Whether they have to move material in bulk or in small, precise doses, conveying system users browsed a lot of options at NPE2018. Supplier stands touted the flexibility and user-friendliness of a variety of new technologies. The offerings included pumps, filters, receivers, loaders, controllers and systems for specialty-material conveying.
CONAIR
Auxiliary equipment maker Conair loaded its trade-show booth with a bevy of new options for materials handling and conveying. They included updates to the PowerFill combo pump and filter, and the launch of the Medline ML series of loaders and MR series of receivers.
The PowerFill vacuum source combines a pump and filter, along with controls. The latest iteration, the PowerFill 8, has been designed so that operators can manage and support as many as eight vacuum receivers at once, rather than just one, using an easy-to-understand 7-inch touch screen. The vacuum source connects to Conair receivers through plug-and-play communications cables that snap together, avoiding the need for special tools.
Designed with a small footprint and casters, the PowerFill 8 can be easily tilted and moved to any conveying station. And, compared with self-contained loaders featuring motor brushes and central vacuum pumps, it's easier to maintain. The direct-drive, three-phase pump system has no belts to maintain and no need for oil. It comes with a high-capacity dust-collection filter that can be removed and cleaned without tools. As an option, users can install Conair's Cyclone or DC1 dust collectors to increase dust-removal capacity. An optional idle-mode valve enables the pump to run continuously between loading cycles, extending the pump's lifespan. Running continuously is easier on the pump than starting and stopping between cycles.
Also at NPE2018, Conair unveiled its MedLine MR receivers and ML loaders for use with injection molding machines with clamping forces of up to 400 tons. Designed especially for medical molding applications, the loaders and receivers are constructed of electropolished stainless steel around a 4.5-inch tubular body that helps ensure smooth material flow into hoppers. Also, to meet clean-room needs, the loaders and receivers can be bolted onto Conair's MicroWheel dryers or other small-capacity hoppers — a procedure that requires no drilling. Both new series are designed to facilitate easy cleaning, and both are equipped with a switch that automatically signals when the material level in the hopper they feed is low enough that another conveying cycle is needed; conveying cycles also can be initiated by a timer.
Designed to operate as part of a central vacuum-conveying system, the MR receiver series includes two models. The MR-1 has a material-holding capacity of 1 pound. Outfitted with a 5-inch-tall glass extension, the MR-2 holds twice as much. Material enters through a top-mounted vacuum sequencing valve. The receivers offer automatic replenishing via switch and discharge valves that are mounted at the bottom of each unit.
The ML series of loaders operate as stand-alone units, with no need for additional vacuum support.
Like the MR series, the ML loader series include two models: The ML-1 loader can handle as much as 75 pounds of material an hour, while the ML-2 sports a 5-inch-tall glass extension that allows it to handle 100 pounds per hour. Each has a 0.375-horsepower motor and a range of up to 20 feet.
The receivers and loaders can be controlled independently or as part of a central system using Conair's FLX-128 controller.
ACS GROUP
ACS' VacTrac Plus series of wired conveying controllers can control vacuum receivers and pumps, purge valves, remote proportioning valves, blowback from hoppers or pumps, and knife gates. According to Anthony Johnson, a senior manager of material handling for ACS, the controllers are compatible with nearly any relevant product from other suppliers. Users of many products, especially those with 24-volt DC power supplies, will find they can simply plug in the controller and start work.
For users, the new controllers provide the flexibility to customize based on current needs, and the scalability to grow. Using a touch screen, operators can easily add and delete pumps and receiver stations. In all, the controller can handle as many as 12 pumps and 44 receiver stations. To upgrade the VacTrac Plus, the user simply needs to add new I/O modules and software, rather than a controller.
The controllers' 7-inch touch screen provides full visual representation of all controlled pumps and receiving stations, as well as real-time status: idle, disabled, in-demand or alarmed.
The controllers connect to equipment via Ethernet. They offer remote monitoring via computer, tablet or phone through a built-in virtual network computing (VNC) server.
Users can program the controllers to send automatic email alarms when any controlled device reaches specified parameters.
COPERION
Coperion has developed a new pneumatic conveying process that it says cuts the formation of dust and streamers by as much as 98 percent, while lowering energy consumption by as much as a third. The new Fluidlift ecoblue process relies on controlled increases in the relative humidity of the conveying gas in order to slow pellets and significantly reduce friction. To make that possible on both new lines and retrofitted installations, the company provides all necessary engineering and products, including a water-dosing unit, control system and humid-air exchange unit.
The process is especially suited to moving softer pellets, as well as materials that tend to break down into fines and streamers. According to Andrea Trautmann, marketing manager for Coperion GmbH, Weingarten, Germany, it "takes advantage of a reduced friction between the pellets and at the wall of the piping," preventing damage to pellets. That also serves up a number of other benefits, including a reduction in the amount of time users spend cleaning out their pipes.
"This reduced friction causes the pressure loss to decrease and thus the energy consumption of the motor of the blower/compressor," Trautmann said.
Though the final products delivered by the process remain dry, materials that are sensitive to water, such as polyamide, might require further examination to determine their suitability to the technology, she said.
Phillip Britt, correspondent
Contact:
ACS Group, New Berlin, Wis., 262-641-8600, www.acscorporate.com
Conair Group,
Cranberry Township, Pa., 724-584-5500,www.conairgroup.com
Coperion Corp., Sewell, N.J., 201-327-6300, www.coperion.com
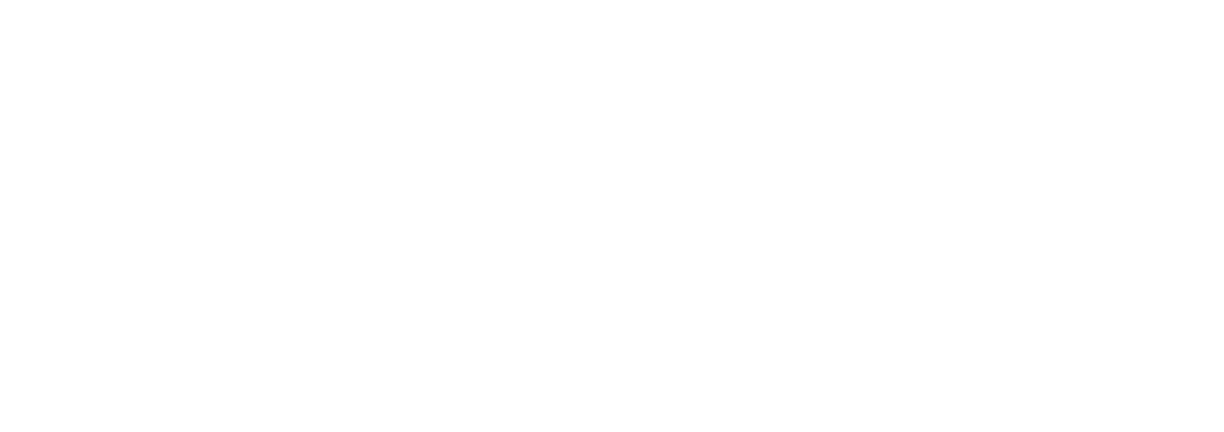