Processors’ attitudes about worker health and safety have evolved significantly over the past 50 years, said Dave Calderone, president of Alternative 4 Plastics LLC, a business coaching and consulting firm that serves blow molders.
Calderone has more than 50 years’ experience working in plastics processing, and he was a plant manager for a blow molding operation by the age of 25. Today, he uses his experience to provide training seminars, technical consulting services and management coaching. While he doesn’t claim to be an expert on health and safety, Calderone dealt with those issues for decades as a plant manager.
He said companies today place a much greater emphasis on employees’ health and safety. As an example, he points to greater concerns about indoor air quality.
When Calderone began working in blow molding plants, there frequently was a heavy stench in the air that saturated his clothing and skin. When he came home in the evenings, his wife would complain about the smell. Calderone joked that to him, it smelled like money.
“There was always an odor or smell that came off the resin as we extruded it in the late ’60s and ’70s,” Calderone said. “Nobody really thought it was harmful. We never really did much about it. We just let it go, and if the plant was running vinyl, the whole plant smelled like vinyl.”
Changes were introduced in the early 1980s when people started realizing that those chemical odors could be harmful, and OSHA began establishing worker safety standards. It started with the installation of vacuum hoods over extruders, when necessary, and modern plants have improved air circulation and quality.
In recently constructed plants, air handlers bring in more fresh air from the outside, which reduces the need for hood vents.
“They’re much more aware today than they were in the late ’60s,” Calderone said.
In addition, equipment has become safer with improved lockout/tagout systems that, for example, better protect workers from accidentally having body parts crushed while servicing the equipment. Unless the clamp is locked in place so it cannot move, locking mechanisms prevent access through a gate or door. Today’s lockout mechanisms include redundancies such as electric switches, hydraulic valves and air valves, Calderone said. Early lockout mechanisms typically included only a single switch, which could fail.
Another improvement within the past 25 years has been light curtains to protect humans from dangerous machinery including robots, winders and palletizers. If a person moves too close and breaks the light curtain’s photoelectric beam, the system will shut down the machine.
“Some of the very large equipment has light curtains so if you break the light curtain, the machine will kick off, and they’re usually 4 to 5 feet away from the machine,” Calderone said.
Trimming or deflashing plastic parts after they are molded also has become safer thanks to robotics.
“Now, they have automation to do some of that trimming that we used to do,” Calderone said. “They take the human part out of it so that they don’t get hurt.”
In some cases, a robot will remove a finished part and place it into a stamping machine that is designed to trim parts.
Employers have come to realize how easy it is for employees to become seriously injured, Calderone said.
“The one thing about the [plastics] industry is that you get either a little cut on your finger or you lose your finger,” he said. “There’s no kind of middle of the road for somebody to get hurt.”
In the blow molding industry, a gradual adoption of all-electric machines also is expected to improve safety, Calderone said.
While adoption of all-electric machines, in the place of hydraulic models, has been slow in the U.S., it holds the promise of reducing accidents from slipping and falling, Calderone said. The changeover has been more rapid in Europe.
“It helps because you don’t have hydraulic oil leaks to worry about,” Calderone said.
Calderone, whose services include management coaching, encourages plant management to place a high value on worker safety and happiness.
“I think that a lot of companies have started to realize: ‘Hey, we need to pay more attention to this. We need to make their job easier. We need to make it safer. We need them to be happy when they come to work.’ ”
Contact:
Alternative 4 Plastics LLC, Murfreesboro, Tenn., 615-785-4226, https://alternative4plasticsllc.com
Bruce Geiselman
Senior Staff Reporter Bruce Geiselman covers extrusion, blow molding, additive manufacturing, automation and end markets including automotive and packaging. He also writes features, including In Other Words and Problem Solved, for Plastics Machinery & Manufacturing, Plastics Recycling and The Journal of Blow Molding. He has extensive experience in daily and magazine journalism.
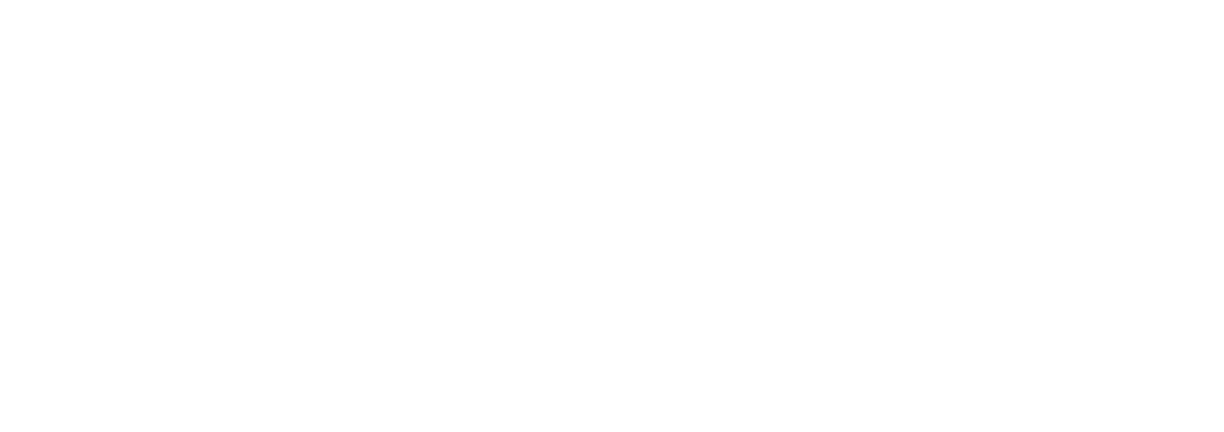