Smart people are working on making the smart factory a reality but the Holy Grail for widespread deployment is a common language that would be spoken between machinery and equipment no matter where it is made.
To achieve the next stage in the evolution of the Internet of Things (IoT) for the plastics industry, industry associations are working together toward the global standardization of the IoT and Industry 4.0. Now, independent, third-party or individual company systems function in place of any global standard interface.
The goal is to reach an agreement on a common interface through which machinery and equipment — no matter where it was made — can communicate in a plastics manufacturing environment. Governing associations in the largest markets for plastics machinery production — North America, Europe and Asia — are working to elevate IoT to the next level. That includes the Plastics Industry Association (PLASTICS) in the U.S. and VDMA in Europe.
Recently, PLASTICS' Equipment Council has developed a subcommittee to work on IoT standards. It is being led by Mark Sankovitch, CEO of Engel North America. This subcommittee was created to do a deep dive into the technical aspects of Industry 4.0 and IoT.
"It all starts with collecting of data and combining information — communication between equipment. The first goal should be to enable this communication," Sankovitch said. "We are just at this stage right now where we have to come together. The most logical place to start is the interface."
The Role of the Interface
Interfaces must be used carefully to avoid variation when it comes to compatibility, said Achim Trübner, team leader of software development, R&D, at blow molding machinery maker Kautex Maschinenbau GmbH, Bonn, Germany. In October, Trübner gave a presentation on the importance of Industry 4.0 at the Society of Plastics Engineers' Annual Blow Molding Conference in Chicago. Avoiding variation in interfaces is accomplished through setting standards. Kautex is working with other Euromap member machinery makers on an interface for connecting blow molding machines to central computers/manufacturing execution systems (MES).
Euromap 77 has been established for the interface between injection molding machines and MES systems for data exchange. Subsections of 77 include 77.1 Injection Molding Machines, Data Exchange Interface for MES-Basic Objects and 77.2, Injection Molding Machines, Data Exchange Interface for MES-Objects for Job Management.
Austrian and German machinery manufacturers, in collaboration with the VDMA, are continuing work on the Euromap 77 platform, officials said. Euromap 77 is based on OPC-UA, an interoperability standard for the secure and reliable exchange of data in applications such as industrial automation, according to the OPC Foundation's website. OPC-UA stands for Open Platform Communications-Unified Architecture.
Beyond data management
Trübner knows that data is the lifeblood of Industry 4.0. Management of that data is key to the future with an end game of conserving resources, increasing production speeds, optimizing production and facilitating more flexible production.
"What is the reason for Industry 4.0?" Trübner asked the audience during the conference. "The business goal is to increase efficiency." The key to increasing efficiency is to have all relevant data about the manufacturing steps available, including having the ability to change parameters for production optimization. Manufacturers also need a flexible machine layout with modular, prouct-specific components that can be set up easily to minimize downtime between product changes. Machinery and equipment must be capable of detecting disturbances or necessary maintenance work. Algorithms can replace or support human decisions.
"Advantages for the machine builder result from the fact that machines can be optimized by means of data services, which results in a competitive advantage and that additional services can be offered for the actual sale of machines," Trübner said. "The relationship with the customer is improved by knowing the conditions at the machine and being able to take specific measures without the need for a sales representative to travel from customer to customer. I think that in the future, services will be the deciding factors that differentiate competitors in the market. These services will always aim to increase efficiency."
Other PLASTICS councils will be joining the Industry 4.0 effort, said Steve Petrakis, VP, industry affairs, Equipment Council for PLASTICS.
"This is very much the wave of the future, and many companies already are in some aspect of compliance with intelligent web-based interaction between machines and smart devices," he said. "Our hopes are that the entire plastics industry globally can unite to make IoT a reality with all equipment easily communicating to make the processor more productive and to keep costs and quality in line for the consumer."
Stan Glover, chairman of PLASTICS' Equipment Council, said that by the end of NPE2018, the association hopes to have all of the primary machinery associations and standards writing bodies discussing Industry 4.0/IoT.
"This is not a hype that will soon be forgotten," Sankovitch said of Industry 4.0 and the IoT. "It's going to be a very dynamic piece of how we manufacture in the future. The efficiency of production, the quality of the products and subsequently the competitiveness of the market will depend on how well a company can use intelligent systems. The vision is to integrate all dimensions of production and available data. This is one of a number of technologies that will put us back to where we need to be in this country."
Angie DeRosa, managing editor
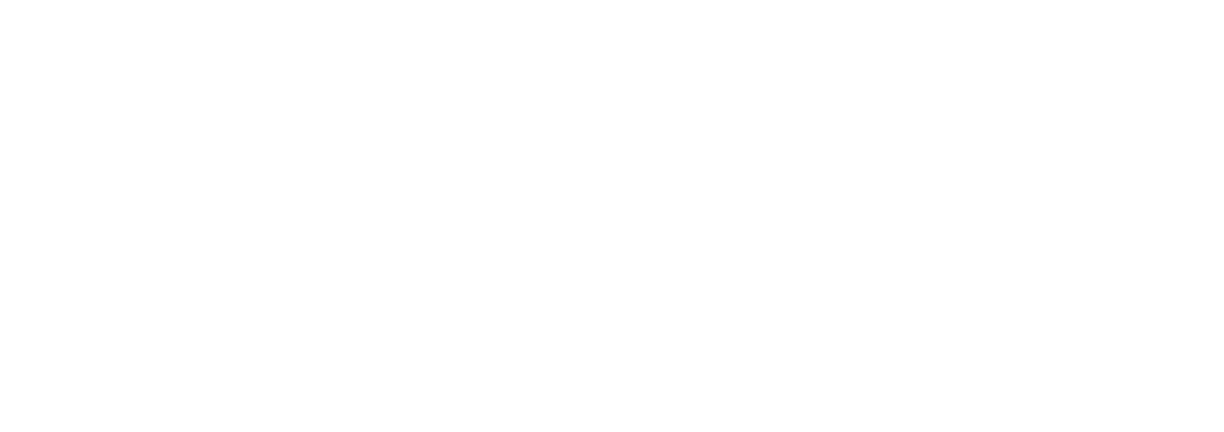