By Ron Shinn
Nissei ASB unveiled three new blow molding machines at K 2022 — a 1.5-step injection stretch blow molding machine, a double-layer stretch blow molding machine and a vertical clamp compact preform machine.
The PF36/9-12000 is the 1.5-step injection stretch machine that is based on the popular PF36 series launched in 2019. Nissei ASB pioneered the 1.5-step technique, which combines elements of one-step and two-step molding techniques into a single system.
At the show, the machine molded 12-liter, bag-in-box water containers that weighed about 120 grams each. Output was 1,540 bottles per hour. Cube-shaped, recyclable bag-in-box water containers in 12-liter and 9-liter sizes are popular in Japan, where Nissei is based, and Nissei ASB says it is a leader in machines to manufacture them.
The bags fit inside a cardboard box.
The demonstration molded nine preforms per injection cycle and blew three bottles at one time. Injection molding typically takes about three times longer than stretch blow molding.
Nissei ASB said the PF36/9-12000 can mold the containers with 35 percent less equipment cost, 70 percent less floor space and 60 percent less energy. PF36 models are suited for producing PET bottles from 100 milliliters to 5 liters, while the new PF36/9-12000 expands the range from 5 liters to 12 liters.
The second machine making its global debut at K 2022 was the ASB-12M-2INJ, a one-step double-layer injection stretch blow molder. ASB’s patented double-layer molding process enables containers to be molded with an inner and outer layer in the body and/or neck sections in a variety of thicknesses, configurations, molding order and resins.
The ASB-12M-2INJ, which is based on Nissei ASB’s best-selling ASB-12-M model, features twin injection units and a six-station rotary table that creates two separate injection and cooling stations. This arrangement makes it possible to use different materials for the inner and outer layers.
The machine was shown at K 2022 making an air-less pump container. As the contents of the container are dispensed by a pump-spray that prevents air from re-entering the bottle, the inner layer of PP delaminates from the outer PET layer and collapses with the product. The 300-milliliter container had a total weight of 28.5 grams, which consisted of 22.8 grams of PET and 5.7 grams of PP. Output was 410 bottles per hour.
Nissei ASB said another typical application is production of food-grade containers using virgin PET for the inner layer that touches the food and recycled PET flake for the outer layer. The outer layer comprises 70 percent of the container’s total weight.
The third new machine was the PM-100/111N preform injection molding model. It is the first in the company’s PM-100 series. The series is aimed at the manufacture of high-quality preforms in small to medium-sized quantities.
It utilizes vertical clamping with mold indexing conducted by a rotary table traversing through injection, cooling and ejection stations. The three operations are carried out simultaneously. Each station uses lip cavities to hold preforms by the neck until they are finally ejected.
Injection molding is in a three-row configuration with a choice of 18, 24 or 36 cavities. Cooling occurs on both the inner and outer surfaces. Further cooling can take place at the ejection station, if needed.
Preforms can be ejected to an optional conveyor or by robot. Two injection screw diameter options and two machine daylight options are available.
The PM-100/111N was shown molding a 28mm “Alaska Neck” PET preform weighing 13.5 grams used for mineral water. Output was 14,700 parts per hour.
A fourth machine in the Nissei ASB booth was the established HSB-4N, a double-blow heat-set reheat blow molding machine that is interesting nowadays because of the growing demand for returnable and refillable water bottles.
A single HSB-4N machine can produce up to 20 million refillable PET bottles per year, according to Nissei ASB, with each having a lifetime of more than 25 cycles, which represents the equivalent of 500 million single-use bottles. At the end of life, refillable PET bottles can be bottle-to-bottle recycled or converted into recycled PET for other products.
Ron Shinn, editor
Contact:
Nissei ASB Co., Smyrna, Ga., 404-699-7755, www.nisseiasb.co.jp
Ron Shinn | Editor
Editor Ron Shinn is a co-founder of Plastics Machinery & Manufacturing and has been covering the plastics industry for more than 35 years. He leads the editorial team, directs coverage and sets the editorial calendar. He also writes features, including the Talking Points column and On the Factory Floor, and covers recycling and sustainability for PMM and Plastics Recycling.
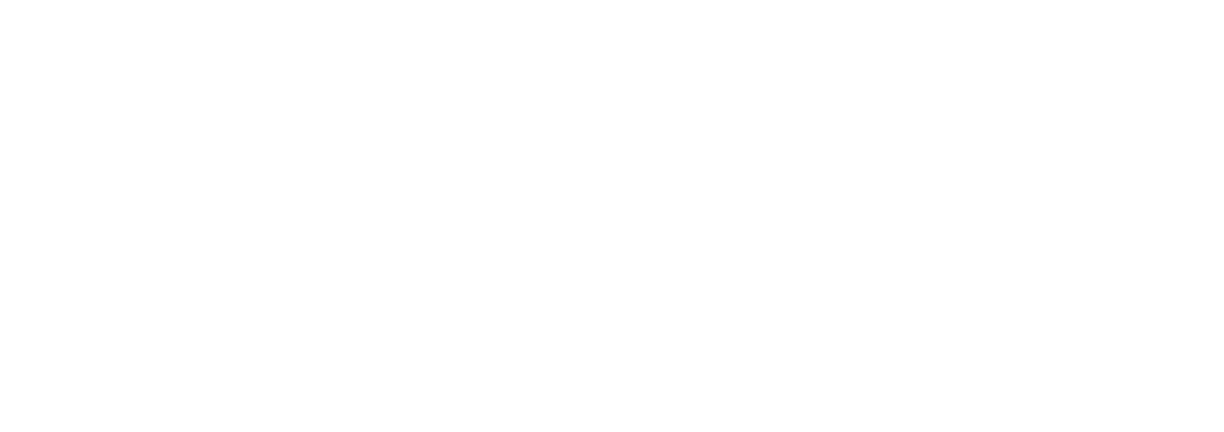