Fourmark Manufacturing, an Oakville, Ontario, custom injection molder, has achieved the holy grail of efficiency by integrating software for machine maintenance management with a real-time plant-floor data-acquisition system.
Since the integration, the company has increased its efficiency rating from 85.6 percent to 92 percent, according to Fourmark COO Tarek El-Sayed, who has been with the company since 2006. Operating equipment effectiveness is based on uptime efficiency, scrap rate and cycle efficiency. Also, the company's rate of completed work orders for routine maintenance increased from 70 percent to 91 percent, he said, and its frequency of repairs dropped by 15 percent because the precise information offered by the integrated system removes all doubt about when routine maintenance is needed.
"Before we had this system, machine repairs often would get pushed back for lots of different reasons," El-Sayed said. "Sometimes, they were good reasons, and sometimes, not so good. This system eliminates any guessing about when repairs are needed."
Fourmark's integrated system combined the maintenance-management software of Coast Systems and the real-time plant-floor data-acquisition technology of Syscon International and its Syscon-PlantStar division. With the data collected from Syscon, Coast's software provides maintenance insights. The project was the first time the companies have joined forces to offer an injection molding company an integrated system, according to executives from both firms.
"The benefit of this system is that it's based on equipment utilization," said Jerry Sherman, managing partner at Coast, which specializes inmaintenance-management software for the plastics industry. "Manufacturers save money by not doing maintenance when it's not needed. You don't want to do the maintenance too often and waste money, or worse, do it too infrequently, which can lead to costly breakdowns."
Syscon-PlantStar's data-collection modules provide a complete picture of various manufacturing processes. Backed by state-of-the-art processors, the web-enabled modules present information on industrial-grade touch screens that offer flexible configurations.
SETTING THE STAGE
Fourmark was a long-time customer of Syscon before it began working with Coast, according to Gary Benedix, VP of sales at Syscon International.
Using third-party sensors on machines, the Syscon-PlantStar system provided Fourmark with a wealth of production information, including scheduling, product specs, uptime hours, cycle efficiencies, downtime hours and time elapsed to fix machines, El-Sayed said.
"It's a live system, so we can take real-time data from the system and make decisions based on that," he said. "It's driven by real numbers, which allows us to improve customer service. We can get real-time information for customers and tell them, for example, 'Your order will be done in 12 hours. Do you want us to ship it then?' It operates seamlessly, and there is no manual data entry. All the data is gathered automatically."
Syscon-PlantStar software tracked the run times and cycle counts of Fourmark's injection molding machines. Syscon-PlantStar later introduced Coast to Fourmark and proposed a full integration to track and manage preventive maintenance (PM).
"Tarek is very forward-thinking and was looking for ways to do more with technology," Benedix said.
"He asked about maintenance-software packages, and the best one we saw was the Coast system. Coast was open to working on an integration system with us for Fourmark. We had not worked before with Coast on an integration system, but we had done other integrations for our customers."
El-Sayed said he was pleased with the Syscon-PlantStar production-monitoring system that Fourmark was using before the integration with Coast.
"Syscon-PlantStar was monitoring all our production lines in real time. It is linked to all our molding machines, which are all updated in real time every 5 seconds," El-Sayed said. "Machine-usage information and optimizing machine capacity are critical to operating efficiently and managing our business."
While the PlantStar system handles production management seamlessly and efficiently, its software does not manage maintenance.
"Our next step was to come up with a TPM [total preventive maintenance] system using all the data offered by PlantStar," he said. "Most PM programs are geared toward standard time. If you don't have a system, you do PM based on the calendar instead of as needed. This could be weekly, monthly, semi-monthly or annually. We did not want to do that. We wanted to base it on operating hours of the molding machines."
He said if a machine is down 15 days, or even only two days, a calendar-based PM program does not make sense.
GETTING STARTED
For Fourmark, the process to combine Syscon's expertise with Coast's was seamless.
"The integration process was very simple," Sherman said. "Once we had Syscon's data-integration information about Fourmark, we used that to track utilization. We captured the total machine utilization incrementally over time. With that information, you can trend utilization. With that trending info, you can forecast the total PM spend that will be needed. You know the time and frequency of machine use, and how much it will cost going forward to maintain it properly."
Syscon-PlantStar and Coast both have access to Fourmark's server, which allowed the two companies to integrate their systems remotely. The implementation did not interrupt operations at Fourmark.
"We kept operating in real time, and they got all the data they needed for the integration," El-Sayed said. "There was zero interruption to our operations."
HOW THINGS WORK
The Coast system is web-based, so it's accessible on mobile devices and laptops. Users can scan QR codes that are assigned to every press and other particular assets at Fourmark. Because it's all software-based and software-linked, Fourmark did not have to purchase any additional machine controls.
"That unique ID allows us to get data from each piece of equipment on any internet device," Sherman said. "When that information is integrated with Syscon-PlantStar, Syscon can get that information also. This useful information can be integrated across multiple environments and platforms."
Plant-floor data from Syscon-PlantStar is dumped into the Coast maintenance system and is updated automatically, according to El-Sayed.
"We put in triggers based on PM," he said. "Many maintenance systems have manual sheets to manage multiple machines, which are based on hours run. But you need people to accurately collect and enter the data. That requires extra people and is open to human error. Before implementing the integrated system, we were operating off Excel spreadsheets and an active database."
With the integrated system, Fourmark can track the cost per machine, frequency of repairs on machines, total costs, repairs by suppliers, parts usage and cost per part, El-Sayed said. And, while the company is not yet using the system to track labor costs, it plans to do so in the future.
"Now we have optimized systems to keep maintenance costs in line. We are getting all the data we need at the time we need it with minimal human interaction. Every morning, it automatically tells me which machines need PM every day. We can monitor the performance of the maintenance and engineering teams. How many PMs were done versus how many were generated? Are we staying on track or falling behind? It illustrates all the gaps that we need to fill."
In addition to reviewing all the injection molding machines and giving reports on each one, the integrated system monitors the condition of the machines on a real-time basis. It offers capital equipment planning data, he said. Such data provides insights into when to update, upgrade or replace machines, as well as the appropriate timing of maintenance.
The integrated system tracks Fourmark's 23 presses, as well as all of its approximately 100 molds, El-Sayed said.
LESSONS LEARNED
El-Sayed has some advice for companies that want to improve their operations through an integrated data acquisition and maintenance system. They first need to understand the technology that's available and how it can help them achieve their goals.
"Look at the results you need, and go backwards from there," El-Sayed said. "Look at companies that are reputable and can give you what you need. Collaborate with other smart, innovative companies that offer great customer service. Don't try to reinvent the wheel."
Bruce Adams, contributing writer
Contact:
Coast Systems, Brooksville, Fla., 877-262-7801, www.coastsystems.com
Fourmark Manufacturing Inc., Oakville, Ontario, 905-855-8777, www.fourmark.com
Syscon International Inc.,
South Bend, Ind., 574-232-3900,www.syscon-intl.com
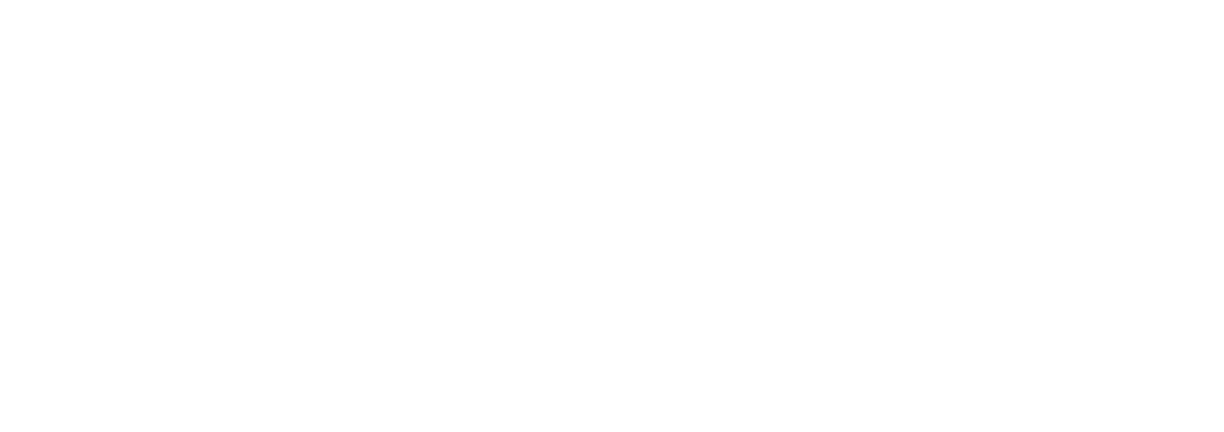