Growth in electric vehicles fuels market for Entek’s battery separators
By Bruce Geiselman
The move toward electric vehicles (EVs) has boosted demand for the complex PE-based battery separators produced by Entek, a company also known for manufacturing and selling twin-screw extruders.
Entek is the second-largest lead-acid battery separator manufacturer in the world, CTO Richard Pekala said. It is a smaller player for lithium-ion separators, but it is working to increase its sales in the U.S. and U.K., he said.
“Lithium-ion batteries were introduced into the marketplace in 1982 by Sony, and they were mainly smaller cells for computers, laptops, and cell phone applications,” Pekala said. “The big opportunity moving forward is the amount of separator that’s required for these large lithium-ion battery packs that are going into electric vehicles. Kind of a figure of merit, if you will, is that for every gigawatt hour that the battery companies talk about putting in place, it requires somewhere in the order of 10 million square meters of separator.”
As an example, Pekala pointed to Tesla building its Gigafactory in Sparks, Nev., that produces electric motors and battery packs.
“Elon Musk and the Nevada Gigafactory has on the order of 35 gigawatt hours [of battery production],” Pekala said. “So, 350 million square meters of battery separator would be required to support that plant every year.”
In 2021, Tesla’s worldwide operations delivered over 936,000 vehicles, the company announced in January.
EV manufacturers around the world are reporting increased production.
“You’re seeing these announcements from around the world. In Europe, they’re talking about putting in over 500 gigawatt hours of capacity. If you multiply that, you’ve got 5 billion square meters of separator. Those are the opportunities that we’re looking at.”
Designed to prevents electrical short circuits, battery separators segregate the positive and negative electrodes in a battery, Pekala said. The sheet (for lead-acid batteries) or film (for lithium-ion batteries) is porous to ions flowing between the electrodes.
Battery separators are manufactured using twin-screw extruders and involve the compounding of a polymer with a process oil or plasticizer. Depending on whether the end product is a lead-acid or lithium-ion battery, the material can contain silica as a filler. The sheet or film can be biaxially oriented, and the plasticizer in most cases is removed with a solvent that is subsequently evaporated to form the porous separator.
Among companies fueling the battery separator business is Britishvolt, aThe MOU addresses Britishvolt’s exploration into the possible use of Entek’s separators in its batteries and a potential investment by Britishvolt in facilities for producing Entek’s ceramic-coated lithium-ion battery separator materials in England.
“Britishvolt plans to put a ‘gigafactory’ in [near] Blyth in the U.K., which it turns out is about 10 miles from our Newcastle, England, plant, where we produce lead-acid battery separators,” Pekala said. “Eventually, we would see lithium-ion separator production taking place in the U.K. for Entek at some point in the future.”
While a significant amount of attention these days is paid to the production of lithium-ion batteries for EVs, Entek realizes that lead-acid batteries will remain in demand, Pekala said.
“The interesting thing is, even as people get excited about EVs and the growth opportunities there, a lot of folks don’t appreciate that in these electric vehicles, you’ve still got a 12-volt battery system,” Pekala said.
A traditional 12-volt lead-acid battery runs accessories such as the radio, interior lights, door locks and other non-propulsion features.
“We’re still investing as a company in lead-acid separators,” Pekala said. “We are in the process of putting a new production line at our Indonesia facility. We still see growth for lead-acid separators in Asia. There are big opportunities, we think, in India and other parts of Southeast Asia.”
Last September, Entek also purchased NSG’s Battery Separator Division, supplying separators for lead-acid batteries in locations in Asia, including Japan.
“There are lots of things going on … and they’re all involving extrusion of plastic materials, ultra-high-molecular-weight polyethylene in particular,” Pekala said. “We’re excited about the future. It’s a good time to be providing components that fit into the category of energy storage.”
Bruce Geiselman, senior staff reporter
Contact:
Entek, Lebanon, Ore., 541-259-3901, http://entek.com
Bruce Geiselman
Senior Staff Reporter Bruce Geiselman covers extrusion, blow molding, additive manufacturing, automation and end markets including automotive and packaging. He also writes features, including In Other Words and Problem Solved, for Plastics Machinery & Manufacturing, Plastics Recycling and The Journal of Blow Molding. He has extensive experience in daily and magazine journalism.
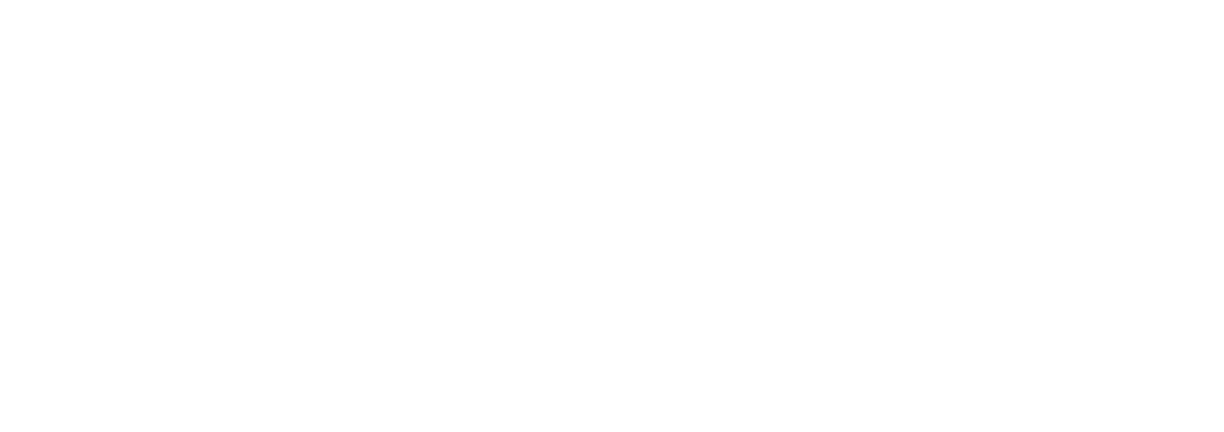