Leistritz has upgraded its tandem twin-screw extrusion line that produces laminated film or sheet in a multi-stage process. The line can make transdermal patches for pharmaceutical, medical and wound-care applications, as well as a variety of packaging, roofing, battery separator and specialty laminate products.
“The improvements are not specific to transdermal patches; they’re applicable to any film/sheet lamination system,” said Charlie Martin, president and GM of Leistritz Extrusion.
Related: Charlie Martin's expertise rooted in hard work
New features that are options on custom-designed systems include:
- Cooling rolls with quick-release bearing clamps and individual drives.
- An integral rewinder with closed-loop tension control.
- Shearing or slitting equipment to trim edges.
- Dual unwinders with magnetic particle brakes.
- Stainless-steel construction.
In the case of a transdermal patch, the line processes and mixes polyisobutylene rubber, the same material used in chewing gum, with resin and additives, such as an active pharmaceutical ingredient. For other applications, the line can work with a variety of polymers, including TPE, thermoplastic vulcanizates and other compounds.
This type of tandem twin-screw extrusion line is unusual, Martin said.
“There are probably less than four machine systems like that in the world, where you’ve got a twin-screw feeding a twin-screw into a lamination system,” he said.
The first extruder conditions the rubber or resin, which is metered into a second extruder for mixing with polymers, fillers and additives. A gear pump attached to the end of the second extruder builds and stabilizes pressure to feed a stainless-steel die that is from 100mm to 250mm wide and includes a removable lip and cartridge heaters.
A downstream lamination system applies an adhesive and a layer that can be peeled off.
The Leistritz system can be used for any product that has an adhesive or modified polymer applied to a substrate.
“Our U.S.A. laboratory is equipped to develop laminate processes with twin-screw technologies,” Martin said.
The lamination system includes a vertical, three-roll stack that accepts the sheet from the die and forms and cools it. The system includes:
- Chrome-plated rolls.
- Rotary unions for liquid cooling and heating of rolls.
- Gap adjustments via fine-threaded hand-wheels.
- Hardened, positive stops.
- Digital indicators for upper and lower roll gap.
- Manual jackscrew adjusters for adjusting the height of the entire unit.
- A heavy-duty steel mainframe.
The system’s pull-roll station features upper and lower rubber rolls with the nip pressure adjusted via air cylinders.
The unwind stations are mounted to the base of the unit to facilitate lamination. They have a fabricated steel frame and feature an edge-guiding system with an electro-mechanical actuator and ultrasonic edge detector.
The winder station, which winds the product onto cores, has an AC motor with closed-loop tension controlled by transducer tension roll and ultrasonic roll-diameter sensor.
Bruce Geiselman, senior staff reporter
For more information
Leistritz Extrusion, Somerville, N.J., 908-685-2333, www.leistritz.com/en
Bruce Geiselman
Senior Staff Reporter Bruce Geiselman covers extrusion, blow molding, additive manufacturing, automation and end markets including automotive and packaging. He also writes features, including In Other Words and Problem Solved, for Plastics Machinery & Manufacturing, Plastics Recycling and The Journal of Blow Molding. He has extensive experience in daily and magazine journalism.
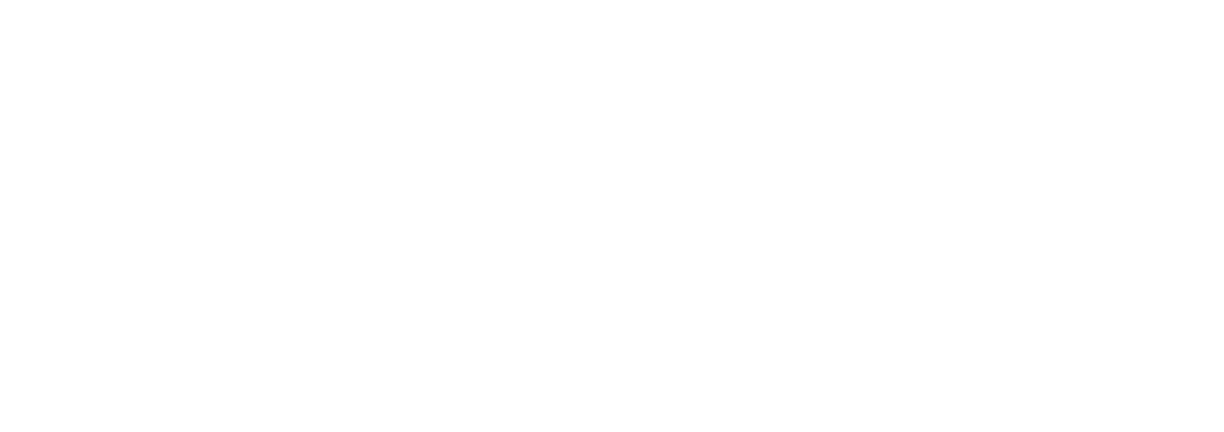