SML develops formulation for producing bale wrap on cast film lines
SML, an Austrian maker of film and sheet equipment, has developed a resin formulation and layer structure that allow its cast film lines to produce high-quality silage film. Typically, such agricultural film is made on blown film lines to achieve the required properties.
Silage films are used in agricultural settings to preserve bales of silage, hay and corn. The film is wrapped around the bales to prevent unwanted fermentation and maintain the nutritional value of the contents. Blown film typically has been used because, compared with cast film, it has been easier to produce the right impact strength, cling level and low oxygen permeability.
However, SML said it worked with material suppliers to develop a cast film that meets or exceeds the properties of blown film.
“Our major concern was the higher oxygen permeability of our cast film,” said Thomas Rauscher, SML product manager.
For peak performance, the agricultural market wants silage film with an oxygen permeability value of not more than 9,000 cubic centimeters per square meter in a 24-hour period. Typical cast stretch film of 25-micron gauge has a permeability value of greater than 10,000 cubic centimeters per square meter in a 24-hour period. SML, with its newest development, has achieved values of approximately 8,500 cubic centimeters per square meter in a 24-hour period.
Such film also needs to cling to itself when wrapped around the bales to form a tight seal. Typically, silage film made on SML’s cast film lines is five layers. SML’s formulation creates a cling layer with a high degree of stickiness on the outer surface of the roll.
“During the cast process, it is an easy task to put the cling material on the outer side of the roll, and we have several possibilities to guarantee a high stickiness,” Rauscher said. Processors can choose to produce film with a polyisobutylene (PIB) additive in a liquid or granular form, or an alternative that avoids the use of PIB while still offering good cling properties, the company said. The alternatives involve commercial polymers or polymer blends that are intrinsically sticky.
The PIB-free solutions reduce handling costs since silage film produced with PIB normally needs to “rest” at least 48 hours in a heated storage room, according to SML.
The cling value of the PIB-free film tested at 8 to 9 Newtons per meter — well within the desired cling level of 5 to 10 Newtons per meter, the company said.
SML’s formulation also includes the addition of a UV masterbatch to the slip layer of the film. The UV additive protects the goods against damage caused by sunlight.
The properties of the inner layers of the cast film guarantee the right impact strength and stretchability, SML said. The impact strength of silage films should be at least 10 grams per micron (g/µm). The tested cast films reached values of more than 15 g/µm, Rauscher said.
A roll width of 750mm is ideal for silage film, which makes SML’s MiniCast and SmartCast lines best suited for its production. The MiniCast produces two rolls of 750mm-wide film, while the SmartCast offers twice the production rate, turning out four 750mm rolls.
Production of silage film tends to be seasonal, and the same equipment can produce conventional stretch wrap film.
Contact:
SML North America Service Inc., Gloucester, Mass., 978-281-0560, www.sml.at
Bruce Geiselman
Senior Staff Reporter Bruce Geiselman covers extrusion, blow molding, additive manufacturing, automation and end markets including automotive and packaging. He also writes features, including In Other Words and Problem Solved, for Plastics Machinery & Manufacturing, Plastics Recycling and The Journal of Blow Molding. He has extensive experience in daily and magazine journalism.
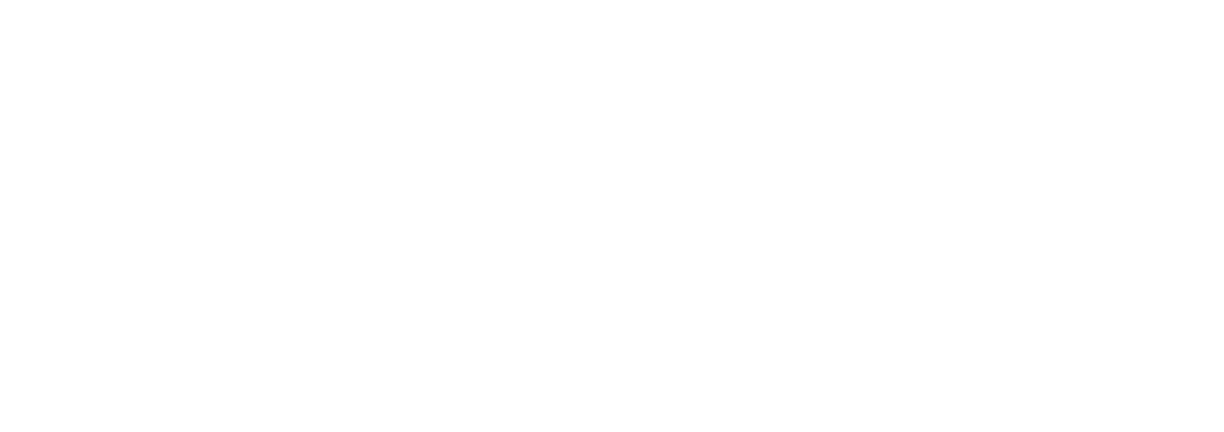