Extruder OEMs respond to changing medical landscape during pandemic
As demand for swab sticks, ventilator tubing and other critical medical products surged during the pandemic, the need for other types of extruded medical items declined. Processors — and their OEM suppliers — adapted to a changing marketplace. Now the trend is swinging back to elective surgeries and more traditional medical procedures, and extruder manufacturers are ready with new and upgraded technologies.
Davis-Standard upgrades MEDD
Davis-Standard is rolling out improvements to its MEDD (Medical Extruder Direct Drive) platform, said Joseph Wnuk, VP of elastomers, pipe/profiles and tubing, and specialty systems.
“We have some really exciting changes to our medical line of extruders with improvements in overall design, ergonomics and cable management,” Wnuk said. “It’s not yet complete, but it’s certainly on the near horizon in 2021.”
Among the upgrades are a more “clean-room-friendly” design. Machine guarding will eliminate areas where contaminants might become trapped.
“It’s an easier wipe-down at the end of the shift and easier to keep clean,” Wnuk said. In addition, the new design will include improved cable-management features.
The most significant change will be more models with a wider size range, Wnuk said.
Davis-Standard’s current MEDD, for producing medical tubing, is available in 19mm and 25mm screw diameters, with a quick-change barrel and screw assembly that allows for easy changeovers in size. Later this year, Davis-Standard will expand the offerings with a new model that can switch between 25mm and 32mm, and a model that can swap between 32mm and 38mm barrel assemblies.
“The complete barrel and screw assembly are on quick disconnect plugs for interchangeability,” Wnuk said.
Davis-Standard is expanding its medical extruder offerings at a time when demand is growing, he said. While the company expected a soft year in 2020 because of the pandemic, it experienced steady sales, Wnuk said.
“Orders have been extremely strong in several segments of the business,” Wnuk said. “Order activity early on was driven primarily by COVID-related products, such as IV tubing, pharma tubing, swab sticks and everything related to testing and vaccine development.”
Going into 2021, equipment sales for medical tubing have been extremely strong, likely because of an increase in elective surgeries and procedures that were postponed during the pandemic.
Graham Engineering sees shifts in demand
Graham Engineering’s American Kuhne brand sells medical extruders used to produce tubing.
In late 2019, the company introduced the Navigator XC300 control system to its Compact Modular MD series of extruders designed for clean-room environments.
“Included in this system is an option for ‘pressure control,’ in which the extruder produces constant pressure, leading to constant output without the need for a melt pump for products that are not compatible with the use of a pump due to shear or degradation reasons,” Michael Duff, Graham Engineering’s VP of sales and service, said. “This, tied to our modular extruder for medical applications, provides medical tubing manufacturers a complete process suitable for the most demanding multi-lumen tubing products.”
Demand for medical extrusion equipment has remained strong during the COVID-19 pandemic, but Duff noticed a shift in the types of products produced.
“While our medical sales have remained high and a significant portion of our business, we saw a shift during the early stages of COVID away from microtubing, often associated with elective and non-critical surgery, to larger tubes associated with airway products such as ventilator tubing,” Duff said.
“We are seeing a recovery in the microtubing business as our customers are returning to a more traditional demand. Demand for melt-blown equipment also increased to meet the demands of filtration media and medical personnel apparel such as masks and gowns.”
Also related to the pandemic, Graham Engineering noted that high demand for cleaning products, wipes and sanitizers boosted demand from its customers for equipment to make packaging.
Leistritz offers features for medical molding
Leistritz offers an optional containment enclosure on its ZSE-18 and ZSE-27 extruders that are used in manufacturing medical devices.
“Many additives that are compounded into a formulation for a medical device are by themselves toxic and need to be handled with care before compounding with polymers in a co-rotating twin-screw extruder,” said Charlie Martin, president and GM of Leistritz Extrusion. “Examples include anti-microbial medical tubes, bioresorbable implanted screws, contraceptive rings and a variety of multi-functional dosage forms. In these cases, a ZSE GMP twin-screw system will be designed to satisfy the required containment levels associated with these additives.”
The enclosure contains the twin-screw process section and feeders. It integrates refill valves to facilitate feeder-hopper refill. The top section of the enclosure is attached to a mobile base, allowing it to be removed for access to the process section and feeder. The stainless-steel frame features a screw jack system to lower the enclosure onto the extruder base.
Other features of extruders sold with the optional enclosure include polished stainless-steel construction; urethane casters with a wheel locking system; dual HEPA filters; LED inside lighting; an open front face with a pivoting Lexan shield; a gauge to monitor airflow with a low static pressure alarm and shutdown interlock; a wand for misting, wiping down and cleaning surfaces; a waste chute for rubber gloves and wipes; and a Tri Clamp enclosure drain with ball valve and hose.
Bausano says bag, tube demand drove sales
Italian extruder manufacturer Bausano has seen an increase in sales over the past year for its lines for producing medical tubes and bags, said Clemente Bausano, VP.
“In the last 12 months, we have sold and closed various deals related to medical bags and tubing in many countries of the world,” Bausano said. “This kind of product has been much more required since the pandemic started last year.”
The company offers both single-screw and twin-screw counter-rotating models that can be used in medical applications.
The twin-screw Bausano MD 66 and the MD 72 can be used for processing PVC and other non-toxic materials for medical tubing and medical bags. The MD 66 features a 66mm-diameter screw and the MD 72 features a 72mm-diameter screw.
Bausano’s MD extruders are available in MD Plus and MD Nextmover models, both of which can be used for medical applications. The MD Nextmover line represents an upgrade of the MD Plus range, integrating an advanced centralized control system that offers advantages in terms of intelligent diagnosis and predictive maintenance. The Nextmover line also includes an induction cylinder heating system for energy efficiency and high-efficiency motors.
“In our experience, the MD 66 and MD 72 (Plus or Nextmover) are the most suitable and the most employed models for medical applications because of the screw diameter,” Bausano said.
Also available is Bausano’s E-GO 60 single-screw extruder, with a 60mm-diameter screw, for making tubing.
Medical extruders can be custom designed to meet a customer’s needs, and normally they feature extensive use of stainless-steel surfaces for easy cleanup in clean-room settings, Bausano said. Downstream equipment for medical extrusion lines includes accessories that accurately measure the internal and external diameter of tubing in accordance with the quality standards required by the pharmaceutical industry, he said.
“It’s something that is much more precise than if compared to normal extrusion obligations,” Bausano said.
Increased demand has come from both existing and new customers, he said.
“Some were traditional customers of ours that just wanted to increase their production, so, they were asking for new lines,” Bausano said. “Some others were new customers or new people that wanted to invest in these kinds of applications because of the boom in demand.”
However, the increase in demand extended beyond typical medical extruders to include compounding equipment, Bausano said.
“We didn’t witness just an increase in the demand for these kinds of lines that produce the final product, but we also saw a very high demand for compounding lines for medical applications,” he said.
For more information:
Bausano & Figli SpA, Rivarolo Canavese, Italy, [email protected],
www.bausano.com
Davis-Standard LLC, Pawcatuck, Conn., 860-599-1010, www.davis-standard.com
Graham Engineering Corp., York, Pa., 717-848-3755, www.americankuhne.com
Leistritz Extrusion, Somerville, N.J., 908-685-2333, https://extruders.leistritz.com
More on medical parts and plastics
Parts makers step up their processes to meet needs
Health-care market keeps IMM makers busy
Injection unit, machine dedicated for test tubes among new processing technologies
Auxiliary makers prioritized medical orders during pandemic
Robots shine in clean room duties
Economist: Run on medical goods provided jolt to plastics manufacturers
University speedily designs and prints nasal swabs
Geisinger’s 3-D lab printed devices to help health care workers stay safe
Beckwood Press designs compression molding equipment for medical devices
Quick deliveries, new products: Husky details COVID-19 response
Bruce Geiselman
Senior Staff Reporter Bruce Geiselman covers extrusion, blow molding, additive manufacturing, automation and end markets including automotive and packaging. He also writes features, including In Other Words and Problem Solved, for Plastics Machinery & Manufacturing, Plastics Recycling and The Journal of Blow Molding. He has extensive experience in daily and magazine journalism.
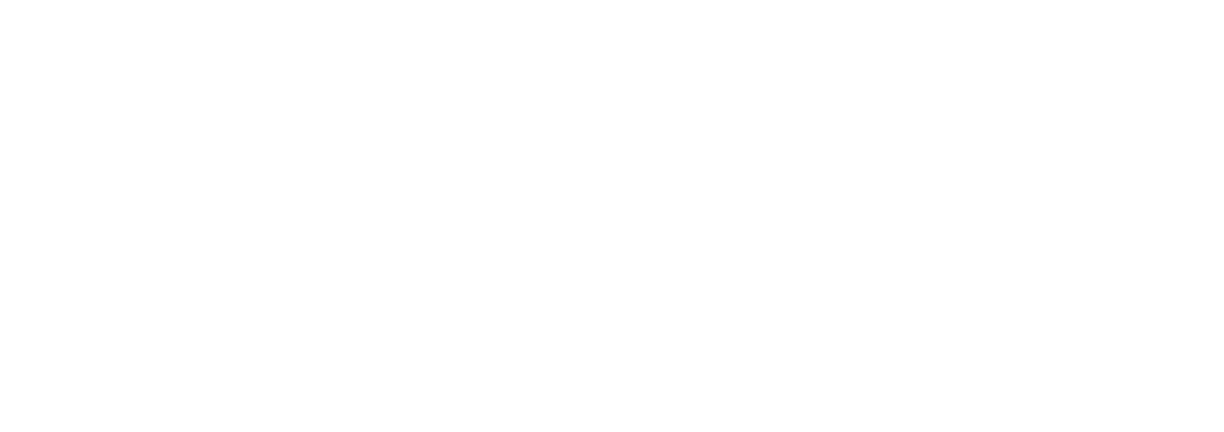