By Ron Shinn
I have always had a vague concept about our nation’s strategic oil supply existing in huge underground caverns filled with crude.
It was an eye-opening experience the first time I visited the Defense Construction Supply Center (DCSC), a sprawling complex near Columbus, Ohio, where personnel procured and stockpiled construction supplies for the military and national emergencies. It looked like a small military base. There was a similar complex in Dayton, Ohio, responsible for electronic equipment; when it was folded in with the DCSC, the Columbus complex’s name was changed to Defense Supply Center, Columbus, its current designation.
So, if we can stockpile oil and nails and radio batteries, why can’t we do a better job with syringes, test tubes and PPE?
The COVID-19 pandemic has shown that medical supplies are as critical in a worldwide medical emergency as are beans and bullets in a shooting war.
It became evident last March that the U.S. was woefully short of many critical medical supplies. In early April, the federal government announced that 90 percent of its stockpiled medical equipment was gone. Blame it on lack of government planning, an inefficient international supply chain — whatever you like. It doesn’t much matter at this point.
The domestic plastics industry quickly pivoted to produce more medical equipment. When the history of the COVID-19 pandemic is written, plastics processors will be near the top of the list of heroes.
For examples of companies that have answered the call, see:Carbon and partners scaling up to produce 1 million swabs for COVID-19 testing
Companies pool knowledge to build better ventilator parts
Making, selling PPE has helped contract manufacturer through pandemic
Reifenhauser converts line to produce PPE
SSI expands capacity to meet testing labs' unprecedented COVID-19 demandBut plastics processors — and the entire U.S. population — would benefit from a national policy of procuring and maintaining much larger supplies of critical medical equipment, and supporting processors’ ability to surge production when needed.
President Donald Trump, in a campaign-style visit to Allentown, Pa., in May, said he planned to replenish the national stockpile of medical equipment and bring manufacturing of critical supplies and equipment back to the U.S.
“These stupid supply chains that are all over the world — we have a supply chain where they’re made in all different parts of the world,” Trump said in an interview on the Fox Business Network the same day. “And one little piece of the world goes bad, and the whole thing is messed up. We should have them all in the United States.”
There is not much evidence that anything has been done thus far. And reshoring the entire supply chain for medical equipment is probably not a very practical idea.
U.S. representatives Tom Malinowski (D-N.J.) and Rosa DeLauro (D-Conn.) in April introduced the Providing Protective Equipment Act of 2020 to improve national stockpiling of critical medical supplies. Some provisions of that bill were rolled into the $2.3 trillion government funding bill that Trump signed Dec. 27.
Included is a requirement that government stockpiles be maintained at a level sufficient for the next national pandemic.
Of course, the devil is in the details. It remains to be seen how that will be interpreted and turned into government practice. The Biden administration needs to make preparing for the next pandemic a priority along with combating the current one.
The plastics industry has a big stake in producing medical equipment, and the Plastics Industry Association (PLASTICS) should be watching closely and stepping into the process as needed. The association has a strong lobbying operation and is well-equipped to do this.
The Council on Foreign Relations published an independent task force report in October. Here are some points worth noting:
The United States and the world were caught unprepared by the COVID-19 pandemic despite decades of warnings of the threat of global pandemics and years of international planning. The failure to adequately fund and execute these plans has exacted a heavy toll on humans and the economy. In the U.S. alone, hundreds of thousands of lives have already been lost.
The pandemic also exposed the nation’s inadequate investment in state and local health systems, many of which were quickly overwhelmed. The failure to maintain an adequate Strategic National Stockpile (SNS) — and to clarify the rules governing its use — led to shortages of essential medical supplies and competition among states over scarce medical equipment.
The U.S. should use incentives to diversify its global supply chains of critical medical supplies and protective equipment for resilience and reliability. This approach could include pursuing emergency sharing arrangements among close U.S. partners and allies and strengthening multilateral regulatory cooperation among major producer nations to ensure common standards and quality control, especially during emergencies.
The SNS should be prepared to address demand surges and shortages during a pandemic, including by careful management of inventory for drugs and equipment routinely sold to health systems through normal distribution channels to avoid the waste associated with letting SNS products expire.
The entire report is available at www.cfr.org/report/pandemic-prearedness-lessons-COVID-19/.
These are all good suggestions, and I hope we are not as unprepared for the next pandemic as we were in 2020 for COVID-19. There is no doubt the plastics industry will play a major role in making sure that does not happen again if there is adequate national leadership.
Ron Shinn, editor
Ron Shinn | Editor
Editor Ron Shinn is a co-founder of Plastics Machinery & Manufacturing and has been covering the plastics industry for more than 35 years. He leads the editorial team, directs coverage and sets the editorial calendar. He also writes features, including the Talking Points column and On the Factory Floor, and covers recycling and sustainability for PMM and Plastics Recycling.
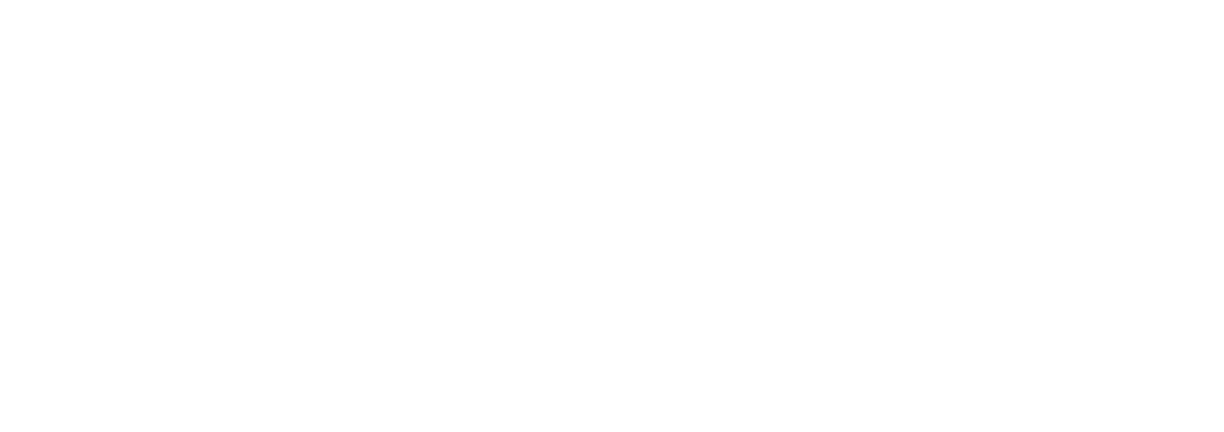