In the past, when processors were searching for process cooling solutions, they didn't have a lot of options. For the most part, the decision was binary — dry cooling or evaporative cooling.
Each has advantages and drawbacks. But in 2017, AEC introduced a hybrid adiabatic cooling system that offers the best of both worlds — and does it while using a fraction of the energy required by packaged air-cooled systems.
The hybrid system uses dry air cooling during the cooler months of the year and evaporative cooling as the weather warms up. AEC said its hybrid cooler can reduce energy costs by as much as 86 percent versus packaged air-cooled systems.
That's because the system monitors environmental conditions at all times and performs in whatever way is most efficient to achieve the desired temperature. When external temperatures are low enough, that is sufficient to expel heat from the system. As temperatures rise, the unit sequentially cycles its fans on and off, using the least energy necessary to reach its target temperature. When ambient air temperatures rise too high for fans alone to cool the fluid, the system begins to use evaporative cooling.
It consumes 95 percent less water than traditional tower-based coolers. AEC said the system can pay for itself with water savings in as little as 2.5 years when compared with traditional tower systems. Compared with packaged air-cooled chillers, the savings are even greater and provide a return on investment in electrical savings in as little as nine months.
Exactly how often the system can use evaporative cooling depends on factors such as temperature and humidity, and savings will vary slightly based on where in the country the facility is located.
How does hybrid adiabatic cooling work?
According to Merriam-Webster, the definition of adiabatic is "occurring without loss or gain of heat" — which makes it an odd term for a machine that's designed to cool process water. After all, if heat is neither lost nor gained, how does it work?
It's all about the transfer of heat. The system doesn't actually eliminate heat, it merely transfers the heat away from the process water to the outside air, then blows it away.
In the dry mode, which is used in cooler weather, heat is carried away from the plastics processing machine by process water that is pumped in a closed loop. The process water passes through a plate-and-frame heat exchanger, where it transfers the heat to cooler glycol fluid circulating in a separate closed loop. The glycol transports the process heat away from the heat exchanger to coils arrayed in a large surface area within the hybrid adiabatic cooler, which resides outside of the factory walls. The heat is transferred from the coils to the colder outside air, and glycol leaves the cooler at a lower temperature to repeat the cycle by traveling back through the heat exchanger. Process water leaves the heat exchanger, having been cooled by transferring its heat to the glycol, to again draw heat away from the plastics processing machine.
When ambient air temperatures rise, the system switches into wet mode. Sprayers direct a fine mist of water around the outside of the adiabatic system. The mist evaporates, cooling the incoming air, which then draws heat from the coils and expels the heat as the system's exhaust fans direct the air out of the cooler.
Regardless of which mode it is in, the adiabatic cooler is a closed-loop system, so the process water can't be contaminated — nor can it contaminate anything outside the system. Glycol is used to keep the outside coils from freezing and protect the cooler if it is shut down during cold temperatures. The glycol loop and process water loop have separate, dedicated pump tanks.
In addition, because it's a closed-loop system, there are no puddles of warm, stagnant water that — if left untreated or insufficiently disinfected — can serve as a breeding ground for the Legionella bacterium, the cause of Legionnaires' disease. If contaminated water is exposed to the atmosphere, it can pose a serious risk to workers.
There are two versions of the AEC system:• A standard-output unit with a 32.5-inch face height that is equipped with 3-horsepower, 35-inch fans. There are six models; the smallest has two fans and the largest has seven. Depending on the model, they offer a nominal heat-rejection capacity of 144,000 Btu per hour to 530,000 Btu per hour.• A high-output, 70-inch version with 5-horsepower, 38-inch fans. Like the standard version, there are six models equipped with two to seven fans, offering a nominal heat-rejection capacity ranging from 277,000 Btu to 962,000 Btu.
The hybrid adiabatic system is freeze-proof and resistant to scale and corrosion, making it easy and inexpensive to maintain. Its housing and framework are made of stainless steel, and its galvanized steel exterior, aluminum fins and copper tubes all are coated with a phenolic epoxy for added corrosion protection.
Michael T. McCue, copy editor
Contact:
AECNew Berlin, Wis., 262-641-8600, www.aecplastics.com
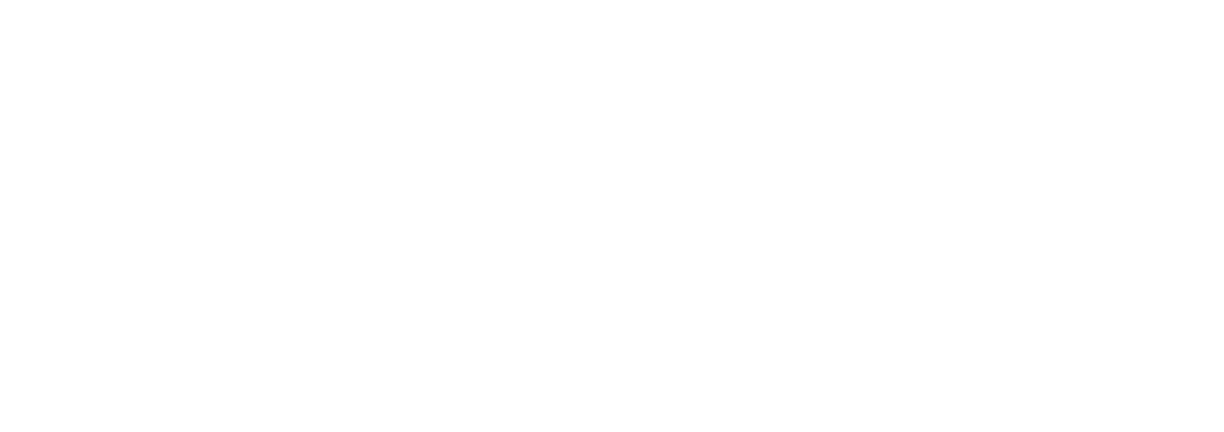