and reports to better operate their factories.”
“We are greatly expanding our process variable monitoring, alarming and charting, as well. The system also includes expanded mobility with a military-grade mobile HMI tablet we now offer to our customer base,” Benedix said.
For Syscon customers that do not have a separate CMMS, Syscon now offers a tool-tracking function in PlantStar 4.0 that records historical use of tooling and allows a customer to document service work done on tools and the amount of time dedicated to those tasks.
The additional tool-tracking function in PlantStar can help smaller manufacturers that do not want to invest in a full CMMS to keep track of performed and needed maintenance, he said.
Bruce Geiselman, senior staff reporter
Contact:
Syscon International Inc. South Bend, Ind., 574-232-3900,
Bruce Geiselman
Senior Staff Reporter Bruce Geiselman covers extrusion, blow molding, additive manufacturing, automation and end markets including automotive and packaging. He also writes features, including In Other Words and Problem Solved, for Plastics Machinery & Manufacturing, Plastics Recycling and The Journal of Blow Molding. He has extensive experience in daily and magazine journalism.
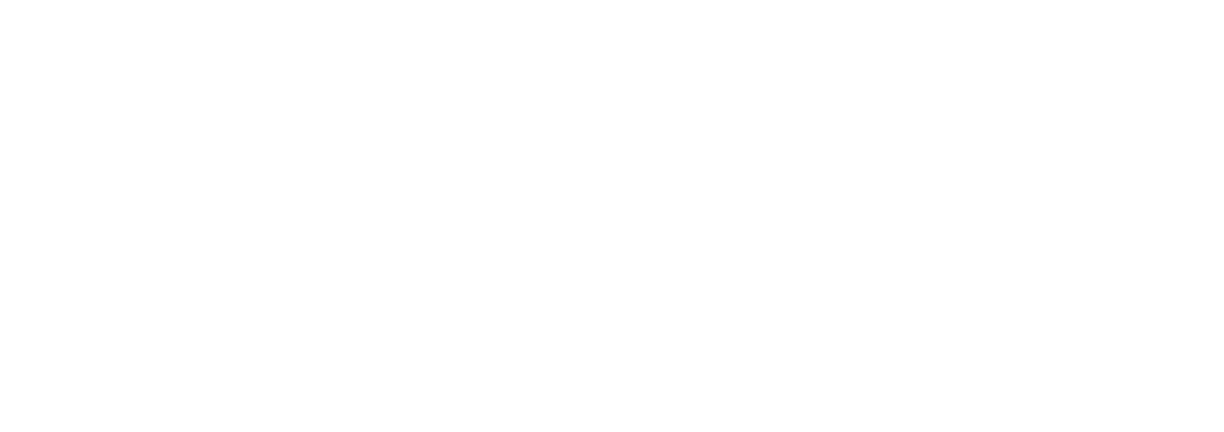