Recycling, bioplastics driving demand for Entek's compounding extruders
Part 1 of a series on extrusion for sustainable materials.
Entek, a manufacturer of twin-screw, co-rotating compounding extruders, is reporting greater interest in plastics recycling and bioplastics among its customers.
Related: Graham customers devoting extruders full-time to bioplastics; CPM sees demand growing for specialized machines; Milacron tailors screws to meet demand
Interest in recycled plastics and bioplastics — biodegradable plastics derived from biological substances rather than from petroleum — tends to be cyclical, said Dean Elliott, technical process manager. Entek runs pilot plant trials for customers. Early last year, about 13 percent of its trials focused on bioplastics and/or recycled plastics. However, by the end of last year, the number of trials involving those materials dropped to zero. Then, in the second quarter of 2020, the percentage surged to 80 percent.
“That’s what I’ve seen for the last 10 to 15 years; it comes and goes,” Elliott said.
On the sales side, Entek is seeing significant growth in sales of extruders designed for compounding recycled resins and bioplastics, said Linda Campbell, Entek’s VP of sales.
“That’s certainly what we have seen in 2019 and 2020,” Campbell said. “The majority of our sales increase — we’ve doubled our budget in sales — is directly related to a recycled product. Dean is absolutely correct, it is cyclical, but on the sales side, we’ve certainly seen a gain.”
While company representatives can’t say for certain what is behind the uptick in interest, Campbell said many in the industry point to China’s ban two years ago on imports of plastics for recycling, which left many U.S. manufacturers looking for another outlet for their waste material.
“There are some processing challenges to recycle their polymer waste,” Elliott said. “We worked with them, and we actually had some success to recycle the waste stream … We’re working on a solution right now. That supports what Linda is saying about heightened awareness is driving this.”
To address the challenges posed by recycled plastics and bioplastics, Entek offers custom extruders.
“What do biopolymers and recycled plastic have in common? What they have in common is moisture — moisture is a concern,” Elliott said. “The other thing they have in common is process variation.”
When processing recycled plastics (especially PET) and biopolymers, processors are likely to encounter high levels and varying levels of moisture. To deal with that, they may need to dry the resin and/or use multiple vents on an extruder.
For example, starch-based bioplastics, such as those made with corn or potato starch, may contain up to 12 percent moisture, Elliott said. Polyhydroxyalkanoates and polylactic acid (PLA) also tend to be hygroscopic, he said.
To deal with moisture means additional venting is recommended on co-rotating, twin-screw extruders, he said.
“For petroleum-based plastics that you compound with various additives, it’s very typical to see one vent on a co-rotating, twin-screw extruder,” Elliott said. “For biopolymers and recycled polymers, it’s very common to see two or three vents on the extruder.”
Co-rotating, twin-screw extruders offer the flexibility to add venting, Campbell said.
“The twin-screw extruder equipment is looked at as more flexible than a single-screw because we have segmented barrels and screws for flexibility as to where a single screw is one solid barrel and screw,” Campbell said. “We feel like we’re uniquely positioned with our equipment to help those folks out there trying to find ways to recycle material and bring polymers to market.”
Venting on a twin-screw extruder is more effective than on a single-screw extruder, Elliott said. Extruders designed for processing bioplastics or recycled plastics also may require vent stuffers, which keep the polymer in the extruder but allow the gases to escape.
“You won’t typically see that on a petroleum-based machine, but you will see it on a biopolymer machine or a recycle machine,” Elliott said.
Bioplastics also tend to be more temperature-sensitive, meaning extruders dedicated to processing those materials need to have barrel and screw designs that minimize shear. While virgin and recycled petroleum-based polymers can withstand considerable shear heat, bioplastics cannot.
“You have to treat them more gently,” Elliott said. “You can’t be too aggressive with them in processing.”
That means barrels sometimes need to be shorter. In addition, if a fiber like hemp is added to a biopolymer, it must be fed into the melt further down the barrel. Otherwise, it would likely burn during processing.
“You would melt the polymer first, and then you add the hemp downstream,” Elliott said.
Because they are likely to contain a multitude of contaminants, post-consumer plastics also require special screen changers capable of handling higher contamination rates, Elliott said.
“The choices of different types of screen changers are quite extensive,” he said. “It depends on the amount of contamination in the recycle stream.”
Contact:
Entek Manufacturing, Lebanon, Ore., 541-259-1068, http://entek.com/
Bruce Geiselman
Senior Staff Reporter Bruce Geiselman covers extrusion, blow molding, additive manufacturing, automation and end markets including automotive and packaging. He also writes features, including In Other Words and Problem Solved, for Plastics Machinery & Manufacturing, Plastics Recycling and The Journal of Blow Molding. He has extensive experience in daily and magazine journalism.
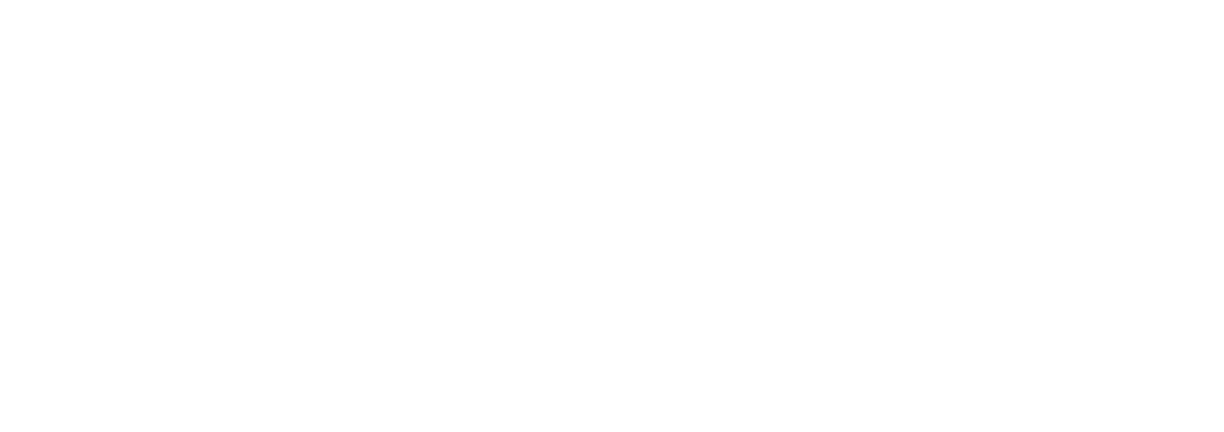