By Karen Hanna and Bruce Geiselman
Yizumi-HPM Corp. builds in a little cushion when it comes to setting timelines for jobs.
Lately, it’s needed the extra breathing room, as it and other plastics machinery OEMs deal with backlogs at international ports of exports and imports, finished goods and parts for assembly.
“Certainly, we’re seeing the ports of entry, especially on the West Coast, have been backed up. It just takes some time. We just recently brought in a whole bunch of machine parts, and it typically took an additional two weeks to get those delivered because of delays at port,” said Bill Duff, GM of sales and marketing of Yizumi/HPM, Iberia, Ohio.
After a year of austerity created by the pandemic, the volume of goods now being processed caught everyone off-guard, according to a presentation provided by Nils Haupt, senior director of corporate communications for Hapag-Lloyd AG, a major shipping company based in Hamburg, Germany. The volume has increased 20 percent, putting significant pressure on companies already dealing with limitations on the number of workers allowed on-site due to COVID-19 protocols.
Hapag-Lloyd's presentation provides a snapshot of the problem: delays of 5 to 7 days at some major ports in China; 2 to 6 days at the ports of New York and Savannah, Ga.; and upwards of a week at the ports of Los Angeles and Long Beach, Calif. Adding to the problem is the fact that, as containers sit waiting to be unloaded, there are not enough empties to ship out. Due to the pandemic, production of new containers fell 40 percent in 2020, compared with the previous year.
It all adds up to the “the worst ‘operational crisis’ our industry has seen for many years,” the presentation states.
Sonny Morneault, VP of sales for Wittmann Battenfeld USA, Torrington, Conn., reported “severe delays, lost freight and difficulty in booking availability,” affecting both domestic and international deliveries. In addition to ship cargo, air freight also has been affected, he said.
“Delays at the ports have been caused by ports being short-staffed, customs quarantines and waiting for containers,” he said.
Ocean Network Express (ONE) Pte. Ltd., a Singapore-based shipper that says it operates the world’s sixth-largest fleet, acknowledged the issues. Shiori Harada, who works in planning, administration and communications for the company, blamed a sudden spike in demand as the global economy bounces back a year into the pandemic. Congestion at the ports has been compounding.
“For example,” Harada said in March, “more than 40 ships are waiting at the anchorage for berthing in the port of Long Beach. And inland logistics, including trucking, rail and warehousing, do not have enough workforce, and their efficiency is far from their full rate.”
According to Hapag-Lloyd, many ship sailings had to be canceled in February and March because of bottlenecks at the ports. And this was even before the grounding of the Ever Given cargo ship in the Suez Canal further complicated the situation.
The problems have created weekslong delays for Anyang, South Korea-based LS Mtron, a maker of injection molding machines distributed in the U.S. by Daiichi Jitsugyo (DJA). Part-sourcing has been delayed about a month, according to information provided by Peter Gardner, GM and VP of sales for DJA.
He broke down how lead times have changed by press size: from 2.5 months to 3 months for presses with clamping forces 20 tons to 440 tons, and from 3 months to 4 months for presses sized 500 tons to 1,200 tons. Lead times for the biggest presses remain unchanged.
According to information provided by Gardner, the shipping time to the U.S. used to be about 1 month, but now averages 6 to 7 weeks.
Issues are evident across the plastics industry, said Glenn Frohring, a co-owner of Absolute Haitian. The China-based company has several locations in the U.S., including Worcester, Mass.
“We have seen Long Beach and the inland port of Chicago hit the hardest with delays,” Frohring said.
As the global leader in injection molding machinery sales by unit, the company has the means, experience and capacity to overcome disruptions, he said. Finding containers has been challenging, however.
“We are monitoring this and proactively securing containers in advance of equipment completion dates. We also have a logistics team in North America communicating with our shipping partners and customers on a daily basis during this situation. We use any option available to us to expedite shipments,” Frohring said.
For Absolute Haitian, the establishment of a new facility in May 2019 in Moncks Corner, S.C., was fortuitous.
“We had built up a large stock-machine inventory there, so when the demand for molding machines returned in just a few months, we were able to respond with available inventory, making shipment on the water less of a factor for us. The new operations center turned out to be good timing for us and our customers, especially those that needed machines quickly to manufacture PPE [personal protective equipment] and medical devices,” Frohring said.
Like Frohring, other OEM representatives reported they’re weathering the storm.
“So far, it has only been seven to 10 days delays on our shipments and not too bad of an impact for us and our customers,” said Marko Koorneef, president of Boy Machines Inc., Exton, Pa.
To speed access to parts, LS Mtron has turned to delivery by airplane, rather than ship. It’s also stocking more parts in inventory and sourcing more parts domestically in South Korea, to create a better cushion.
Companies can still move anything anywhere, said Mark Jones, the director of support services for SML North America Inc, Gloucester, Mass., although the routes might be a bit more circuitous.
“We are warning customers that delivery times for spares may be longer than usual, but the reality seems to be that everything is shipping on time,” Jones said.
Hapag-Lloyd and ONE said they’re working to make supply chains move more smoothly by redeploying ships and containers where they’re needed most. Hapag-Lloyd said it’s trying to reroute shipments to less-congested ports, but it warned the disruptions could continue for months, as companies seek to refill low inventory levels amid record demand, fueled in part by governments’ ongoing efforts to pump money into their economies.
“Wherever possible we are seeking to find alternative routings to bypass the most congested terminals with the longest delays — even at higher cost,” the Hapag-Lloyd presentation states.
Karen Hanna | Senior Staff Reporter
Senior Staff Reporter Karen Hanna covers injection molding, molds and tooling, processors, workforce and other topics, and writes features including In Other Words and Problem Solved for Plastics Machinery & Manufacturing, Plastics Recycling and The Journal of Blow Molding. She has more than 15 years of experience in daily and magazine journalism.
Bruce Geiselman
Senior Staff Reporter Bruce Geiselman covers extrusion, blow molding, additive manufacturing, automation and end markets including automotive and packaging. He also writes features, including In Other Words and Problem Solved, for Plastics Machinery & Manufacturing, Plastics Recycling and The Journal of Blow Molding. He has extensive experience in daily and magazine journalism.
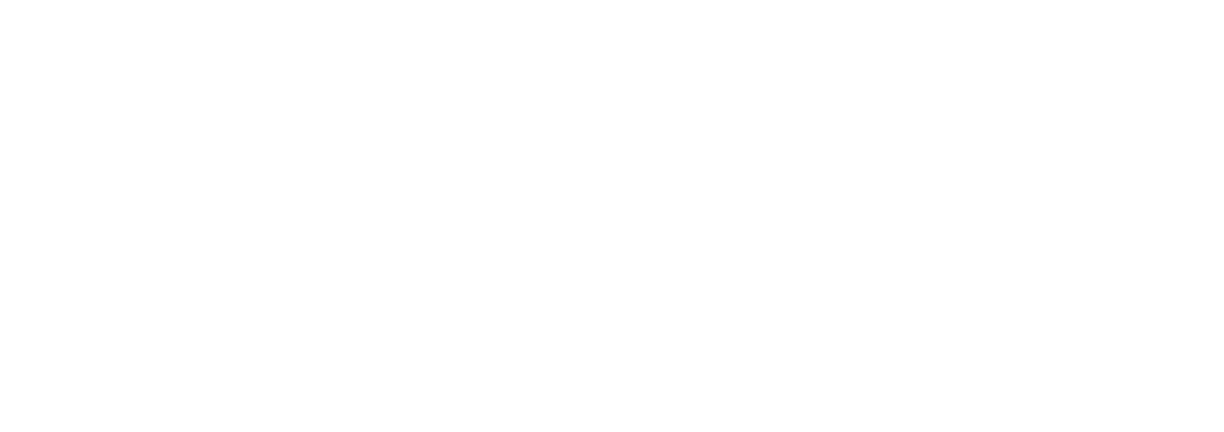