By Bruce Geiselman
Blow molders have been on a years-long quest to lighten their containers. Consequently, opportunities for making big weight reductions are few, but work continues on incremental improvements to foaming technologies, machines and process control, as consumer demand for sustainable packaging remains a driving force in lightweighting.
W. Müller USA
“Lightweighting has been a trend in packaging for decades, but consumer demand for sustainable products and packaging has brands and processors demanding more. Our foaming technology is that more,” said Elijah Harris, marketing and sales coordinator for W. Müller USA, a manufacturer of extrusion blow molding die heads.
A few years ago, W. Müller sold its first foam-extrusion head for blow molding three-layer bottles with a foamed inner layer to a client in Paraguay. Interest in foaming continues to grow as consumer product manufacturers look for ways to boost recycled content in their bottles, Harris said.
“Because domestically there is a lack particularly of [post-consumer] polyethylene for blow molding, the easiest way to reach those percentage targets is by reducing the weight of your container. I think that is a big driving force on why you see container weights going down.”
End consumers’ concerns about plastic waste and recycling are spurring changes.
“We’re seeing with society’s newfound role as environmental stewards, a lot of the driving force for more sustainable packaging is coming directly from the consumer,” Harris said. “Their purchasing habits are affected directly by the sustainability of a product and its packaging. This is a fact … The Unilevers and the Procter & Gambles, they get it. They understand these trends amongst their consumers, and they make those demands of their packaging suppliers.”
Equipment OEMs like W. Müller have several technologies that can help reduce the weight of blow molded packaging.
“The first and most prevalent one is being able to have what we call wall-thickness control,” Harris said. “The main culprit behind weight in blow molded packaging besides the packaging design is the thickness of the wall. We have technology that’s equipped on … our heads that allows you to control where in the part you’re placing the plastic, so you can make the wall thinner or thicker based on if you need an area to be more supportive.”
The extrusion die heads can produce a thicker wall in areas of the parison that need more reinforcement or rigidity, and a thinner wall elsewhere to save as much material as possible.
The technology has been available for decades, but newer design trends are leveraging these capabilities, Harris said.
“Now that lightweight containers and using less material is such a deep concern for the container manufacturers, we’re starting to see this become more and more popular,” Harris said.
However, there are limits as to how thin rigid packaging can be made. If the walls are too thin, the packaging becomes flexible.
“I think foaming is that next big step where you can keep your rigid wall thickness but reduce weight,” Harris said.
Foaming — generally used to create an inner layer that is surrounded by two rigid outer layers — typically can reduce packaging weights by 15 percent to 30 percent, Harris said. That’s based on the company’s testing and “the results may vary,” he said.
Foaming also can result in a 50 percent increase in top-load strength, which is important when stacking products, Harris said.
W. Müller’s foaming technology is mechanical and not chemical, which is an advantage in terms of the degree of control, ease of maintenance and not having to worry about contamination. The company’s static mixer injects nitrogen and talc into the resin to induce foaming.
Manufacturers of bulk containers and automotive parts also are using foaming technologies to make their products.
“The current application for a lot of plastic foaming technologies is under the hood because it has more than just the advantage of weight saving,” Harris said. “You also get better sound buffering, and you have better resilience in compression. There also are thermal advantages.”
Since blow molded foamed parts have less mass, they absorb less heat and don’t retain the heat for as long, he said.
Foamed parts particularly lend themselves to use under the hood because automakers don’t have to worry about the appearance of the part. Instead, they can concentrate on making the part as light as possible.
Graham Engineering
Graham Engineering, which makes blow molding machines, American Kuhne extruders and Welex sheet extrusion systems, has a slightly different perspective on lightweighting.
While interest in lightweighting packaging products continues, it spiked about 10 years ago, according to the company.
Most blow molders would like to reduce weight because it reduces costs, but in packaging, specifically, performance specifications and consumers’ lack of acceptance of lighter products frequently limit the opportunities, Graham Engineering said in a written statement.
“For consumer packaged goods, we saw interest in lightweighting peak in the first half of the last decade as the prices for most resin grades rose to historic levels,” the company said. “There is still ongoing interest, though not at the same pace. More frequently, we see customers focused on the intersection of package design and performance to inform the optimal weight with a high focus on consumer reaction to package aesthetics and shelf appeal. Customers will lightweight if the aesthetics are met and any design requires marketing approval.”
Outside of consumer packaging, for example in industrial parts, Graham Engineering has seen performance as the key driver.
“There is also a higher emphasis on consuming recycled materials and reducing waste,” according to the company. “Utilizing post-consumer regrind has become a higher priority than weight reduction.”
Graham Engineering has decades of experience working with customers’ package designs and can typically reduce the weight of a part by 15 to 20 percent by optimizing its design for production on a rotary-wheel extrusion blow molding system.
“The proprietary design of our systems includes up to 180-point parison programming to optimize material distribution within the mold and a captive (vs. hanging) parison for greater control of the process,” the company said.
Precise process control, such as is available on a Graham Engineering rotary-wheel extrusion blow molding system, is a key to offering weight savings, the company said.
Jackson Machinery
U.S. blow molders are falling behind European companies in terms of lightweighting their products because many aren’t investing in new equipment, said Bob Jackson, owner of Jackson Machinery Inc., a manufacturer and distributer of blow molding machines that also refurbishes equipment.
Blow molders always have had an incentive to produce lightweight products because it reduces their material costs, Jackson said. That means blow molders have been doing the best job possible to lightweight products with the equipment they have.
New equipment — with improved hydraulics or all-electric operation — offers better process control and the ability to produce thinner products with consistent wall thicknesses.
U.S. sales of blow molding machines have declined since 2000, Jackson said. He believes the sales decrease relates to growth in the number of blow molding companies owned by private equity firms, firms that are not willing to pay for new equipment that would facilitate lightweighting.
“The newer machines have fancier programmers and newer controls,” Jackson said. “They have proportional hydraulics, which are much faster than the old controls, and, in general, are able to make a better product just because of the changing technology. But machinery people haven’t been buying any machines.”
Proportional hydraulics mean a valve can be partially open, whereas the older hydraulic valves had to be either fully open or fully closed, Jackson said. “The new proportional controls and the hydraulics allow you more control over the machine,” he said.
Some companies are opting to hire Jackson Machinery to rebuild older machines and install upgraded hydraulics and controls, which can give them the same advantages as buying new.
The biggest improvements in terms of production speed, changeover speed and lightweighting can be gained by switching from hydraulic blow molding machines to all-electric blow molding machines.
German and Italian manufacturers now produce almost exclusively all-electric models. But American consumers haven’t been quick to adopt them.
“It’s a much finer control because it’s all servo-driven as opposed to hydraulic-driven,” Jackson said. “You first go through the old bang-bang valves to the new proportional valves, and then you get into the servo drives, and servo drives are much faster and they’re just literally perfect. You get a 12-second cycle. You’ll pick up anywhere from one second to a half second depending on what you’re doing. They’re just all the way around a better beast in every direction we could see, but there doesn’t seem to be much enthusiasm in the marketplace to go out and do what all of Europe has done.”
One of the factors discouraging the purchase of all-electric machines is a higher price tag than a comparably sized hydraulic unit.
Jackson Machinery recently became the North American distributor for Alphamac, an Italian equipment manufacturer whose products include electric blow molding machines.
For more information
Jackson Machinery Inc., Port Washington, Wis., 262-284-1066, www.jacksonmachinery.com
Graham Engineering Corp., York, Pa., 717-848-3755, www.grahamengineering.com
W. Müller USA Inc., Agawam, Mass., 413-787-0664, www.mullerheads.com
Bruce Geiselman
Senior Staff Reporter Bruce Geiselman covers extrusion, blow molding, additive manufacturing, automation and end markets including automotive and packaging. He also writes features, including In Other Words and Problem Solved, for Plastics Machinery & Manufacturing, Plastics Recycling and The Journal of Blow Molding. He has extensive experience in daily and magazine journalism.
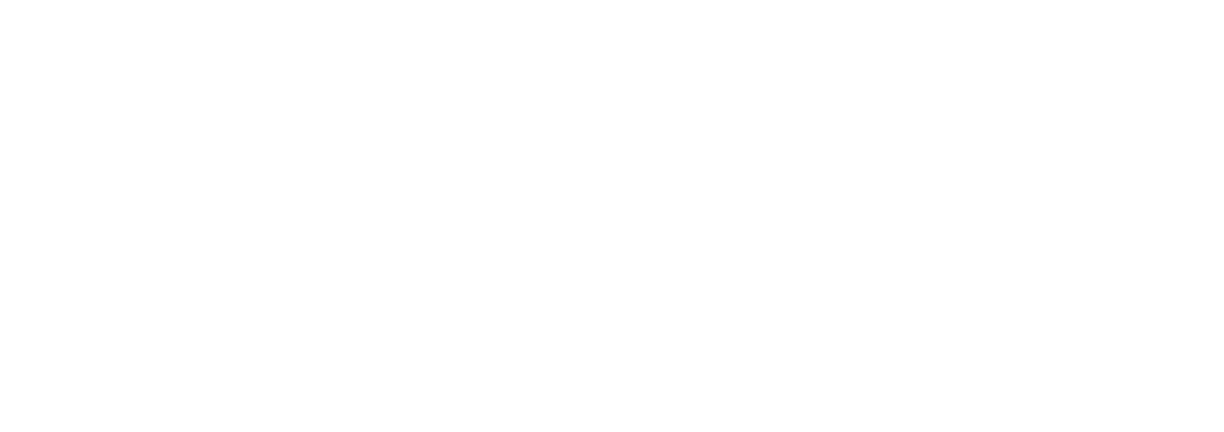