Companies that help plastics manufacturers improve their techniques agree on the fundamentals of process optimization but have their own training courses and tools for attaining it.
Paulson Training Programs and RJG Inc. agree that process optimization centers around four variables — the plastic’s melt temperature, flow rate, pressure and cooling rate. The companies offer different classes, seminars, custom training and other tools to help processors better measure and control those variables.
Paulson Training Programs
Paulson Training was launched approximately 40 years ago by Don Paulson, who traveled nationwide teaching classes about molding principles, according to his daughter Karen Paulson, who’s now the company’s co-owner and president. The company now includes the Paulson Plastics Academy, a division that offers in-person classroom training, custom onsite training and virtual live-streaming classes.
Todd Bryant, senior instructor and consultant for Paulson Training, has spent his entire career in plastics, plastics engineering and plastics processing. In the 1980s, he studied Don Paulson’s published training materials that taught the science behind plastics processing.
“Don promoted the philosophy of the four plastic variables: plastic melt temp, plastic flow rate, plastic pressure and plastic cooling rate,” Bryant said. “That is the whole premise that brings forth all the formal training and education in the plastics industry.”
Karen Paulson said some people confuse the four plastic variables and machine settings.
“A lot of people think that the machine settings determine the part property or optimize the cycle,” she said. “That is not true. What determines the part properties or optimizes the cycle are those four plastic variables. Those four variables are controlled by the machine settings. You have to go through those four variables. That is what you are actually optimizing. The machine controls are just a means to adjust them. Those four variables will determine whether you will have a good part, a bad part, or whether your cycle is going to be optimized.”
Whether injection molding, extruding or thermoforming, machine controls influence the melt temperature.
“How is the machine introducing heat, putting the energy to the material, and how do we get feedback on the temperature of the material from the machine?” Bryant asked. “The better machines will have a control system to introduce the heat and complete a closed-loop system to get feedback from the machine.”
Flow rate is another consideration.
“How well does that machine control a flow rate?” Bryant asked. “Processors want feedback to know if they are getting the designated flow rate and they want the machine to control that flow rate.
“Processors also want to know how much plastic pressure the machine put in the cavity each time and get feedback on that. They put heat into the plastic when they flowed it into the mold. Then they had to take the heat back out. How fast they take that heat out of the plastic is the plastic cooling rate. They want to be able to measure that.”
Paulson Training offers SimTech, a web-based molding simulation program that is a mathematical model of the four variables.
“We use SimTech to train people how to optimize those four plastic variables,” Bryant said. “We are using molding machine settings on a molding simulator on a laptop via the Web. It helps students develop the specialized knowledge to control the machine settings to manipulate those four plastic variables to optimize the process.”
SimTech is proprietary software that Paulson Training licenses.
“Airplane pilots use simulation to train to fly an airplane. They can be on the ground and, if they make a mistake on the simulator and crash, there is no harm,” Bryant said. “They reset the simulation. If you make a mistake on SimTech, you crash the mold without doing any physical damage to the mold or machine. It is mathematical-based and algorithm-based, not rules-based. When you click the cycle button, it does 26 million calculations in less than 2 seconds.”
SimTech is based on the science of the plastic, heat transfer and flow dynamics. Students learn how to make adjustments to the heat, the flow rate, the pressures and the cooling times and get real-time outputs.
Paulson Training also offers SkillBuilder, licensed software that’s available online. It is a simplified version of SimTech.
“When somebody is going through an online lesson, at various points, it will stop and tell them to take their SkillBuilder lesson,” Karen Paulson said. “It launches practical examples on a molding machine for them to solve.”
The SimTech lab lesson presents more advanced problems in which students need to apply what they have learned in their lessons to optimize a cycle. SimTech comes at the end of the training course after students. SkillBuilder is taken throughout course lessons to emphasize select training.
Paulson Training offers seven courses year-round, including five on injection molding. They are being offered virtually during the pandemic. The company said it has trained more than 50,000 people.
RJG Inc.
Jason Robinson has been a consultant and trainer with RJG since 2011. He was an RJG customer from 1994 to 2011, when he was a process engineer at Piolax, a Japanese auto parts supplier.
A trend with machine control systems is that they offer more information in a more visually appealing manner and are designed to make the user interface easier to navigate, he said.
“The development of controls goes along with Industry 4.0 and the availability to access information,” Robinson said. “Companies also are providing more ability to integrate through the machine controller to control hot runners, thermolators and other pieces of auxiliary equipment.”
When teaching classes, Robinson said he focuses on the four plastic variables.
“The machines all do the same thing,” Robinson said. “They have different controls with various features and options. We weed through that to the control on any machine. We are looking at optimizing the material prep, the back pressure, the RPMs and the barrel temperature setting. When we are filling the mold, we are looking at the volumetric fill rate and how far we are actually filling the cavity. We look at pack-and-hold pressure and pack-and-hold times and speeds and the cooling times.
“We filter out a lot of bells and whistles that machine makers put on their machines. We are not trying to sell a certain brand of machine. We boil it down to what the machine does and teach them how to use the basics of the machine that all molding machines have.”
Robinson teaches in the RJG facility in Woodstock, Ga. The company is headquartered in Traverse City, Mich., and has a training facility in Gibsonville, N.C., as well as locations in Mexico, Europe and Asia.
“We have seven machines in our lab and most are less than 3 years old,” he said. “Not all our customers have brand-new machines, so we also have a 1998 Nissei with knobs and sliders and a PLC control. They can do the same thing on that machine but with less precision.”
Students can pick from a wide array of training courses, from basic math to advanced molding.
“There is a lot of math in our training, and we used to teach an in-person math class,” Robinson said. “Now, it is online in 40 hours of math instruction. We have a two-day class called Essentials, which is good for people new to the industry.
“We have a relatively new four-day class called Fundamentals of Systematic [Injection] Molding. It is an excellent class, about 50 percent classroom time and 50 percent machine time. It is meant for relatively new people. We teach it using cause and effect.”
Students start at the machine, follow instructions on a spreadsheet, then go to the classroom and talk about the adjustments they made on the machine and what effect the changes had.
RJG’s two-week Master Molder I class is more intense.
“It is a pass/fail class that covers process optimization strategies, machine performance strategy, how to build a process and document it,” Robinson said. “It is eight days of instruction and two days of testing. There are daily quizzes, written finals and graph testing. It teaches how to do basic processing on any brand of machine and performance test the machine.”
Students who earn a certificate in Master Molder I can opt to take a second two-week class, Master Molder II, which is similar to Master Molder I, but taught with RJG equipment.
“We have two areas of our business, the training side and the equipment side,” Robinson said. “The equipment is sensor technology for cavity pressure, thermocouples and exterior hardware that reads and interacts with the machine. Traditionally, it is called the eDART System. We are in the process of releasing a newer version that is called CoPilot. You can sort good parts and bad parts by data from inside the cavity. Students learn how to optimize the process using cavity pressure data to control the machine. It is more focused on building processes using instrumentation, such as cavity pressure transducers and thermocouples, from inside the cavity. It minimizes the variation of part quality.”
This offers molders a highly optimized process.
“If you are running a high-liability part, like a medical application, and you want to control the process and sort out bad parts, and be more confident that you are shipping good products to your customers, you might see more of a benefit of putting the instrumentation in your mold,” Robinson said. “Every shot that is made, the system stores all that data so there is traceability. You can look at that data six months out to see how a part was made. It is similar to scientific molding. We trademarked it as Decoupled molding because we decouple or separate filling and pack and hold.”
During the pandemic, RJG is offering some of its classes online with videos to simulate hands-on instruction.
Bruce Adams, senior staff reporter
Contact:
Paulson Training Programs Inc., Chester, Conn., 860-526-3099, www.paulsontraining.com
RJG Inc., Traverse City, Mich., 231-947-3111, www.rjginc.com
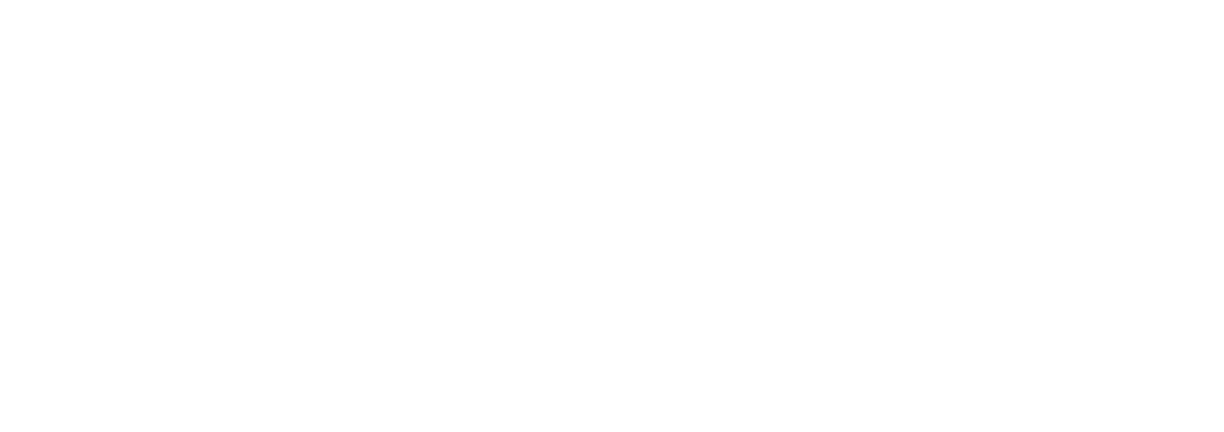