At Arch Plastics Packaging, blow molding is held in high esteem. The company recently added injection blow molding (IBM) to its portfolio of capabilities and now has three blow molding processes under one roof at its headquarters in Chattanooga, Tenn.
Every technology that is pursued by the company is driven by customers' needs, said facility manager Shital Rali during an interview and tour by Plastic Machinery Magazine on Aug. 30.
"Everything is around what the customer wants," Rali said. "We tell our customers and potential customers that our capabilities are far beyond our limitations. What you see, do not think this is the only thing we can do. We have come, in just 11 years, from having two blow molding machines to today having 14. This is going to be a unique blow molding facility where in such a small footprint we will have all three processes, all three technologies, under one roof: extrusion blow molding (EBM); injection stretch blow (ISBM); and injection blow molding. That, in itself, speaks about the resources that we have, the capabilities that we have, and the comfort and confidence we have to deal with any technology."
Arch makes bottles within 24,000 square feet of manufacturing space — part of a 82,000-square-foot facility that also includes warehousing. The bottles Arch makes have numerous uses; the company serves the pharmaceutical, nutraceutical, beverage and food, personal care, cosmetic and household-products markets. Officials prefer to keep confidential the names of brands and clients, but the bottles carry major brand names and can be found on retail shelves.
When it comes to innovations and adding technology to meet those requirements, the operations team is trusted to make decisions for an ownership group that essentially is hands-off. Rali leads the day-to-day team.
Arch has a pre-approved credit line through banks, and its investors also have financial resources — this means that projects can be implemented in record time.
"The number of machines does not bother us. It's the business. The customers give us the business," President and CEO Charles Amin said matter-of-factly. "You're not going to buy the machine and then look for the business."
For example, the company purchased three blow molding machines at once in what was a $5 million investment for a specific piece of business. At that time, Arch had $7.5 million in total assets. That investment illustrates the company's willingness to invest in innovation if the business demands it, Rali said. The company does not prefer one brand of blow molding equipment over the other; officials select the brand and model that is best suited for a project.
Rali said no fixed percentage of capital expenditures is allocated to innovation in a given year. "Innovations are need-based. When there is a need, when we see the value in that new technology or new manner of doing the job or introducing a new capability, that is where we get the support," he said. "Our team is young and dynamic, and they are tuned [in] to learn the new technology and new processes. We always ask the customer, 'What do you need? Don't look at what we have. We will have what you want.' That is basically the centric objective of this company from Day One."
The company's EBM machines are Bekum H-155s that can produce 50-milliliter to 10-liter bottles, narrow/calibrated neck bottles, wide-mouth jars and packer bottles.
With its 10 Nissei ISBM machines, the company can produce bottles ranging in size from 1 ounce to 15 liters, working with tool sets having one to 20 cavities. The machines are capable of loading 0.1 percent to 8 percent let-down-ratio (LDR) colorants. "Depending on the end-use applications, certain products need very low dosage with minute solid particles and, in some cases, a higher dosage of colorant, depending on the pigment in the colorant," said Rama Etekallapalli, the engineer who is in charge of plant quality.
With an IBM machine provided by Jomar, the company produces 5-milliliter to 100-milliliter tablet bottles, mascara tubes, jars, oval bottles and roll-on deodorant bottles.
NEED FOR INNOVATION IS CONSTANT
If necessity is the mother of invention, necessity and the desire for quality might be the bedrocks for innovation within Arch. In 2009, the company created a core group known as Smart Productivity Improvement; it has five permanent members. That team's objective is simply to brainstorm at least twice per month.
"The team doesn't meet with a particular agenda in mind," Rali said. "The majority of the time, we spend in doing brainstorming, asking, 'What can be done better?' More than 100 changes and improvements that we have done in the last eight years have evolved in these meetings. The changes can be in any areas — safety for employees, productivity improvements, resource management, developing a new technology, etc. These ideas are nourished during those meetings."
Officials here have come to terms with the fact that the solution they are seeking might not be available from an industry supplier. Of the innovations they have adopted over 11 years, many have been developed in-house, such as an in-line system to measure ultraviolet-light resistance in bottles.
Separately, on the day of the tour, officials highlighted an innovation in development within Arch's quality-assurance lab. In a bottle-making operation, workers need to be able to measure overflow capacity. But it is time-consuming and inefficient to have one employee test one bottle at a time. Arch's goal is to develop equipment that can test multiple bottles of different sizes all at once.
Also on their project list is finding a way to integrate robotic packaging with a vision inspection system. Arch is working with robotics suppliers to find a way to use a collaborative robot that can work alongside people. This would allow bottles to be automatically inspected before being packed.
"There is no system today available with the automatic robotic packaging with the vision system integrated to that," said Chaitu Gogula, who is in charge of production and process. "So that is what we are trying to develop right now."
Innovations abound on the plant floor. They include a unique design for head tooling that was developed for a particularly challenging EBM process that results in consistent quality and precise dimensions.
In addition, Arch installed magnets in the hopper throats of each of the blow molding machines, which is a part of risk mitigation for the company to ensure that no foreign material enters the machine barrel.
To help remove hot-runner cores from ISBM machines, the company has adopted specialty jigs. The task can be very difficult otherwise.
Arch has developed unit cavity sample tooling, used to make samples for potential long-term projects, with ease of interchangeability for its EBM process. Officials said this gives them an advantage over their competition for quick turnaround. In addition, they can blow prototypes for any newer projects.
Officials were careful to point out that investments have non-tangible benefits. For example, the company installed a vision system for measuring the diameter of bottles.
"It gives you the repetitive, more accurate and quicker measurements, but you cannot quantify the return of that investment in terms of dollars," Rali said.
"But we thought that if one bottle measurement takes two minutes for a quality inspector using a caliper, if this is doing that in 20 seconds, then one minute and 40 seconds of that quality person's time can be used on the floor to check more bottles as they comes out of the machines," he said. "We can probably detect the defect earlier and that is how we can be a little more confident that we are not having any defective bottles going into the finished case. Plus if there is a defect, if we were catching that defect after two hours, now because we were doing checks more often we will probably find that defect in one hour. That is the indirect advantage of having that technology."
MOLD MAINTENANCE AS TOP PRIORITY
Maintenance is a top priority for Arch. The company has what it calls a unique way of preserving and handling tooling. At the time of the tour, Arch had 38 total molds, 17 stock and 21 custom.
"Every mold that we get, as soon as we get it, the first thing our mold expert in charge will do is prepare a wooden box for it," Rali said. That box will have the room to accommodate all the components for the mold. The box is fabricated with a clear plastic cover so that the contents are easily visible. It then is tagged to communicate what stage the mold is in.
"Every tooling has its own location on the rack where it needs to go," Rali said. "The mold, once it is taken out of the machine, will invariably go onto the mold table. It will not be kept on the shelf. Mold shop technicians will do the preventive maintenance on that mold, clean the mold thoroughly and apply the protective spray onto the mold, and put it into its box to be put on the shelf. This is a very unique mold-maintenance and mold-preservation program we have had since Day One."
For the 13 molds used to process HDPE in EBM, officials also use water-flow testers when preventive maintenance is performed to ensure that there is no water leakage. Arch has seven stock and six custom molds for that process.
SUSTAINABILiTY: A WAY OF DOING BUSINESS
Sustainability is a key theme for the company. Its facility emits zero pollution and the cooling water is recycled. Additionally, the company now has 100 percent postconsumer resin (PCR) successfully tested and qualified for use in ISBM applications
Companies that market shampoos, conditioners and lotions are pushing the sustainability efforts, Gogula said. "We are able to process and produce bottles up to 100 percent PCR," he said. "If a customer says they want 20 percent, or another percentage, we have the infrastructure and ability to blend to that customer's specifications."
Sustainability is being pushed through to customers. In another example, Arch is working on getting some customers to convert from corrugated cardboard packaging to recyclable and reusable plastic packaging.
One of Arch's major customers currently uses corrugated cardboard for its packaging. Due to how much product is shipped annually, a team manages 350,000 pounds of corrugated packaging at the customer's facility. Arch is working to change that.
"We have come up with a packaging patent that will use plastic tubes to layer-pack the bottles to keep the bottles in a particular manner," Rali said. The tubes are designed to stack on top of each other, and all these tubes will be on a plastic pallet. The pallet can then be reused. In addition to being wasteful, corrugated cardboard is a source of potential contamination. Fibers from the cardboard can get into filling lines or back into the product.
"If we are successful implementing this, they are going to prevent 350,000 pounds of corrugated packaging being used in their facility every year," Rali said.
FUTURE EXPANSION
Arch has its sights on expansion, with plans to build a facility on a 3-acre parcel across the street. Separately, the company also has 12 acres of land in Huntsville, Ala., targeted for a future addition.
Rali points out that future investments could include other processes, perhaps injection molding.
"We are kind of technology independent," he said. "If you get an opportunity, if you get that piece of business, then you will probably next year see an injection molding machine."
Angie DeRosa, managing editor
Contact:
Arch Plastics Packaging,Chattanooga, Tenn., 423-553-7751, www.archplasticsllc.com
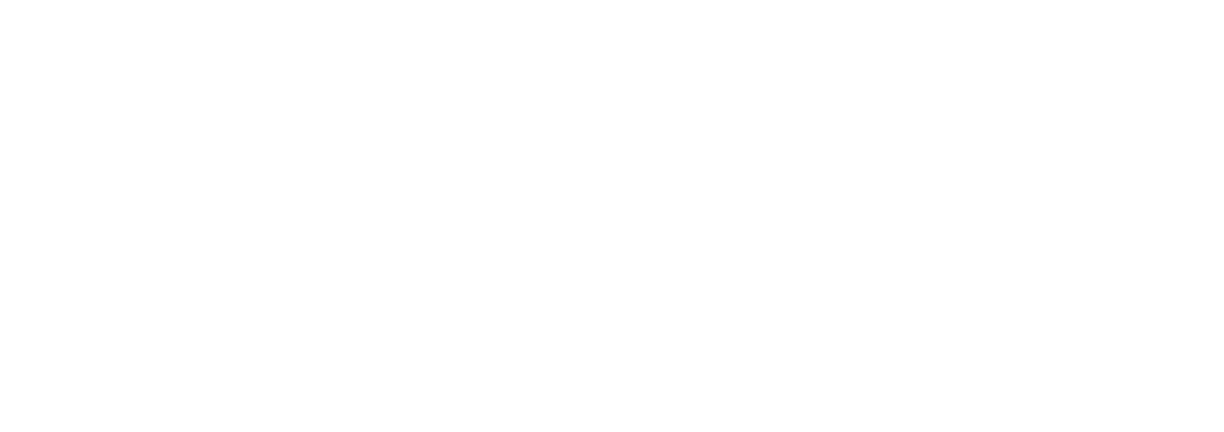