For 12 years before selling its first twin-screw extruder, Entek, Lebanon, Ore., was a successful extrusion company producing complex specialty sheet used in lead acid battery separators.
Today it commands about 60 percent of the lead acid battery separator market in North America and smaller shares in other parts of the world. Entek's separator material goes into automotive, forklift, golf cart and many other industrial batteries.
Entek's worldwide market share for lithium-ion battery separator film, where it focuses on much smaller batteries for personal electronics, is 5 to 6 percent. All of its lithium-ion customers are in China and Korea.
Entek started making lead acid battery separator sheet in 1984 and lithium-ion separator film in 2001. Officials say there is good growth potential in the fiercely competitive lithium-ion market.
The average automobile battery uses about 1.5 square meters (about 16 square feet) of separator material to wrap or envelope every other lead plate. A typical cellphone battery uses about 0.1 square meter (about 1 square foot) of separator film.
Entek manufactures lead acid battery separator sheet, lithium-ion battery film and a full range of extruders at its headquarters campus in Oregon. It is the only company making lead acid and lithium-ion separators on the same site. Its battery separator sheet and film are sold on six continents.
Although Entek does not divulge sales figures, the lead acid battery separator business accounts for about 70 percent of total company sales. The other 30 percent comes from equal sales of lithium-ion battery separator film and extruder-related products and services.
Kirk Hanawalt, president of Entek's extruder business and one of the owners of the company, recently led a tour of the newest of Entek's nine extrusion lines manufacturing lead acid separator material. Entek also has two lines for thinner lithium-ion separator film in Lebanon but it does not show these lines to visitors because its technology is closely guarded.
Entek also has four more lines for the lead acid battery separator material in Newcastle, England.
"It takes less than five minutes from the time raw materials go into the extruder until we put the product in a box to test and ship," says Hanawalt in describing the highly automated process.
Entek builds all of the equipment for its extrusion lines. The newest line is 350 feet long and took 2½ years to design and build.
Lead acid battery separators are made by mixing a specialty grade of amorphous silica, ultra-high molecular weight PE, oil and a few other ingredients in smaller quantities, then pushing the mixture through a die with a 133mm extruder at 392 degrees Fahrenheit. This forms an oil-filled sheet that is then calendered to the desired thickness. A rib pattern is embossed during calendering.
After calendering, most of the oil is extracted with a trichloroethylene bath and steam process, then the sheet is dried, wound and slit into separate strips. The individual strips are then wound into rolls, each containing about 6,000 feet of material. Battery makers turn the material into envelopes for the battery plates.
The mixture going into the extruder is more than 60 percent oil; the finished product contains about 15 percent oil, which helps the separator material last for five years or longer in battery acid.
"It is a highly engineered product," says Hanawalt. "It looks like a plastic film but there is a lot more to it."
The silica creates a porous structure that provides the separator's electrical properties while the PE provides its mechanical properties. The finished PE separator has a porosity range of 50 to 65 percent. Customers demand different widths, back web thickness, rib height, shoulder designs and final oil content, according to Hanawalt. Back web thickness typically ranges from 0.15mm to 0.25mm. Overall thickness ranges from 0.6mm to 1.5mm.
The process to remove oil content from 65 percent down to about 15 percent is accomplished in a series of fully enclosed chemical and steam baths. Drying takes place in an oven that is 250 feet long. The path of the sheet through the entire line is about 1,000 feet. Excess material trimmed from the sheet is automatically recycled back into the extruder.
A vision system watches for pinholes that are bigger than 25 microns. If more than two are found in a 6,000-foot roll, the roll is recycled into the extrusion process. Entek's purpose-built 133mm extruder has a 1,000-horsepower motor. The line has the capacity to produce separator material for more than 40 million batteries per year.
The downstream handling equipment — all built in-house at Entek's extruder manufacturing plant — requires no human intervention until the rolls are put into shipping containers. Tracks built into the floor facilitate changing calender rolls, which takes about an hour. The 77,000-square-foot building that houses the newest line was built to accommodate a second line at a later date. The building is kept extremely clean and vapors are captured, cleaned and eliminated. The trichloroethylene used to extract oil is captured, distilled and re-used.
"This line is still in its planned ramp-up to maximum capacity and is running at about 85 percent capacity," says Hanawalt. It has been in operation since July 2014. The ramp-up to full capacity is scheduled to be complete this summer in time for the peak demand for batteries and battery separators in the fall and winter months.
Ron Shinn, editor
Contact:
Entek,
541-259-1068, www.entek.com
Ron Shinn | Editor
Editor Ron Shinn is a co-founder of Plastics Machinery & Manufacturing and has been covering the plastics industry for more than 35 years. He leads the editorial team, directs coverage and sets the editorial calendar. He also writes features, including the Talking Points column and On the Factory Floor, and covers recycling and sustainability for PMM and Plastics Recycling.
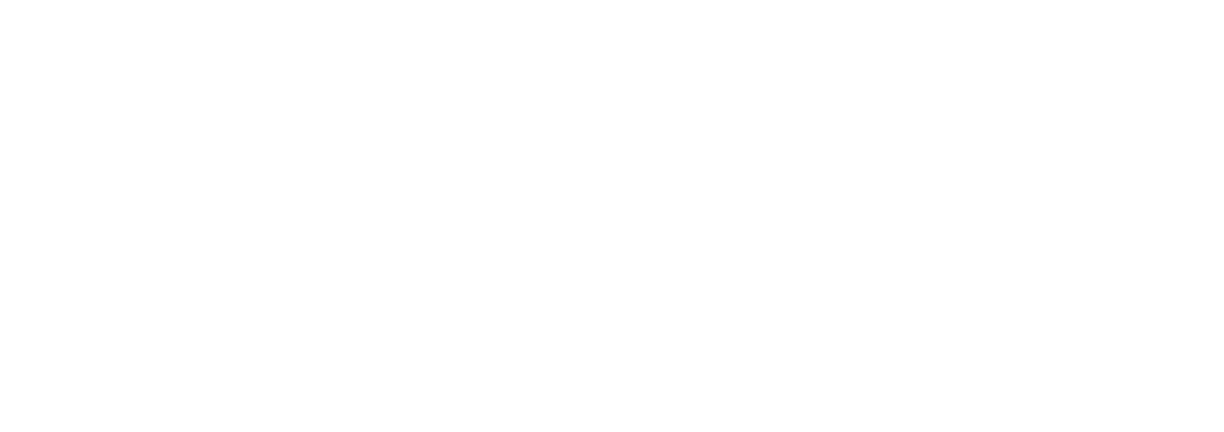