Problem: Forklifts were inefficient and posed safety hazards for workers at one molding plant.
Solution: A mobile robot transports finished parts, eliminating pallet clutter and reducing forklift traffic.
A robot that steers itself has improved safety for workers at a Noblesville, Ind., custom molder.
Family-owned Metro Plastics deployed an MiR200 autonomous mobile robot from Mobile Industrial Robots (MiR) shortly after opening its new 72,000-square-foot facility in March. The plant, which has 25 injection molding machines with clamping forces ranging from 15 tons to 700 tons, uses the robot to transport finished products to the quality-assurance department.
President Ken Hahn said the robot has allowed Metro Plastics to quickly identify and address quality issues, which helps reduce waste and improve competitiveness.
“We always wanted an automated guided vehicle (AGV) for product movement,” Hahn said. “We studied how to implement AGVs in new building design, but you need to install wires in concrete. Then we became aware of this autonomous robot, which doesn’t require wires embedded in concrete. Another advantage is that autonomous robots cost half as much as the most expensive AGVs.”
The list price of the MiR200 is slightly less than $40,000, said Ed Mullen, VP of sales for the Americas for MiR, a Danish company that recently was acquired by Teradyne, North Reading, Mass.
The flexibility of the MiR200 was key to its use at Metro Plastics, Hahn said.
“We have 500 different molds owned by our customers, and our average job runs for about 2.4 days, which doesn’t give us a lot of opportunities to automate production,” he said. “We had to look at other areas of our processes to automate, such as material handling.”
HOW IT WORKS
The robot, which can carry up to 440 pounds, moves finished goods from press operators to quality-control inspectors in the warehouse. When its work is done, the robot automatically docks into its charging station and waits for its next round of activity in a facility that runs 24/7. The process has evolved over time.
“Initially, we set the robot up to loop the factory floor every 10 minutes,” said Emma Morris, a project coordinator at Metro Plastics who programs the robot. “It would stop at each press for 30 seconds so the operator could load the parts.”
Since then, Morris has reprogrammed the robot so that it is on call. Metro Plastics refers to this as Phase 2. It involved adding iPads at each machine, allowing operators to summon the robot to make a pickup. Operators manually load boxes of finished products onto the robot.
The company is working to implement Phase 3, which would involve the robot loading and unloading the boxes.
“After Phase 3 is successful, we think we will be able to interface the Yushin robot on the press and the MiR200 robot,” Hahn said. “As parts are finished and the mold opens, we will need to build tooling to remove the parts from the machine and put them in a box.” Currently, 20 of the company’s presses are equipped with Yushin robots for part removal.
BENEFITS OF THE MIR200
With the MiR200’s arrival has come a number of other changes, Hahn said.
“Before we started using the robot, we had pallets stacking up on the factory floor that had the potential to be tripping hazards,” he said. “We were able to eliminate that issue.”
The robot also has improved worker safety by virtually eliminating forklift traffic on the manufacturing floor. Consequently, the company was able to switch from propane-powered forklifts to electric models, which are cleaner and safer, Hahn said.
“Since we operate 24/7, electric fork trucks weren’t a good option because you need more electric trucks due to their frequent charging cycles,” Hahn said. “We are still operating 24/7, but, since the robot does all the material handling, we were able to get rid of three propane fork trucks and replace them with three electric fork trucks” that are used less frequently.
The robot also has streamlined production, he said. The MiR200 never takes a break or misses any workdays, so pallets are always delivered promptly to quality-assurance inspectors. If they notice any problems, inspectors can notify press operators immediately so that they can take corrective action.
PROGRAMMING AND MAINTENANCE
Automation distributor Neff Engineering, Indianapolis, which has had a long-time business relationship with Metro Plastics, introduced Hahn to the easy-to-use MiR200.
“I spent one-half day training with Neff Engineering to learn how to program the robot,” Morris said. “The robot has built-in scanners and is easy to program. I had to scan the building manually with the robot by driving it around the floor, which took about 20 or 30 minutes. Then it took about two or three hours to program. Neff Engineering wasn’t even here one full day to train me, and we were up and running the same day.”
If there are changes on the factory floor, such as the addition of new injection molding machines, the robot would need to be reprogrammed. Because it has laser sensors, the robot can avoid obstacles and maneuver around people.
Morris said she has software on her smartphone that lets her adjust the robot from remote locations.
The robot is easy to maintain.
“I wipe it off every couple of weeks,” Morris said. “We have not had to lubricate it or change any wheel bearings. It has been maintenance-free.”
The robot has never been out of service and its battery charge has never dropped under 85 percent, Hahn said.
“It works about 30 percent of the time while the plant is running,” Hahn said. “It plugs itself into the charger and charges when it’s not in use. We are only using 30 percent of its capacity, so we are a long way from needing another one.”
Bruce Adams, correspondent
Contact:
Metro Plastics Technologies Inc., Noblesville, Ind., 317-776-0860, www.metroplastics.com
Mobile Industrial Robots Inc., Holbrook, N.Y., 631-675-1838, www.mobile-industrial-robots.com/en
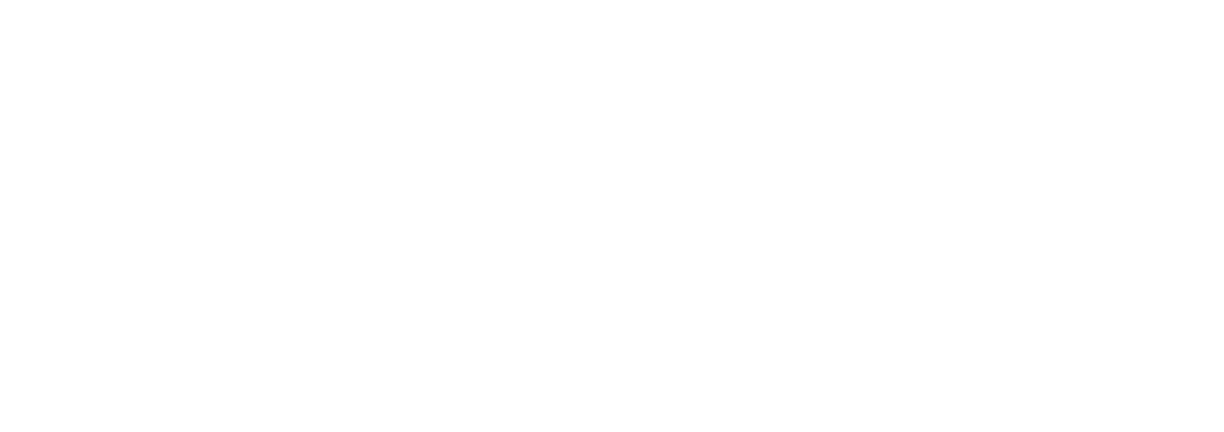