There is also strong interest in in-house recycling equipment as processors who once paid a vendor to take their scrap to a reclaimer or to the landfill are now recognizing its value in their production.
New machinery shown at K 2019 emphasized both of those requirements. The trend will continue, with the Plastics Industry Association announcing that circularity will be the defining feature of NPE2021.
Vecoplan
Vecoplan launched its VIZ line of single-stage shredders, which are designed to be easily adaptable to different requirements.
“Our VIZ series offer a universal solution for all kinds of input materials,” Martina Schmidt, head of Vecoplan’s recycling and waste division, said at a press conference at K 2019. “There are almost no limits when it comes to characteristics, color and form.”
Germany-based Vecoplan showed the VIZ 1300, which has an infeed opening of 4.1 feet wide by 6.1 feet high. A larger version, the VIZ 1700, has an infeed opening that is 5.5 feet by 6.1 feet.
The patented HiTorc drive maximizes torque at low speed. It has no mechanical drive train. The machine can start when fully loaded and runs quietly, the company said.
The patented ESC drive is the most cost-effective option. It offers real-time slippage detection, has self-regulating drive speed and is low maintenance.
Schmidt said the shredder’s design allows for much easier access to internal components so that maintenance, cleaning and blade changes are faster. “With the former generations of shredders, you had to get inside the machine to clean or perform maintenance,” Schmidt said. “Now there is good accessibility.”
A new rotor design uses bolted tool-holder plates with variable cutting-tip sizes. The rotor does not have to be removed to change plates. This design means the cutting geometry can be easily changed with the rotor remaining in the shredder when different output sizes are desired.
If a tool holder is damaged, it can be replaced without welding or removing the rotor.
The rotor on the VIZ 1300 is 1.6 feet in diameter by 4.1 feet long. The VIZ 1700 rotor is 1.6 feet in diameter by 5.5 feet long. The rotor speed is 105 rpm to 265 rpm on the VIZ 1300 and 110 rpm to 280 rpm on the VIZ 1700. Three rotor configurations are available for each machine.
Users also can add a second counter knife, if needed.
Compared with previous Vecoplan models, the VIZ’s cutting chamber has been expanded. The chamber now can accommodate bales, which can be fed directly into the machine. The ram height also has been designed to accommodate full bales and other bulky items.
The screen swings away and can be easily changed, the company said. Users can adjust the size of the output material by using screens with different hole sizes.
The company has upgraded the maintenance panel interface to be more user-friendly. It includes operator prompts, recipe storage, a full user’s manual, video tutorials and the ability to go online to order parts. The panel is accessible via smartphone, tablet or laptop.
Another option is a camera integrated into the hopper. The camera feed is accessible through all devices.
The new panel collects data and displays statistics via an an easy-to-use dashboard. With this information, operators can make adjustments to improve energy efficiency, said Daniel Kessler, who is responsible for electrical development. In addition, the new panel records machine operating parameters and is designed to be protected from vibration and damage.
CEO Werner Berens said it took about a year to develop the VIZ machine.
Herbold
Herbold introduced four size-reduction machines covering a wide range of applications.
The new EWS 60/210 high-performance, single-shaft shredder is designed for dry or wet operations that require high throughput. Herbold said it focused on improving rotor wear protection for the new machine.
“In addition to custom knife configurations, it is equipped in particular with bolted armor plating and a special grinding chamber seal,” said Daniel Zeller, head of sales. This eliminates the time-consuming hardfacing of rotors, he said.
The machine’s throughput is up to 6.6 tons per hour, depending on the material being shredded, drive capacity and screen.
The EWS 60/210 has a low-maintenance, two-sided belt drive and a clutch to prevent damage when uncrushable material is in the shredder.
The drive system employs a countershaft gear. An optional overload coupling is available.
The cutting system uses a rotor with variable knife configurations equipped with screw-on steel plating.
The EWS 60/120 has a rotor diameter of 1.9 feet and a working width of 6.9 feet. The number of rotor knives can vary from 30 to 210. There is one row of stator knives with an option for a second row.
Hydraulic lifts facilitate access to the grinding chamber trough and the screen support.
Herbold also demonstrated a redesigned SMS 80/160 SB granulator equipped with a horizontal feed-screw system for heavy-duty applications.
SMS-series granulators are designed for size-reducing heavy lumps, tough fibers, extremely thin films or very large amounts of material.
“We have accumulated a lot of experience with a couple hundred force-feed granulators,” said Karlheinz Herbold, the company’s managing director. “We used to put a modified hopper on top of the bigger units, but now we have a horizontal feed-screw arrangement for the bigger units like we have for smaller machines.
“This arrangement gives more efficiency because the screws can be located much closer to the rotor since no gap is needed to allow [material] to get access to the rotor.” The ram ensures that material is fed into the knives at a steady pace.
The SMS 80/160 SB with horizontal force feeding shown at K 2019 has a forged, single-piece rotor that is 31.5 inches in diameter by 63 inches long. It can process 5.5 tons per hour.
Herbold said the new design permits easier access to the cutting chamber since the feed-screw body is bolted directly to the housing. That eliminates the need to move the feeding device to tilt the granulator body.
Herbold also debuted a new version of its DWS two-shaft shredder with the stator positioned in the middle. The company said it is suitable for pre-shredding of big bags and large containers.
The DWS 45/160 features a large working surface for the rotor. The granule size is determined by the size of the perforations in the screen.
The feed opening is 34.6 inches by 63 inches with a flanged cover. The hopper is open and designed for direct or conveyor feeding.
The rotor is 17.7 inches in diameter and 63 inches long. It is water-cooled with an anti-wear coating available as an option. It has two rows of 24 stator knives and two rows of 74 rotor knives. The knives are chromium-nickel steel.
The DWS 45/160 is appropriate for dry or wet operation.
Hosokawa Alpine
A compact new unit from Hosokawa Alpine combines a shredder rotor with a granulator rotor in a simple, vertical arrangement that uses gravity to move material.
The company said the new shredder-granulator, called the Polyplex PPC 50/120, works with any plastic material and is suited for in-house recycling.
The machine can handle items up to 19.7 feet in length, and tackle pipe, profiles and trim, as well as machine purgings weighing up to several hundred pounds.
A mechanical feeding unit with an adjustable length feeds material either continuously or in batches into the shredder. The shredded plastic falls from the shredder into the granulator, where it is further reduced in size to approximately 5mm.
The Polyplex unit has six rotor knives and six rows of granulator knives.
Doug Ort, VP and GM, said the Polyplex unit is considerably cheaper than buying separate shredders and granulators. It is also more energy-efficient since it uses only one drive for both shredding and granulating.
He said the vertical design provides easy access to the cutting chamber, granulator knives and rotor, reducing cleaning and maintenance times.
If needed, the unit can be run as only a shredder, Ort said.
Italian manufacturer Tria is replacing its TRK series of granulators with a new series, the XR Series 30, for processing extruded edge trim inline. It showed the first two models of the series at K 2019.
The new series is designed for use with faster extrusion lines, thinner materials and PS, PP, polylactic acid and PET. Tria said the granulators have a redesigned traction unit and rollers that make them ideal for grinding edge trim with slippery or sticky additives in thicknesses of up to 3mm.
The XR 3530 has a single, 12.6-inch-wide traction unit, and the XR 5030 has two traction units that are each 7.5 inches wide.
The speed is adjustable at rates of up to 512 feet per minute, compared with 361 feet per minute for the TRK granulators. Tria said the traction unit’s speed can be synchronized with the production line output.
The company designed the new series with all moving parts inside. This provides easy access for maintenance without requiring that the fixed traction unit be tilted. No tools are needed to access the front and rear sides of the granulator.
The company also has minimized the footprint. The XR 3530 is 3.8 feet wide and 3.1 feet deep; the XR 5030 is 3.8 feet wide and 3.5 feet deep. Both are 3.9 feet high. The base has been redesigned to be lifted by a forklift.
The rotor diameter is 10.2 inches, and both granulators have a speed of 340 rpm. The maximum throughput is 551 pounds per hour.
The traction-unit speed can be set to zero while the accumulator is active to prevent the rollers from slipping, which can cause material to break during reel changes.
The new series offers Industry 4.0 functionality, with the ability to continuously monitor blade wear and temperature during feeding, as well as diagnose problems. Remote access to data is available.
To save energy, the granulators go through a sequential automatic shutdown during prolonged periods with no material input.
Pure Loop
Pure Loop GmbH, a sister company of Austria’s Erema Group, has developed a high-throughput version of its ISEC evo shredder-extruder combination, which can be used inline to process scrap and return recycled pellets to the production line.
The patented ISEC evo 702 is the eighth size in the line of highly automated combination units designed for in-house scrap reclamation. It can produce up to 3,307 pounds of recycled pellets per hour. The company said the unit returns the largest possible quantity of pellets to the production process. The next-largest model in the line, the ISEC evo 602, has a throughput of up to 2,756 pounds per hour.
The ISEC evo series uses only two drives, which significantly reduces energy consumption, she said.
The long, conical conveyor screw achieves a high degree of compression, causing oxygen to be discharged backwards and the material to be optimally preheated, Jung said. This improves the quality of the melt and recycled pellets.
Pure Loop refers to this as cold cutting, warm feeding. It said the process does not degrade the plastics, but instead results in high-quality pellets, stable throughput and high refeeding rates of recycled pellets.
The shredder is a single-shaft unit with two feed rams.
The ISEC evo 702 uses Pure Loop’s Ifeed system, which allows it to process many types, shapes and densities of in-house or post-industrial material. It also guarantees continuous and uniform filling of the extruder.
The ISEC evo 702 can link directly to a production line via a materials-handling system with a blower. It can also be configured so that it accepts production waste in crates or bins that have been dumped in by forklift.
The ISEC evo 702 is 37 feet wide including a belt conveyor and 13.3 feet high. When supplied without a degassing unit, it is 45.3 feet long.
Ron Shinn, editor
For more information
Erema North America Inc., Ipswich, Mass., 978-356-3771, www.erema.com
Herbold Meckesheim USA, North Smithfield, R.I., 401-597-5500, www.herboldusa.com
Hosokawa Alpine American Inc., Northborough, Mass., 508-655-1123, www.halpine.com
Tria America Inc., Charlotte, N.C., 704-716-0060, http://triaamerica.com
Vecoplan LLC, High Point, N.C., 336-252-4066, www.vecoplanllc.com
Ron Shinn | Editor
Editor Ron Shinn is a co-founder of Plastics Machinery & Manufacturing and has been covering the plastics industry for more than 35 years. He leads the editorial team, directs coverage and sets the editorial calendar. He also writes features, including the Talking Points column and On the Factory Floor, and covers recycling and sustainability for PMM and Plastics Recycling.
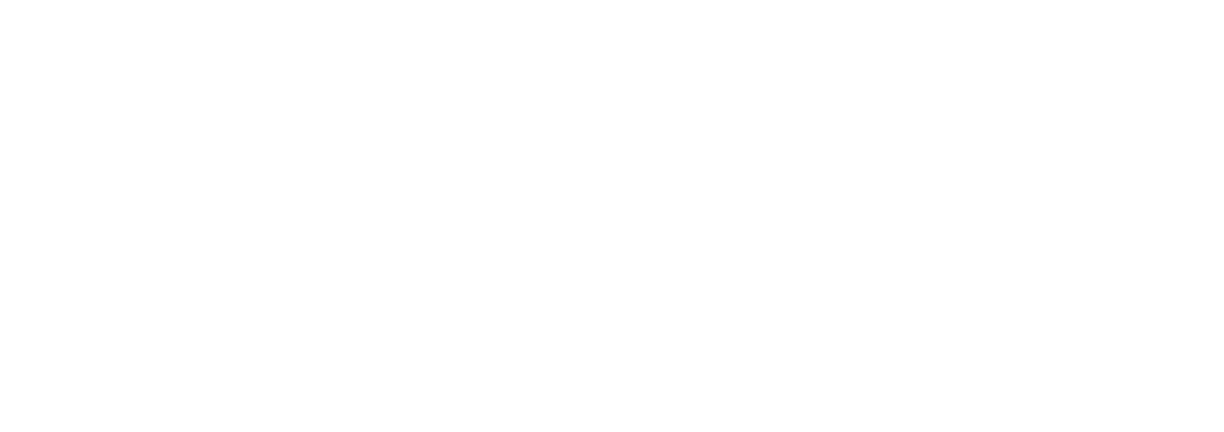