Whether the job requires handling entire cars or small, sophisticated parts such as syringes, Yaskawa's newest robots are ready to answer the call.
In September, the company introduced several robots and advanced technologies at the International Manufacturing Technology Show in Chicago.
MOTOMINI
"We showed our mini-robot [the MotoMini], which is a small, one-half-kilogram-payload robot that is brand-new for us," said Dean Elkins, segment leader for materials handling at Yaskawa Motoman. "I see that [being used] in some pre-process or upstream applications like insert handling and insert staging in the injection molding industry.
"I also look at it in some post-process applications where we might be looking at kitting or part placement or in the blow molding industry, the handling of shots and things like that. There is some play there. I also see it as very useful in applications like plastic syringe handling."
Yaskawa bills the MotoMini as the smallest and lightest six-axis robot in the industry. Weighing only 15.4 pounds, the MotoMini is easy to carry and ideal for tabletop-, floor-, ceiling- and wall-mounted installations. According to the company, it is 20 percent faster than comparable small robots, reducing cycle times and boosting productivity. Its 1.1-pound payload supports a variety of tooling and sensors to perform various tasks.
Internal cabling and air lines minimize interference with other equipment and improve safety.
A compact footprint, measuring 7.5 inches by 4.9 inches, allows the robot to be mounted close to machinery in existing production lines or cells.
In addition, the robot operates quietly, producing less than 65 decibels when operating at maximum load and speed.
Its applications include assembling, dispensing, inspecting, kitting, machine tending, materials handling, packaging, parts feeding and sorting.
The MotoMini uses Yaskawa's new YRC1000micro controller, which minimizes installation space and optimizes performance. Its small footprint and lightweight cabinet are ideal for factories with high-density layouts, where stacking of controllers may be required, according to the company. The controller can be installed horizontally or vertically, or on a 19-inch rack.
The YRC1000micro controller, which comes with the MotoMini, also is compatible with Yaskawa's GP7, GP8, GP12 and HC10 robots.
MH900
The heavy-duty, long-reach MH900 robot is the latest addition to Yaskawa's line of materials-handling robots.
Designed and assembled in the U.S., the MH900 has a 1,984-pound payload capacity, a 15.3-foot horizontal reach and a 20.3-foot vertical reach to accommodate a range of heavy components, including car frames and agricultural equipment.
The MH900, while larger than most injection molding operations would need, could be useful to companies that are 3-D printing entire car bodies, for example, Elkins said.
The MH900 is a full six-axis robot with heavy-duty bearings that provide smooth arm rotation. It is floor mounted, and cables and air lines are routed through the robot base to the upper arm to increase cable life and enhance safety, the company said.
SMART PENDANT
Another new feature from Yaskawa is its Smart Pendant with an easy-to-use touch screen for programming.
"It is a much more intuitive, conversational programming pendant than we have ever had before," Elkins said. "We have a feature called Smart Frame. It allows the operator or the programmer, by using four arrow keys, to move the robot left, right, forward or away in English rather than in some higher-level programming language."
The controller screen displays arrows that are marked with the direction of their movement, he said.
"When you are standing in front of a robot, by hitting these four arrows, the robot will move toward you or away from you. That really helps make programming less sophisticated."
Smart Frame's patented technology determines the user's orientation relative to the robot, according to the company. This eliminates the use of conventional coordinates and uses intuitive natural language directions for easy command of robot movement, the company said.
It can be used with the YRC1000 controller on Yaskawa's GP7, GP8 or GP12 industrial robots, according to the company's website.
YASAKAWA COCKPIT
Yaskawa Cockpit is a new software platform that monitors, collects and visually delivers operational data in real time for networked equipment throughout a production facility.
"It's a great step for us in meeting the demands of IoT and Industry 4.0," Elkins said.
It gathers information related to overall equipment effectiveness, alarm histories and maintenance. It helps manufacturers optimize planning by making data-driven decisions and maximizing efficiency, the company said. The information can be easily forwarded to existing enterprise- resource-planning, manufacturing-execution-system or artificial-intelligence software.
It can be set up to monitor the functioning of robots and can use sensors to track other operations in a manufacturing cell, Elkins said.
"In plastics, you could look at the amount of resin in an injection molding machine; you could look at the number of sprue cuts a robot has performed; you could look at how many parts have been extracted," he said. "It has counter functions to look at anything you want to set up from a production-flow standpoint."
Bruce Geiselman, senior staff reporter
Contact:
Yaskawa America Inc. Motoman Robotics Division Miamisburg, Ohio, 937-847-6200,
Bruce Geiselman
Senior Staff Reporter Bruce Geiselman covers extrusion, blow molding, additive manufacturing, automation and end markets including automotive and packaging. He also writes features, including In Other Words and Problem Solved, for Plastics Machinery & Manufacturing, Plastics Recycling and The Journal of Blow Molding. He has extensive experience in daily and magazine journalism.
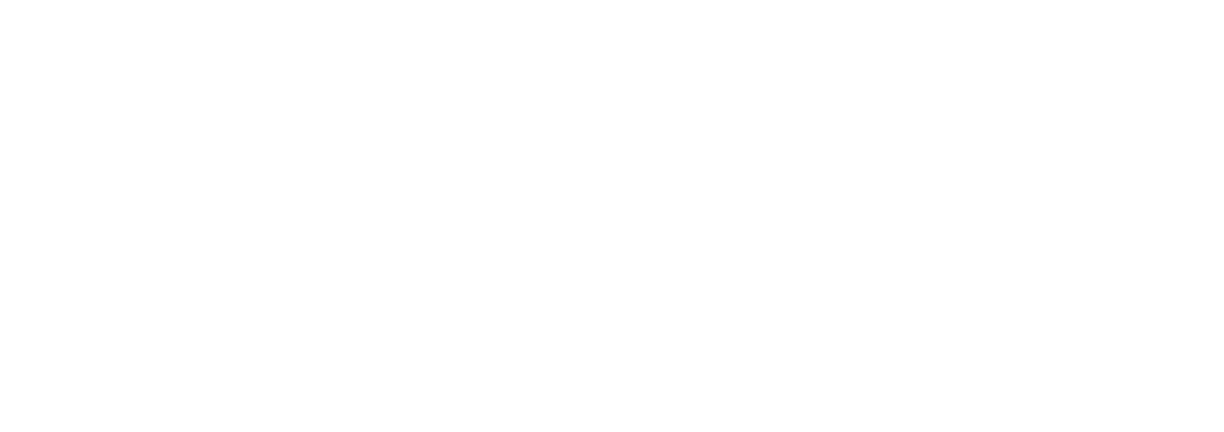