By Bruce Geiselman
Machinery OEMs are helping sheet makers and thermoforming companies to reduce material usage, cut transportation costs and ease their impact on the environment.
Expanding interest in foaming
For extruders, foaming is one of the major ways to lightweight.
“The reason, generally, for foaming is that you can get the same stiffness in the tray without the same weight of materials,” said Mark Jones, director of support service for extrusion line supplier SML North America Service Inc. “It is the I-beam effect. … You get two very stiff surfaces, the top and bottom surfaces of the sheet, and in between, you have this foam that keeps the two stiff surfaces apart. When you do that, you’re basically building the equivalent of a bridge I-beam, and it’s a lot stiffer for the same weight.”
According to SML, a typical PET A-B-A structure weighs half as much as rigid sheet. It includes a foam core comprising up to 85 percent of the sheet thickness.
SML recently developing an extrusion line for producing sheet with improved heat resistance, insulation properties and recyclability in a joint R&D program with its partner, Kiefel. The three-layer, mono-material sheet made from PP or PET has a foamed center layer. No special additives are required to enhance the heat stability of the sheet, which makes it economical for producing low-weight cups with excellent insulation properties, SML said.
Battenfeld-Cincinnati reported that manufacturers in the automotive and aircraft industries retain their traditional strong interest in producing lighter-weight parts.
“What has changed is the number of inquiries for foaming,” said Henning Stieglitz, CTO of BC Extrusion Holding GmbH.
Gneuss, which offers a foaming module with its standard MRS extruder, said its technology can turn undried PET into foamed sheet weighing in at less than half the weight of rigid sheet. The process involves injecting carbon dioxide or nitrogen into the melt. Operators can use 100 percent post-consumer PET, such as flake from soda bottles, or in-house regrind.
One of the challenges of working with undried PET is maintaining a high intrinsic viscosity (IV), said Monika Gneuss, VP of sales and marketing. However, the company’s MRS extruder is extremely effective at distributing the nucleating and foaming agents completely and homogeneously in the melt.
The extruder has eight satellite screws that rotate in the opposite direction of the main screw, expanding and exchanging the surface area of the melt. A vacuum system then pulls out the moisture before the melt goes through a filtration system to remove contaminants and an inline viscometer ensures adequate IV for the foaming process. To adjust the viscosity, an operator also can increase or reduce the amount of vacuum applied to the melt. Applying more vacuum increases the melt viscosity; applying less vacuum reduces the viscosity.
Foamed PET sheet is ideal for making thermoformed food containers, including meat trays, egg boxes and cups.
Limitations of foaming
Gneuss introduced its foaming technology in response to increasing interest from customers that wanted to reduce material use and cost.
However, both Stieglitz and Gneuss noted that foaming meets some green considerations but runs afoul of others, because of concerns about recyclability.
Foamed PET is easily recycled. However, PET often is separated by weight in recycling facilities, making the task of separating out foamed PET tricky.
“Depending on the degree of foaming, these products cannot be separated properly in a sorting process,” Stieglitz said.
Environmentalists’ efforts appear centered on banning PS containers. However, Gneuss said some processors are reluctant to “muddy the waters” by foaming any plastic, including PET.
“I think some people are more cautious now,” she said. “There are cost savings to be made, but then, what if somebody bans it? What if you invest in the technology and then somebody’s going to ban foamed products? I would say we encounter a lot of caution.”
Other methods
Foaming is not the only way to reduce product weight. One trend among plastics processors over the last few years is a growing interest in thermoforming thin-walled products that previously had been injection molded, said Gregory Romanski, an area sales manager for WM Thermoforming.
“Customers sometimes are trying to move from injection [molding] toward thermoforming technology,” he said. Injection molding a sidewall thinner than 0.4mm is a challenge, but it can easily be achieved by thermoforming, Romanski said. “This is also resulting in faster and higher production outputs as well as lower tooling and material costs.”
Moving from injection molding to thermoforming can result in thinner-walled products, faster production and lower tooling and material costs, he said.
However, only certain products lend themselves to transitioning from injection molding to thermoforming, he said. They include rigid packaging and industrial products, such as electrical components, he said.
Battenfeld-Cincinnati’s Stieglitz ticked off a number of other ways to reduce product weight. They include designing components based on finite element method calculations, so that resin is used only where it is needed. Another method involves using materials that are stronger than the materials that were previously used.
Weighing in on future advances
Romanski believes the industry’s abilities to go much lighter might already be stretched.
“I think we are getting to the point where we cannot go much thinner than we already are in order to maintain a product with a certain structure that is not becoming flexible,” he said. “You still want to have … rigid packaging at the end. The minimum gauge is a limitation.”
In addition, if a thermoformed product is too thin, cutting and punching tools might not make clean cuts, he said.
Stieglitz, though, is optimistic that lightweighting efforts will continue to make strides.
“It can be foreseen that new technologies will allow lighter-weight parts than we have today,” he said.
Contact
Battenfeld-Cincinnati USA, McPherson, Kan., 620-241-6843, www.battenfeld-cincinnati.com
Gneuss Inc., Matthews, N.C., 704-841-7251, www.gneuss.com
SML North America Service Inc., Gloucester, Mass., 978-281-0560, www.sml.at
WM Thermoforming Machines SA, Stabio, Switzerland, 41-91-640-7050, www.wm-thermoforming.com
Bruce Geiselman
Senior Staff Reporter Bruce Geiselman covers extrusion, blow molding, additive manufacturing, automation and end markets including automotive and packaging. He also writes features, including In Other Words and Problem Solved, for Plastics Machinery & Manufacturing, Plastics Recycling and The Journal of Blow Molding. He has extensive experience in daily and magazine journalism.
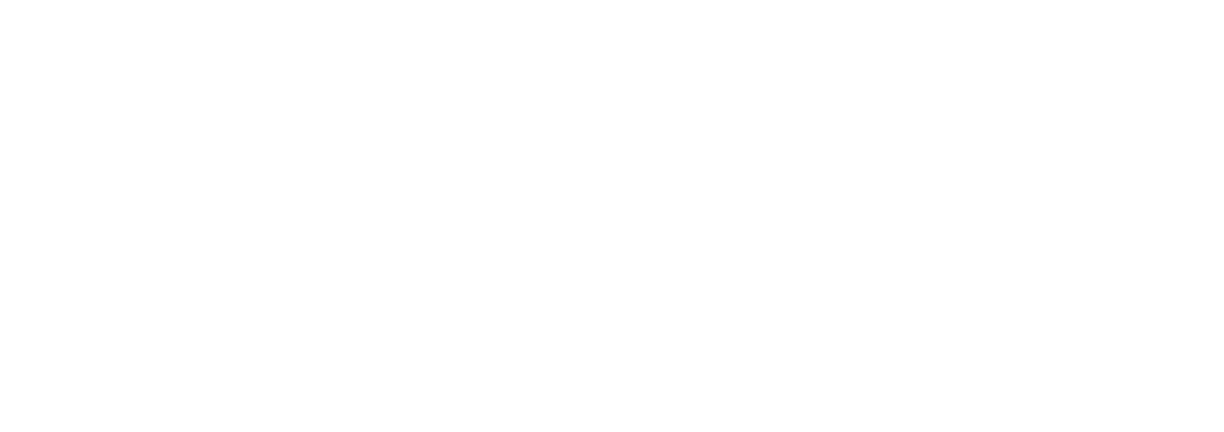