Uniform wall thickness is essential to ensure that containers and bottles don't leak. But measuring thickness at only a single point does little to ensure the integrity of the entire unit. One company is addressing the need for assessing wall thickness at multiple inspection points with a system that can do so automatically without human intervention.
FocalSpec's Online Wall Thickness Measurement System has sensors to measure the thickness of each wall of a container or bottle. It provides immediate feedback for blow molding machine operators so they can quickly adjust and optimize settings during daily production, said Juha Saily, FocalSpec sales manager.
A photo eye trigger installed immediately before the sensors alerts the system that a container is approaching the measurement station. A trigger and encoder track the container's position and continuously sense the speed of the conveyor.
The sensors are arranged in a stack, giving the system a small footprint. Each sensor includes an integrated light transmitter and receiver, which enables measurement of individual walls, rather than combining the measurements of two walls in a single result. The measurement of each wall significantly improves process control capabilities.
"If a bottle manufacturer doesn't have complete information about wall thickness, then he could have problems with recalls," Saily said. Wall thickness measurements are becoming more important as the industry goes to thinner bottles to save on raw materials, he said.
The system is mounted on the side of a conveyor on a stand that includes stack lights, brackets for a PC/monitor and a sensor-interface module, which allows up to four sensors to transmit thickness data to the PC.
The main screen shows data collected from each container as it's measured and analyzed in real time.
The user can set the multiple sensors at different heights, with each one scanning every container at a rate of up to 120,000 bottles per hour, resulting in up to hundreds of readings from each measurement area, depending on the speed of the conveyor and the thickness of the container.
The system is designed for containers with thicknesses of 0.05mm to 4mm.
Users can set the system to automatically alert operators via a stack light and to reject containers that don't meet specified thickness limits. This ensures that only bottles and containers meeting the desired specs are shipped out for filling while also reducing the need for time-consuming, manual quality-control procedures.
Phillip Britt, correspondent
Contact:
FocalSpec Inc.Cumming, Ga., 770-713-0837, www.focalspec.com
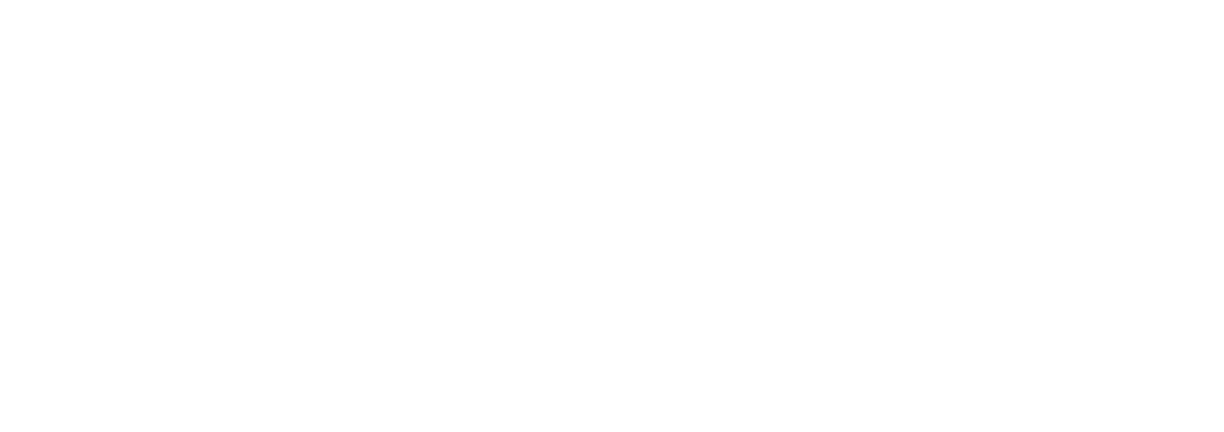