Injection molding machine (IMM) makers are offering a growing array of technologies that reduce or optimize energy consumption. New and updated machines, software and controls give users more ways to match their usage to actual energy needs.
With the adoption of ISO 50001, Süleyman Akseven, an Arburg application engineer, said that manufacturers are increasingly looking for ways to account for and optimize their energy usage. Identifying obvious energy hogs, including peripheral devices, is a first step. "It is obligatory to measure internal energy requirements, identify well-known consumers and continuously seek and implement ways to optimize consumption."
Saving money, qualifying for green incentives and achieving status as an environmentally conscious company are among the driving forces behind improving energy efficiency for machines such as IMMs. In some places, such as Austria, specific laws setting efficiency standards provide motivation for improvements, said Susanne Zinckgraf, manager of public relations for Engel Austria GmbH in Schwertberg.
"Regardless of the energy-efficiency act, our customers keep asking for energy-efficient machines and system solutions," Zinckgraf said. "And this clearly is a worldwide trend."Cincinnati Process Technologies
Automatic energy management is one of the selling points for a new line of IMMs from Asian Plastics (AP) Machinery Co. Ltd., a subsidiary of Chen Hsong Machinery Taiwan Co. Ltd., Taipei, Taiwan.
The new line of hybrids, called Super Master EV2s, "more directly matches the power consumption to the power needs," said Mike Green, GM of Cincinnati Process Technologies (CPT), which distributes the machines. Compared to earlier AP machines that used fixed-displacement or variable-volume systems, the new IMMs employ servomotor pumps that can achieve energy savings of up to 80 percent. Cost savings usually are most noticeable when molding parts that require longer cycles and greater pack-and-hold periods.
The servomotors provide a quick and efficient ramp-up and ramp-down to match energy needs throughout the cycle, Green said.
Priced in the low $40,000 range, the Super Master EV2 line features 13 machines, with clamping forces ranging from 88 tons to about 1,100 tons and shot weights ranging from 4 ounces to 191 ounces. The smallest of the machines, the SM80EV2, so-called because of its clamping forces in metric tons, measures about 14 feet by 4 feet by 6 feet, while the largest, the SM1000EV2, takes up about 39 feet by 8 feet by 8 feet of real estate.
Green cautioned against underestimating the machines just because of their relatively low prices. "I think the gap between a value-priced machine and a premium machine — from a technology standpoint — a lot of them are starting from the same point," he said, adding that CPT is responsible for service of the AP machines.
Outfitted with an established Smart Mold controller and designed for fast clamping movements that reduce clamping time by 70 percent, the Super Master EV2s are suited for general-purpose custom molding. "These machines can fit very well for an automotive application," Green said.
Engel
At recent trade shows, Engel has touted its machines' energy efficiency. At its Drinktec 2017 booth in September in Munich, the company used an e-cap 2440/380 IMM to make 26mm HDPE caps in 2.5-second cycles. The entire cell used less than 0.32 kilowatt per pound.
"Thanks to its all-electric drive technology and low cooling-water requirements, the e-cap injection molding machine is very energy efficient," Zinckgraf explained.She said the arrangement of the integrated cell, which included a new dehumidifier from Blueair Inc., Chicago, represented a first for the IMM maker. The new dehumidifier is particularly miserly in its use of energy.
Zinckgraf stressed the importance of planning the entire injection molding cell with energy consumption in mind; however, Engel provides innovations that curb energy use all by themselves. One recent example is the company's expansion of its proprietary iQ clamp control.
Previously available only on Engel's electric presses, iQ clamp control, which determines the optimum clamping force necessary throughout an injection cycle, now is available as an option for Engel hydraulic duo machines equipped with CC300 controls, Zinckgraf said. The software automatically adjusts machine clamping force shot by shot, so that excessive force never is applied.
In many cases, the process needs less than the maximum clamping force, which is the key to saving energy and reducing mold wear, Zinckgraf said. Exact energy savings vary, according to the application and circumstance.
The savings "are directly related to the reduction of the clamping force," she said. "If the clamping force meets the requirements of the process quite well already, the energy reduction will not be that much. But it's bigger if the process needs less clamping force than the machine is able to provide. We had one test application, for example, where we could reduce the energy consumption of the duo clamping unit by 13 percent."
By restricting clamping force, iQ clamp control prevents the burn marks that might occur because of excessive pressure, as well as the visible burrs that could result from too little tonnage. Engel's duo presses are available in clamping forces of about 400 tons to more than 6,000 tons.
Arburg
Arburg is touting a software upgrade that cuts energy usage. At Fakuma in October in Friedrichshafen, Germany, the company demonstrated the newest module for ALS, its manufacturing execution system. The module, called Energy Visualisation, documented and displayed data from an automated electric Allrounder 370 E Golden Electric, as well as the robotic system and peripheral equipment supporting it.
Axel Kinting, team manager for host processing engineering for Arburg, said the module allows users to better compare energy usage across cells, as well as break down energy consumption by each specific piece of machinery. "With the new module, the ALS host computer is able to visualize and document the data of the measured energy combined with the orders," Kitting said. "It ascribes the amount of energy consumed belonging to the order. For that, you can say how [much] energy was needed e.g., for a certain order/batch of Product A or B."
According to Arburg, with Energy Visualisation, energy-consumption data from its IMMs, as well as auxiliary equipment, can be integrated into ALS reports. Information regarding energy, power, current and voltage data can be recorded for future analysis using the software.
Karen Hanna, copy editor
For more information
Arburg Inc.,Rocky Hill, Conn., 860-667-6500, www.arburg.us
Cincinnati Process Technologies,Cincinnati, 513-619-7415, www.cinprotech.com
Engel Machinery Inc.,York, Pa., 717-764-6818, www.engelglobal.com
Karen Hanna | Senior Staff Reporter
Senior Staff Reporter Karen Hanna covers injection molding, molds and tooling, processors, workforce and other topics, and writes features including In Other Words and Problem Solved for Plastics Machinery & Manufacturing, Plastics Recycling and The Journal of Blow Molding. She has more than 15 years of experience in daily and magazine journalism.
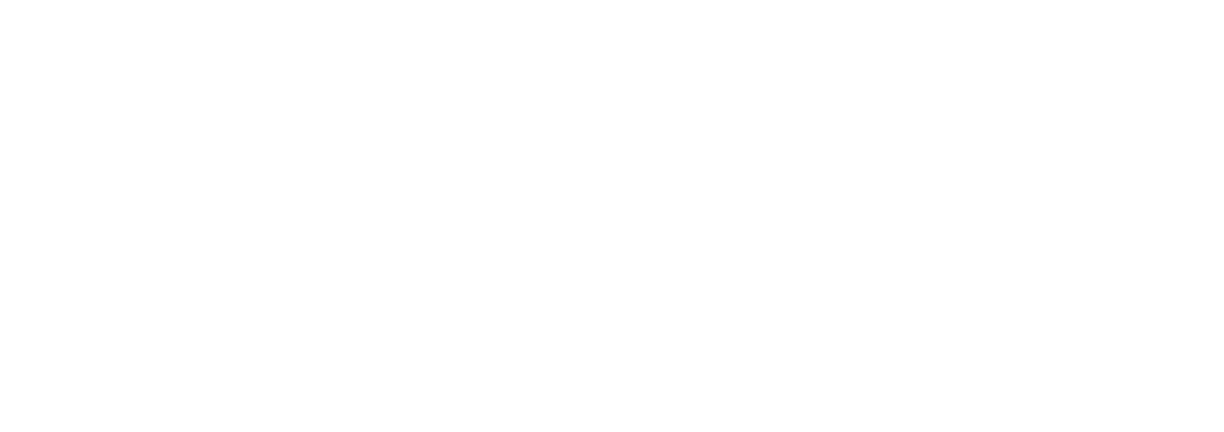