Manufacturers of size-reduction equipment for plastics processors introduced new granulator lines as well as upgraded granulators and related optional equipment at NPE2018. Highlights included new sizes of units and user-friendly features.
CONAIR
Conair introduced its new Viper line of granulators at NPE2018; the line replaces a variety of granulators the company offered under various product names.
The Viper line features 18 models, from small press-side units to large central granulators. The Vipers are suited for use with a wide variety of plastics processes, including injection molding, blow molding, extrusion and thermoforming. The press-side machines have rotor diameters of 6, 8 and 12 inches; the central granulators have rotor diameters of 17, 23, 32 and 35 inches. The granulators' maximum throughputs range from 80 pounds an hour to 13,200 pounds per hour.
Conair plans to add larger granulators and specialty units to the line.
"Our objective was to develop a straightforward, uncomplicated suite of Conair-designed machines, suitable for most applications," said Sam Rajkovich, VP of sales and marketing. "We also wanted to make standard as many popular features as possible."
Key features include improved sound insulation and hardened and water-cooled cutting chambers for most models.
The smaller grinders have tangential-feed cutting chambers; the larger units have a super-tangential configuration to accommodate bulky scrap. Three-blade, open rotors are standard, with other rotor designs available. Machines with 12-inch or larger rotors come with cooling channels to prevent overheating that can cause the plastic to smear or melt. "Granulators cause lot of heat," said Dave Miller, GM for size reduction.
Compared to Conair's previous offerings, the Viper units have bigger screens for increased throughputs. All models have screen areas equal to 50 percent of the rotor diameter, allowing the granulate to move through the cutting chamber quickly for higher throughputs with no added horsepower. The bigger screens result in better-quality regrind and fewer fines, the company said. Previous Conair granulators had screens that were about 30 percent of rotor diameter, Miller said.
The scissor-cut rotor and bed knives can be adjusted easily to maintain tight tolerances relative to each other and the screen. For simpler sharpening, they can be adjusted in an outside jig on a workbench, instead of inside the cutting chamber, Miller said.
Maintenance and cleaning are also easier, with the granulators sporting tool-less front access; hinged, tilt-back hoppers; and drop-down screen cradles.
The machines have energy-saving features such as rotating sidewalls, integral roller bearings, a solid flywheel and high-efficiency motors.
They can be configured for manual use or feeding by robot or conveyor. Hoppers can be customized for different material shapes. "Profiles, film and sheet — each requires a different hopper style," Miller said.
Several evacuation options are available. One is a self-powered vacuum motor loader that draws granulate out of the catch bin and deposits it into a gaylord or bin. Compressed air evacuation via venturi also can be used. Lastly, central vacuum systems can empty materials from multiple granulators into a common collection bin. The systems can use positive- or negative-pressure blowers, Miller said.
CUMBERLAND
Cumberland introduced several products at NPE2018: a beside-the-press series of granulators; the X1800-series central granulators; the T50-series central granulators; and its Crusher-brand feed rolls for reclaiming thermoforming scrap.
Cumberland's new line of beside-the-press granulators — the 7, 10 and 16 series — can be integrated with extruders and injection molding machines to process scrap directly inline.
The company is emphasizing several benefits of the beside-the-press line, said Tyler Check, Cumberland product manager for size reduction. They include safety, user-friendliness, application flexibility, durability and performance. The machines are compliant with ISO 12100 safety standards, and the cutting chambers can't be accessed until the rotor stops.
The new granulators have a viewing window, so operators can monitor the material in the cutting chamber, Check said. The cutting chamber has wide-open access for easy cleaning and knife changes. An improved discharge seal minimizes dust and potential regrind leakage, and a larger discharge bin doesn't have to be emptied as often.
Two types of geometries available for the cutting chamber, tangential and offset, are to accommodate different sizes and densities of materials. Additionally, the granulators can be customized with a variety of hopper styles and discharge options that include manual, blower and vacuum discharge.
Cumberland also has added the X1800 model to its X series of central granulators, which is suited for processing large injection molded and blow molded scrap, furniture components and appliance parts. The X1400, which has a 56-inch-wide cutting chamber, previously was the company's biggest machine; the robust X1800 bests that with a cutting chamber that's 72 inches wide. "Sometimes the machines can't handle the size and throughput [of some materials]," Check said. "Now, wider applications can be handled."
The X1800 features dual-tube discharge for improved machine evacuation. It has a throughput of 4,500 pounds an hour and a 150-horsepower motor.
The T50-series granulators made their trade-show debut at NPE2018. They have a 20-inch-diameter rotor and can handle a wide variety of materials, including large injection molded or blow molded scrap, furniture components and appliance parts. The line has three models, with throughputs ranging from 1,500 pounds per hour to 2,500 pounds per hour.
Two types of geometries also are available for the T50's cutting chamber. The tangential design allows the granulators to process parts that are large relative to the size of the machine. The offset design is suited for granulating thick-walled, higher-density parts. The precision- tolerance cutting chambers are designed for regrind consistency and smooth processing.
For easy maintenance, the machines feature a wide-open design. Also, screens are reversible to allow longer use.
The granulators can be configured to a customer's application with specialized hoppers, in-feed designs and options for evacuation.
Finally, Cumberland unveiled its Crusher feed rolls for reclamation of thermoforming scrap.
"Granulators have no means of metering how much material they take in, so if you have a continuous stream of plastic from a thermoforming line, the granulator will pull material into itself as fast as it can," Check said. "This causes the granulator to jam. Feed rolls meter the feed of the granulator and ensure the material is being correctly directed into the granulator."
The Crusher can process parts that are up to 12 inches deep and has a drive system with a 3-horsepower, C-frame motor drive and adjustable air cylinders to allow users to set the minimum roll gap.
RAPID GRANULATOR
Rapid Granulator has come out with a new granulator line specifically for thermoforming scrap.
The ThermoPro series addresses in-line processing of skeletal waste from thermoforming lines. It's available in various standard and low-profile formats for handling scrap widths from 24 inches to 60 inches, the company said.
The ThermoPro machines offer new features designed specifically to make thermoforming operations more cost-effective and efficient.
"Thermoforming companies live or die according to how well they handle and recycle their trim," said Bengt Rimark, CEO with Rapid's parent, Rapid Granulator AB, Bredaryd, Sweden. "Skeletal waste can easily account for up to 30 to 40 percent of their total throughput, so it is critical that the trimmed material is returned to the process as cost-effectively as possible and with the highest quality possible."
The ThermoPro series features an integrated roll feed for constant and consistent feeding of material. That helps lower costs, Jim Hoffman, VP of sales and marketing, said at NPE2018.
The compact design of the roll feed and dancer bar allows skeletal waste to be pulled from the machine in sync with the production line's stops and starts. The roll feed includes a pneumatic pressure control that allows it to adapt to the thickness of the incoming material.
A standard heavy-duty roll feed reduces handling problems of skeletal waste and can feed several webs into the granulator at the same time. The roll feed also facilitates granulation of scrap when a thermoforming line is just starting up, before the parts are stamped out.
The new series combines some features that are already offered on other Rapid granulators, such as double-scissor cutting action, an open-hearted design for fast cleaning and maintenance, and a mineral composite base for stability and noise reduction.
The granulators' modular design accommodates equipment that expels skeletal waste upwards, downwards or sideways. The series also is compact enough to fit in the tight spaces commonly found in thermoforming operations, Rimark said. The design allows Rapid to manufacture and assemble the equipment more quickly, reducing lead times, Hoffman said.
An optional modular sound enclosure limits the sound level to less than 80 dBA for most applications. "Noise reduction is always important in granulating equipment, but, in this application, it takes on a special importance because the equipment is constantly running near where the line operator is likely to be," Rimark said.
ENMA
Enma displayed its new two-in-one shredder/granulator at NPE2018. "Usually the shredder and granulator are separate," said Cotita King, global sales manager for the company.
The TIO1300 is designed primarily for lumps of material and large parts. The machine's rotor is designed to handle both rigid and soft materials.
The granulator features a 30-inch incline housing that makes it easy to feed the material. The feed chamber can be opened quickly for simplified blade exchange and cleaning.
Enma said that the TIO1300 saves the cost of the conveyor that normally would be needed between the shredder and granulator. Featuring integral steel plate welding, it is compact and uses a Siemens PLC.
GETECHA
Getecha introduced a new design for several of its granulator series, allowing them to be quickly reconfigured by the user to optimally process a wide variety of feedstocks. Dubbed "variation granulators," they are especially appropriate for recycling facilities and central granulating applications, President Christopher Koffend said.
The granulators are designed so that users can change the setup of the stationary blades and rotor. For example, the machines can have two stationary blades, which is good for handling voluminous parts. Or, they can have three high-impact blades, a setup that is appropriate for very thick or solid parts. Lastly, a three-blade, high-throughput configuration increases the number of cuts per revolution of the rotor while still providing an aggressive grabbing action by the rotor; this option is suited for voluminous parts, Koffend said.
Additionally, the rotor has three possible configurations. It can operate with no inserts, meaning it is an open rotor for grabbing bottles and large parts. Partial inserts create a semi-closed rotor, suitable for dense, medium-sized parts such as pipes and automotive manifolds. With full inserts, the rotor can be fully closed o it can tackle purgings, thick-walled parts and other items that cannot be safely handled otherwise.
A change to the rotor configuration can take only a couple of hours, Koffend said. "The variation rotor is more costly than a single-configuration granulator, but much less expensive than purchasing two separate granulators for the differing operations," he said.
The variation design is available on Getecha's RS 3800 family of granulators, which have 15-inch- diameter rotors; the RS 450 family, with 18-inch rotors; the RS 6000 family, with 24-inch rotors; and the 32-inch-rotor RS 8000 family of granulators.
REPUBLIC MACHINE
Republic Machine has updated the controls on all of its single-shaft shredders to give users more programming options.
The firm's shredders now include an Allen-Bradley MicroLogix 1400 PLC with a full-function, touch-screen HMI. Users can customize parameters such as ram speed, ram pressure and ram hold time. The control comes loaded with three basic programs that suit most applications, but its open architecture allows users to alter the programs and create three additional programs.
"Most other suppliers offer a few basic programs, and that's it," said product manager Bill Cox. "But we know that controls are crucial to basic performance, and our customers have found that tweaking the programs can really increase throughput and overall efficiency."
Republic's shredder lineup includes the Eagle Modular and Heavy Duty Eagle lines. They are low-speed, high-torque machines with throughputs ranging from 600 to 8,000 pounds per hour.
Allan Gerlat, correspondent
Contact:
Conair Group, Cranberry Township, Pa., 724-584-5500, www.conairgroup.com
Cumberland,
New Berlin, Wis., 262-641-8600,www.acscorporate.com
Enma USA,
Dalton, Ga., 706-529-2386www.enma.fr
Getecha Inc., Kalamazoo, Mich., 269-373-8896, www.getechaus.com
Rapid Granulator Inc.,
Leetsdale, Pa., 24-584-5220,www.rapidgranulator.com
Republic Machine, Louisville, Ky., 502-637-6778, www.republicmachine.com
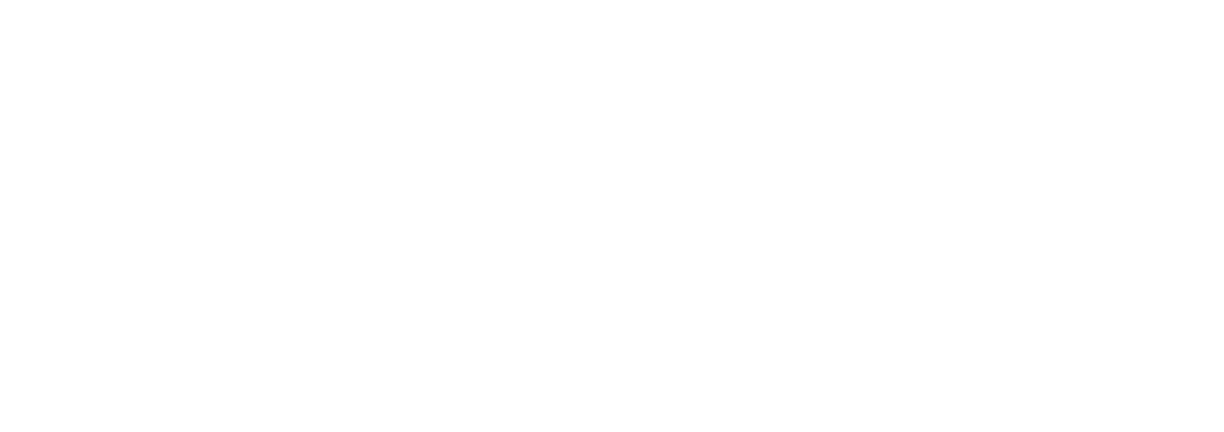