Alpha Laser which makes lasers that can be used for mold and die repair, has updated a mobile robotic laser system designed for targeted laser hardening, welding or repair of metal surfaces.
The AL-Rock has a caterpillar track, giving users the ability to move it to a tool or die, rather than having to move the tooling to the system to perform heat treatments or repairs, said Wesley Wheeler, sales manager at Alpha Laser US. Recently, the company added a vision system to the AL-Rock as a standard feature, allowing users to scan parts in order to program the robot to perform specific repairs.
The ability to heat-treat a precise, localized area of a tool or die significantly reduces downtime compared to the conventional process that requires dismounting the tool and moving it elsewhere.
As an example, Wheeler described the difficulties a large-parts maker might encounter in moving a mold for repairs.
"A manufacturer of an automotive fascia mold producing a car bumper may have a tool that is huge dimensionally and weighs 30,000 pounds for each mold half," he said. "Instead of dismounting and transporting that tool to a traditional heat treater where then the entire mold sits in an oven to be heat-treated, the AL-Rock laser works on the tool onsite to harden a specific area of the tool, such as the parting line/shutoff, leaving the remainder of the tool untreated."
The AL-Rock can be used with any tool steel or alloyed metal, as well as aluminum, cast iron, nickel-based materials and stainless steels. It can heat-treat, weld or repair dissimilar metals, he said.
Alpha Laser's laser systems have CNC capabilities that allow production and high-volume welding and hardening processes to be completed quickly and with precision. The company said laser welding is appropriate for any task that could be performed by traditional tungsten-inert-gas (TIG) welding, but it delivers better results, greater repeatability and higher productivity. The process is applicable for areas as small as 0.004 inch.
MOVEABLE LASER UNIT
AL-Rock's wide, sweeping robot arm easily reaches even the most challenging areas in a workpiece. The laser beam — which can be up to 1 inch wide — precisely follows workpiece contours and can be applied along complex closing edges, scars or single points.
Mobility is just one benefit offered by the AL-Rock. Versatility is another advantage, Wheeler said. Although it is primarily suited for localized hardening, the AL-Rock can also be used for laser-powder-deposition welding or for build-up welding using welding wire. It is also suited to cladding deposition, used to enhance, restore and strengthen the surface of a metal component.
The AL-Rock has interchangeable heads that each perform a distinct operation — laser welding, laser cladding or laser hardening. The AL-Rock controller displays the controls and parameters for use with each head.
The AL-Rock has several unique features. For example, unlike most of the laser units manufactured by Alpha Laser, which work with 50- to 90-watt lasers, the system uses a 3-kilowatt fiber laser. "AL-Rock is not built for extremely tiny accurate welding, but rather for production process welding, large molds and larger tooling," Wheeler said.
AL-Rock also incorporates a special pyrometer system that measures the temperature of the laser. It controls how much power is applied to the laser to deliver a consistent operating temperature. When the laser reaches the desired temperature, the pyrometer system backs the power down. "This is unique. Other laser-hardening systems do not do this," Wheeler said.
Mikell Knights, senior staff reporter
Contact:
Alpha Laser US Meadville, Pa., 814-336-9000,
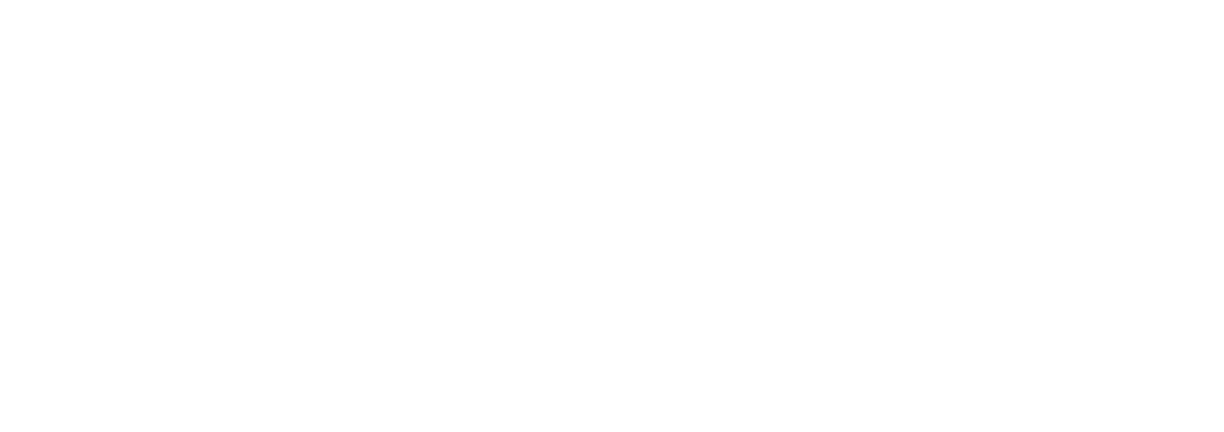