Fakuma provided a view of things to come with a sneak-peek release of a rotary-table injection molding machine series from Wittmann Battenfeld. At the October show in Germany, Arburg, Sumitomo and Boy also stepped out with new versions of existing injection molding machines. The new models offer a range of benefits, including energy efficiency, versatility and speed.
WITTMANN BATTENFELD
Wittmann Battenfeld unveiled its VPower R line of rotary-table machines. The VPower R line is the first of Wittmann Battenfeld's vertical injection molding machines to be based on the company's PowerSeries design. Compared with the existing vertical presses in its product line — the VMR series — the VPower R series is more energy-efficient, precise, compact and user-friendly. Eventually, the new line will replace the VMR series.
Wittmann Battenfeld offers two models of the VPower R, with a clamping force of either 132 tons or 176 tons, and a choice of rotary tables with a diameter of either 51.1 inches or 63 inches. The company plans to add a rotary table with a diameter of 78.7 inches late next year. The new line takes up considerably less space than its predecessors, and its low working height of about 3 feet is convenient for users.
To optimize accessibility to the mold, the machine features the company's innovative two-tie-bar clamping unit, which eliminates the use of a central tie bar. The clamping unit is equipped with two fast-stroking cylinders that are hydraulically driven.
A servo-electric drive controls the rotation of the table. The servo-drive ensures short rotation times and accurate positioning of the table. The smaller table rotates 180 degrees in 1.4 seconds and the larger table rotates 180 degrees in 1.9 seconds.
The rotary table can operate as an oscillating, two-station unit or as a rotary two-, three- or four-station unit. The tie-bar-less rotation center leaves ample space under the rotary table for connections for cooling water, hydraulic oil, compressed air and power, according to the company. These connections can be directed to the mold through the center of the rotary table, either with direct tubing or with an oscillating or rotary distributor, the company said.
For the machine series, Wittmann Battenfeld developed a new compensation plate system that ensures the uniform transmission of clamping forces to the mold.
Molders using the new machines can change the position of the injection unit from vertical to horizontal. In addition, the VPower R is equipped for operation with an add-on injection unit so it can be used as a two-component machine. The second injection unit can be retrofitted to the unit later, if the connections have been installed.
A servo-hydraulic twin-pump system drives injection and clamp movements and enables parallel movements of the clamp and the mold ejector strokes.
Wittmann Battenfeld's Unilog B8 controller, which has Windows 10 IoT installed, controls all machine operations. The company's Industry 4.0 connectivity software, called Wittmann 4.0, is incorporated into the machine control and can be used as the basis for safe, easy integration of equipment inside a production cell.
Wittmann Battenfeld said the new line's open design makes it suitable for the integration of automation systems for insert feeding and finished parts removal.
VPower R machines will be available in the U.S. late next year.
ARBURG
Arburg introduced a packaging version of its Allrounder 820 H machine with a new clamp design. The machine also has an updated, more powerful injection unit. Like all Allrounder H machines, four digital assistance packages that provide set-up and operating guidance are standard.
The new version's biggest advantage is its short cycle times. At Fakuma, it produced an in-mold-labeled, 15.7-gram, rectangular container made from PP in a four-cavity mold in a cycle time of 3.8 seconds. An IML system from H. Müller-Fabrique de Moules SA, Conthey, Switzerland, inserted the labels, removed the finished parts and stacked them on a conveyor belt.
Featuring clamping forces from 280 tons to 730 tons, the Allrounder H series combines a servo-electric clamping unit with a servo-hydraulic accumulator injection unit; the "H" in the name indicates that the machines are hybrids.
The machines combine the speed and precision of an electric drive with the power of a hydraulic system.
The newest version has tie-bar spacing of about 32.3 inches by 32.3 inches and a maximum clamp stroke of about 29.5 inches. Its five-point toggle clamp delivers 415 tons of clamping force. The machine incorporates a 45.4-ounce injection unit with new adaptive valve technology that ensures the injection flow volume is uniform. It allows for maximum injection speeds of about 19.7 inches per second.
As standard, the Allrounder 820 H packaging machine version comes with Arburg's 4.set-up and 4.start-stop digital assistance packages, which simplify machine setup and production startup; 4.production, which simplifies the programming of complex operations and movements; and 4.monitoring, which provides process and quality monitoring.
Two other digital assistance packages remain optional: 4.optimization for improved part quality and reduced unit costs and 4.service for online support.
SUMITOMO
Sumitomo has launched a compact, high-speed version of its IntElect series of direct-drive, all-electric injection molding machines.
The new IntElect S series has models with clamping forces from 50 tons to 198 tons, with injection speeds of between about 13.8 inches to 19.7 inches per second. The high-speed units offer cycle times of 3 seconds to 10 seconds.
Compared to standard IntElect presses, the high-speed IntElect S machines feature an optimized configuration of motors and drives. They are designed to outperform standard IntElect machines in terms of mold movements, injection and metering speeds and ejector movements, resulting in significantly reduced overall cycle times.
Machines in the IntElect S series employ high-torque, direct-drive motors specially developed by Sumitomo for precision and energy efficiency. The IntElect S line features a toggle-clamp design and Sumitomo Demag's NC5 controller.
During Fakuma, Sumitomo premiered an IntElect S 130/520-450 producing pipettes in 32 cavities. It featured a package of options especially for clean-room production of medical components.
The demonstration manufacturing cell also incorporated the VarioTip compact automation system with 100 percent camera inspection from Waldorf Technik, Engen, Germany, to sort the pipettes into racks according to the mold cavity that produced them.
BOY MACHINES
To accommodate continuing developments in multicomponent injection technologies, Boy has rolled out the Boy 125 E, its newest and largest horizontal injection molding machine in terms of clamping force. Multicomponent applications require a machine with a larger molding area.
Employing a two-platen locking system, the Boy 125 E generates a clamping force of 137.5 tons, which is 25 percent greater than the previous top model in the line, the Boy 100 E.
The Boy 125 E has tie-bar spacing of about 1.5 feet by 1.4 feet. The maximum daylight between the moving and stationary platen is about 2.7 feet, while the maximum opening stroke of the platen is about 1.7 feet. Despite the upsized molding area, the machine is compact, with a footprint of about 56 square feet.
E-series machines are hybrid models that incorporate a servomotor pump drive. Compared with machines with electronically controlled, fixed-displacement pumps, the series uses about half the energy, or less.
Boy also offers a servo-electric screw drive as an alternative, which allows it to overlap injection and clamping movements. Such a strategy can reduce cycle times by as much as 30 percent. The servo-electric screw drive can further reduce energy consumption by more than 30 percent.
The new model has an injection unit that can accommodate injection screws with diameters of 1.1 inches, 1.26 inches, 1.4 inches, 1.5 inches, 1.65 inches and 1.89 inches and generate a maximum material flow of about 12.2 ounces per second.
Boy's Procan Alpha controller handles all machine operations. Boy said the new machine, which made its world premiere at Fakuma, will be available globally in the spring.
At Fakuma, a Boy 125 E and a Boy 2C S injection unit were producing two-component cups. The Boy 125 E molded the cup body. A Boy LR 5 robot repositioned the intermediate part in another cavity within the same mold where it was then overmolded with resin from the Boy 2C S. The LR 5 robot removed the finished, two-component part, placing it on a conveyor belt that was located within the protective housing of the LR 5 automation cell.
Mikell Knights, senior staff reporter
Contact:
Arburg Inc., Rocky Hill, Conn., 860-667-6500, www.arburg.com
Boy Machines Inc.,
Exton, Pa., 610-363-9121,www.boymachines.com
Sumitomo (SHI) Demag Plastics Machinery North America Inc.
Strongsville, Ohio, 440-876-8960,www.sumitomo-shi-demag.us
Wittmann Battenfeld Inc.,
Torrington, Conn., 860-496-9603,www.wittmann-group.com
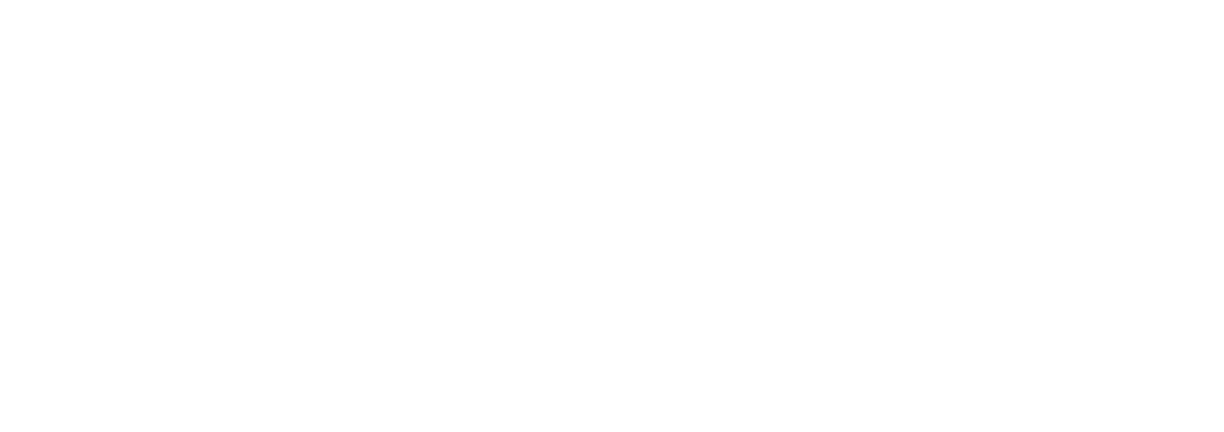