By Ron Shinn
More and more brand owners that once purchased huge numbers of blow molded containers have in recent years started making their own. It is a trend that Bekum America has embraced with application-specific extrusion blow molding equipment and customer support that can jumpstart customers new to container manufacturing.
“They were consumers of plastic containers, and now they have become producers,” said Steven London, president and COO of Bekum America Corp. in Williamston, Mich. “People want to control their own destiny, not be constrained by the supply chain swings, plus and minus.”
Bekum America’s parent company, Bekum Maschinenfabriken GmbH, founded in 1959, is headquartered in Berlin and builds machinery in Traismauer, Austria, as well as Williamston.
The company has four lines of equipment — the H-series, HyBlow/EBlow models, XBlow industrial machines and the BA-series. Versatile H-series machines are compact, flexible and offer the lowest cost per output. HyBlow/EBlow models come in hydraulic, all-electric and hybrid variants, easily tailored for a customer’s application. XBlow machines are single-station units for canisters, intermediate bulk containers (IBCs), drums, water tanks and industrial parts. The BA-series machines are especially suited for jerrycans, L-ring drums, automotive fuel tanks, air ducts and spoilers.
The H-series and EBlow/HyBlow machines are built in Williamston and account for about 90 percent of the Bekum machines sold in North America. The rest are XBlow and BA-series imported from Austria. Occasionally, some machines built in Williamston are shipped to customers in Europe or elsewhere outside of the territory generally covered by the Williamston division.
Bekum sells blow molding machines in Asia but does not manufacture there.
London said industry consolidation has resulted in a decrease in the number of small, regional, strictly custom blow molders. But Bekum’s business has remained strong. He said sales in 2024 were better than 2023, and he expects 2025 to be better than 2024.
London said Bekum is the leading provider of mono-layer and multi-layer extrusion blow molding technology in North America.
Bekum America currently has a backlog of machinery orders. London said that has been the case for the past two years and he has been unable to build machines to stock in Williamston for quick delivery.
A machine for nearly any need
The wide range of containers made on Bekum machines is another reason for its growth. That includes nearly everything from a 5-milliliter inhaler to a 330-gallon IBC, across markets from medical to industrial products.
“There have been downturns in the market, but it seems that during these downturns, we’ve always had a market segment that was strong, that helped us maintain or even grow during some difficult times for the plastics industry as a whole,” London said during a recent interview at his Williamston office. “We just have a diverse customer base.”
London said Bekum’s technical expertise has also helped differentiate it from competitors.
“We have a great technical staff in the organization globally and we are able to handle some complex projects that have brought us business,” he said. “Now the simpler projects are not coming here. Those customers are not knocking at the door or calling us.”
That business model seems to be working fine for Bekum America. In 2021, it added 40,000 square feet of manufacturing space and 7,500 square feet of office space in Williamston. The total facility now covers more than 160,000 square feet.
The expansion improved workflow and enabled the building of more machines at the same time.
Gary Carr, VP of sales, said the expansion offers another big benefit.
“It provides us an opportunity to build a machine and basically simulate the customer’s plant environment in terms of final conveyor layout, downstream and even auxiliary equipment,” Carr said. “It has allowed Bekum to do more of a project, turnkey approach by including machine molds, all the conveyors, downstream leak testing, trimming and finishing operations.
“It can all be done and qualified and trained on before the machine ships to the customer. Prior to this expansion, we did not have the space,” Carr said. “This has been an interesting tool, especially as we work with companies that are entertaining bringing blow molding in-house. Those groups need help, and we are now able and well-positioned to do that.”
London said larger Bekum machines with automation are more often purchased as part of a complete work cell. Being able to set up and demonstrate the complete work cell in Williamston reduces start-up surprises when it is delivered to the customer.
Bekum builds some automation equipment in-house. “We will build the automation to the point where the container is finished with full trim specs and set on a single conveyor,” London said.
Building, innovating in America
While most engineering and design work is accomplished in Germany and Austria, there is also collaboration. At NPE, Bekum introduced a tri-layer extrusion head that can be ordered on a new machine or retrofitted to older machines. The unit was designed and built in Europe, but the retrofit package was created in Williamston.
“The retrofit package includes how that head is mounted and supported with vertical extruders,” London said. “There is a lot of weight on the barrel, so we had to engineer support systems and then the control interface. There is a separate satellite retrofit cabinet for that.”
Bekum builds all-electric, hydraulic and hybrid extrusion blow molders. “We offer it in every flavor that a customer might want,” London said. “We are trying to be as accommodating as we can and provide what works best for them.”
Bekum introduced its first fully electric blow molding machine in 2007. In 2010, it patented the C-frame closing unit for electrical and hydraulic machines; in 2017, it developed a stable process for blowing PET handled bottles; and in 2018, it introduced the first magnetic quick-change system for blow molding machines.
Manufacturing at the Williamston plant — fabrication, machining, electrical assembly, painting and engineering — is vertically integrated. “We are clearly buying raw materials,” London said. “Depending on the workload, we are buying some finished assemblies or machined assemblies from the outside, but internally we first fill here and then overflow to the outside.”
Bekum America was established in 1979. The campus covers 42 acres, and there is plenty of space to expand the plant again.
The new addition is equipped to build the larger XBlow industrial machines as market conditions warrant. These are currently built in Austria.
Equipment made to last
Bekum has sold an estimated 18,000 extrusion blow molding machines worldwide, and London said that in the region covered by Bekum America — which he defines as being from the North Pole to the Panama Canal — there are machines still running that were built in the 1960s. London estimates about 3,500 are currently operating in North America.
“Buying a machine from Bekum means a customer has nearly lifetime support for that machine,” London said. “We sell them parts and upgrades. If older parts are not available, we work with them to upgrade their machines.”
Bekum America has a unique approach to after-sale customer service. There is an in-house team that deals with spare parts, replacement parts and MRO parts as well as machinery upgrades and rebuilds. There is also a service department for phone consultations and visits to customers’ sites. Both of those departments are available around the clock.
“The one unique feature we have is that nearly every machine builder, electrician supervisor or manager has traveled on behalf of service,” London said. “If there is a unique problem, it is not uncommon for us to take a machine builder or supervisor to the customer’s plant.
“We say, ‘You helped build it. Go out and take a look. They are having this and this issue,’ ” London said. He estimated 90 percent of the machine builders and 100 percent of the engineers have traveled to customers’ plants. The applications group also visits customers.
“It is really part of the fabric of Bekum,” London said.
The service team generally participates in machine runoffs. “This makes sure they are personally familiar with the customer and the project,” London said.
Carr said the reputation for service “is one of Bekum’s pillars. That’s one of the biggest reasons for our success in North America.”
Family-owned and managed Bekum has about 350 employees worldwide, with 109 in Williamston. London said there are currently about 20 openings here.
Training the next generation
Bekum America established an apprenticeship program in 1995 to recruit high school juniors and seniors interested in manufacturing trades. Apprentices work during the day and attend Lansing Community College at night, and must maintain at least a B in all courses. Graduates of the 8,000-hour program receive a journeyman’s certificate.
London said more than 25 percent of Bekum’s manufacturing workforce is composed of graduate apprentices.
The apprenticeship program helps lower the average age of the skilled trades workforce. “We are looking to develop the next generation of leaders, whether it is through personal coaching or training,” London said. “The next generation of leaders is already getting training and skills they are going to need in the future, and the senior team brings them into the decision-making process.”
London said the company is not contractually obligated to offer apprenticeship graduates a job, “but we’ve never sent one away,” he said. “I mean, they are already employees. Many have already bought their first house by the time they graduate. In four years, we see a big maturity change.”
The program takes in four to six new apprentices each year and typically half graduate four years later.
The apprenticeship program has been operating for 25 years.
“It is quite frankly a differentiator, and I think it is what businesses need to do,” London said. “We can wait for a government program to find us qualified workers, but I think if you want to have a long-term future, you need to embrace this and say we are going to get employees who know exactly what we need them to know to do their jobs.
“There are a lot of benefits,” he said. “It is an expense, but the reward is much greater.”
Carr said the company is well-equipped for the future. It has a strong position in the agricultural chemicals and industrial packaging markets, and is known for its machines that can manufacture high-quality packaging with uniform necks and multi-layer materials.
“Bekum is building premium equipment of the highest standard, so we tend to do really well in demanding market applications,” Carr said.
Other strong markets are pharmaceuticals, personal-care and food and beverage packaging.
One interesting new project is a handled PET bottle with a PCR layer for premium olive oil. “That’s still untapped territory for extrusion blow molding,” Carr said.
Contact:
Bekum America, Williamston, Mich., 517-655-4331, www.bekumamerica.com
Ron Shinn | Editor
Editor Ron Shinn is a co-founder of Plastics Machinery & Manufacturing and has been covering the plastics industry for more than 35 years. He leads the editorial team, directs coverage and sets the editorial calendar. He also writes features, including the Talking Points column and On the Factory Floor, and covers recycling and sustainability for PMM and Plastics Recycling.
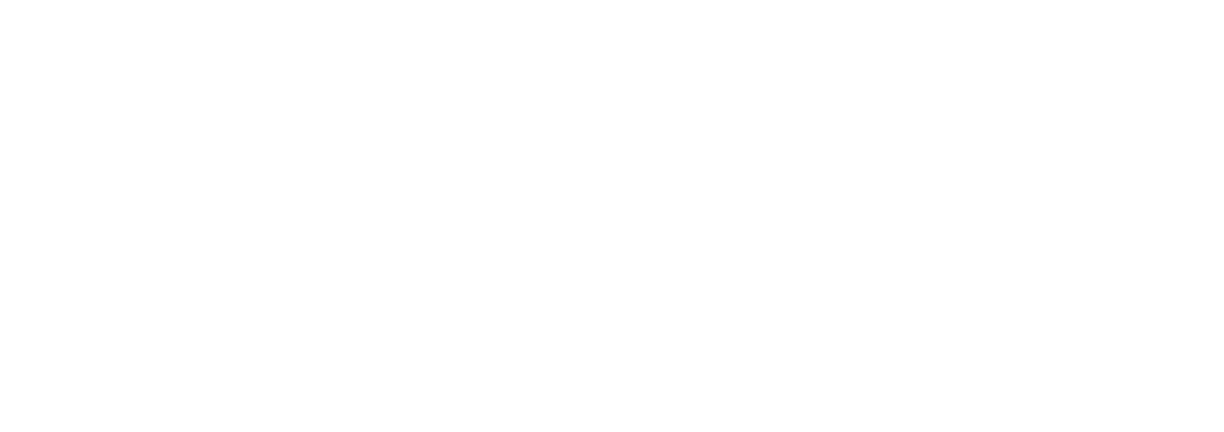