The unemployment rate for plastics and rubber companies in April was 0.1 percent, a huge drop from a high point of 17.1 percent in April 2009.
What does that mean to a plastics processor with a Help Wanted sign in front of the plant?
After all, the unemployment rate for plastics and rubber companies was high during the recession of 2007-2009 and the COVID-19 recession in 2020. But the unemployment rate has been falling since October 2020.
The average rate from April 2009 until April 2023 is 5.9 percent.
“It is unlikely that we will see a significant increase in unemployment when the economy reaches the trough of the business cycle,” Pineda said.
He said that a potential recession in the near future probably cannot be solely attributed to a specific plastics industry end market, as was the case in the housing market crash in 2008-2009.
Pineda said his analysis shows that the surge of uncertainty during March and April 2020 caused by the COVID-19 pandemic was related to the loss of 17,680 jobs in plastics and rubber manufacturing companies. In addition to COVID-19, domestic migration, wage differentials and regulatory and policy responses contributed to higher unemployment.
If you have a Help Wanted sign planted in front of your plant, you are not alone. Plastics and rubber companies are continuing to hire workers. Your task is more difficult than ever before because manufacturers in all sectors are also hiring from the same labor pool.
“As the economy adjusts to its long-term growth rate, reaching the trough of the business cycle may not resemble recessions of the past,” Pineda said.
The Federal Reserve has indicated it may need to raise interest rates one or two more times to reach its inflation target. But Pineda said a jobless recovery is possible and adjustments by the Fed will create jobs.
“However, it is improbable that employment in plastics and rubber products manufacturing will persist at unsustainably low levels, such as those witnessed in April and May of this year,” Pineda said.
Here is another interesting assessment of manufacturing employment. Joe Campbell, senior manager for strategic marketing and applications development for Universal Robots, has been saying for the past couple of years that manufacturing has a demographic problem, not an unemployment problem.
“Baby boomers, we’re retiring at the rate of about 10,000 a day,” Campbell told PMM Senior Reporter Karen Hanna in this month’s In Other Words interview. “And, in the manufacturing sector, we’re just not doing a good job of attracting millennials, Gen Xers and Gen Zs. There’s going to be continued pressure on the manufacturing job market for decades.”
Give machinery makers credit
A recent announcement from Engel reminded me of the important role plastics machinery manufacturers are playing in advancing technology to reduce harmful emissions.
Engel is developing an interesting tape sandwich technology with Austrian firm KTM Technologies. The tape sandwich story is about a motorcycle seat base, but the process can be widely expanded to other products.
The tape sandwich process uses very thin, single-layer reinforcement materials such as tapes and fabrics with a PP matrix. They are inserted into both halves of the injection mold without preheating before the cavity is filled with PP.
The numbers are interesting. Engel said the resulting motorcycle seat base is 66 percent thinner and weighs 26 percent less than the current production model. It is also cheaper to produce.
Here are some numbers that are even more important: Engel said the tape sandwich seat base reduced the global warming potential by 27 percent when using fossil PP and by 85 percent when using PP from renewable sources. Engel said the single-grade plastic design helped reduce greenhouse gases.
We often credit resin manufacturers for their research and development successes but in this case, Engel has pushed forward a processing technique that is better for parts makers and the planet.
Ron Shinn, editor
Ron Shinn | Editor
Editor Ron Shinn is a co-founder of Plastics Machinery & Manufacturing and has been covering the plastics industry for more than 35 years. He leads the editorial team, directs coverage and sets the editorial calendar. He also writes features, including the Talking Points column and On the Factory Floor, and covers recycling and sustainability for PMM and Plastics Recycling.
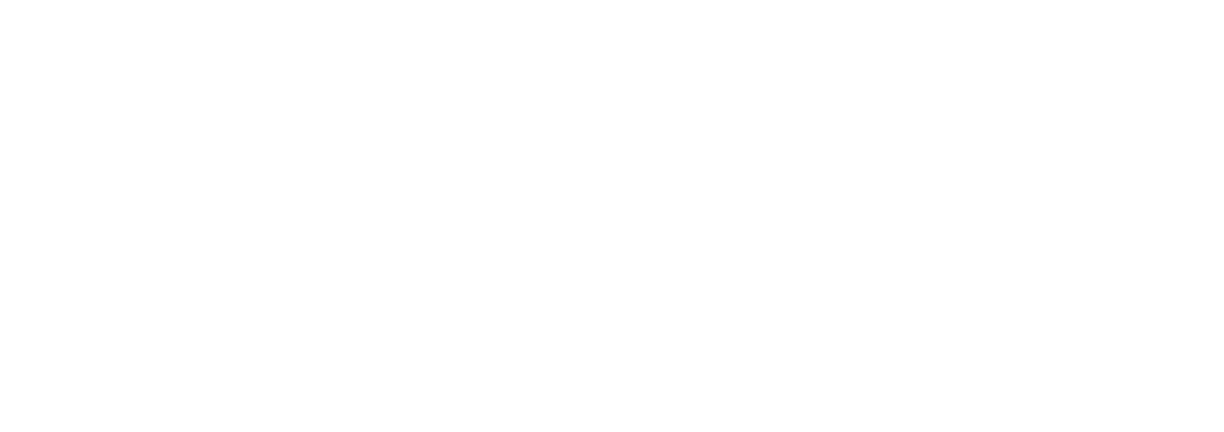