Wilmington Machinery two-wheel rotary blow molding machine boosts efficiency
Wilmington Machinery has rolled out a new dual rotary blow molding machine distinguished by a unique wheel-and-rail system that makes it more versatile than other systems and reduces downtime.
The MSBW60-DC, which consists of two wheels with a common extruder, die head and trimming components, reduces the time required for mold changes and allows one set of molds to be serviced while a second is in operation.
Wilmington developed the machine after a customer asked for a blow molding line that could produce two bottles with significantly different capacities at rates of up to 600 bottles per minute.
“We considered several approaches, including two totally separate machines that would feed a common trimming system, but that got to be pretty pricey,” Wilmington Machinery President Russ LaBelle said. “That’s what gave birth to the dual wheels where you leave the setup in there.”
LaBelle said he is unaware of any other commercially available blow molding machine like it. Molds for the machine are installed on two wheels, which can accommodate molds for bottles of different sizes or shapes.
By using a rail system, users can quickly and easily roll one of the wheels out of place, then roll the second wheel into place, reducing setup time from one bottle size to another by as much as 75 percent, according to the company. The wheel that is not in use can be rolled off to the side on the track system, and users can perform maintenance on it while the blow molder remains in production. The wheels have quick disconnects for electrical, water and pneumatic services, reducing wheel set-up time to minutes rather than several hours.
The quick wheel change also reduces downtime and labor costs, and the design assures correct mold setup.
If production volumes increase, both wheels can operate simultaneously with some retrofits, including the addition of a second extruder and additional trimming equipment. This would minimize the investment required for a second production line.
“We had to apply ourselves to make this affordable,” LaBelle said. “There is a premium of about 15 to 20 percent over and above the single wheel with two sets of molds. Now, what it’s all about is the amount of time that is saved in going from one bottle size to another. It makes it more versatile. Anyone in today’s world is interested in saving production time and getting greater utilization out of their investment. … Time is money.”
Both wheels on the MSBW60-DC feature 60 mechanically actuated clamping stations with single- or dual-cavity molds.
The line provides 1 ton of clamping pressure and can produce up to 600 bottles per minute in sizes of 1 ounce to 10 ounces that are suitable for single-serving beverage, personal-care and chemical products. However, the design could be employed to build larger blow molding machines with up to 10 tons of clamping pressure for making containers with capacities of up to 2.5 gallons.
“This technology could be carried forward to any of those sizes,” said Jim Boos, VP of sales and marketing.
Contact:
Wilmington Machinery Inc., Wilmington, N.C., 910-452-5090, www.wilmingtonmachinery.com
Bruce Geiselman
Senior Staff Reporter Bruce Geiselman covers extrusion, blow molding, additive manufacturing, automation and end markets including automotive and packaging. He also writes features, including In Other Words and Problem Solved, for Plastics Machinery & Manufacturing, Plastics Recycling and The Journal of Blow Molding. He has extensive experience in daily and magazine journalism.
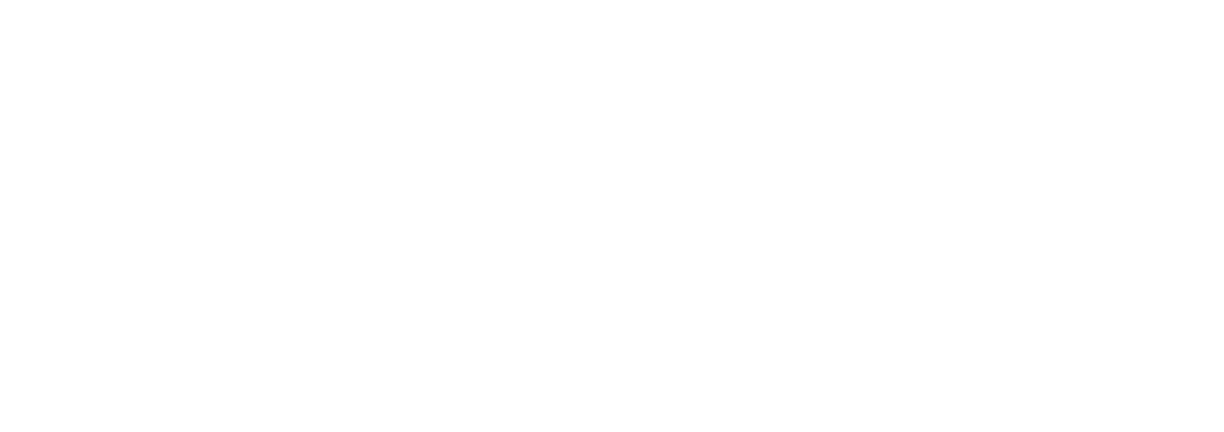