Multiplexing Surface Generation of Oakham, England, has developed a high-volume compression molding system that incorporates its proprietary technology for mold temperature control. The Multiplexing system, which can be used for thermoplastic and thermoset composites, consists of a linear conveyor and proprietary cassettes that transport molds through stations for material loading, preheating in an infrared oven, molding and demolding. In the molding station, the company's Production to Functional Specification (PtFS) technology delivers precise, localized control of heating and cooling throughout the molding cycle by applying streams of hot and cold air to the back of the mold. The cassettes maintain the required pressure on the molds to protect part quality until parts are cooled and demolded.
What's new? High-volume production of compression molded parts.
Benefits Dramatically reduced cycle times and energy use. The use of multiple stations minimizes the time the mold spends within the press, allowing production times of as low as one minute. Parts that take more than six minutes using traditional compression molding can be produced in two minutes using Multiplexing. Surface Generation says the PtFS technology can reduce energy use by as much as 95 percent compared to traditional compression molding.
Surface Generation America, Richardson, Texas, 972-699-9976, www.surface-generation.com
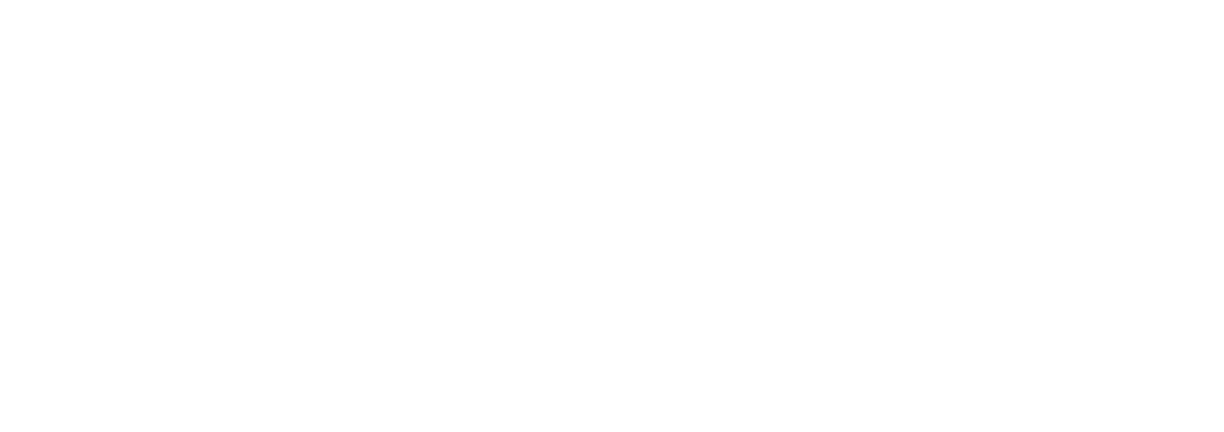