iml Solutions' monitoring system bolsters predictive maintenance
Alicante, Spain-based iml Solutions, a developer and supplier of turnkey in-mold labeling (IML) systems for injection molding, has launched a new monitoring system that helps users provide optimal mold care, including preventive maintenance.
The iMould system, launched late last year, centralizes data relating to the mold, IML system and injection process to anticipate failures and minimize unexpected downtime, said Juan Francisco Carot Martin, area sales manager in North America for iml Solutions.
The system uses sensors in the mold to monitor and measure operating conditions. It can capture data relating to in-cavity pressure and temperature, cooling system flow and temperature, vibrations and cycles. In addition, it provides complete control of the hot runner and monitors the thermocouples, said Carot, who spoke in April at the Molding 2017 conference in Charlotte, N.C.
The iMould system applies an algorithm to the data it captures and uses comparisons with pre-set parameters to anticipate failures. It displays set parameters and actual and historical data for each monitored parameter. Molders can use the data to schedule downtime as part of their normal operations.
For example, the screen used to display data about mold cooling provides real-time information about individual cooling channels, inlet chiller temperature and the temperature and flow of the cooling media. "We have developed the technology to monitor the behavior of every parameter of the mold and can therefore foresee any failure and generate alarm for it," Carot said. "This is a predictive maintenance tool that can be used to ensure your system will always be working at its highest capacity."
The iMould system offers Industry 4.0 connectivity, allowing users to monitor all components in a manufacturing cell remotely and in real time. The company tailors the system to the needs of the molder, based on factors such as the label-handling procedures, polymers and automation that are used. For hands-free operations and access to remote technical assistance, users can add smart glasses. The system also can integrate augmented reality to show the inner parts of the mold.
In addition to iMould, the company designs custom-made, fully adaptable three-, four- and six-axis robots with side-entry, top-entry and hybrid designs. All systems can be designed to decorate multiple parts, and can integrate versatile labeling magazine systems.
The company also designs and manufactures the end-of-arm tooling and supporting frame for the robot, as well as sensors that allow different labels to be handled and placed without mislabeling. It also offers its own product stacker, optical inspection and carton packaging systems.
Last year, iml Solutions opened a 4,000-square-foot complex at its headquarters. IML Innovation Park was created to develop, demonstrate and test IML systems and related technology.
Mikell Knights, senior staff reporter
Contact:
iml Solutions,Charlotte, N.C., 904-609-9595, www.imlsolutions.com
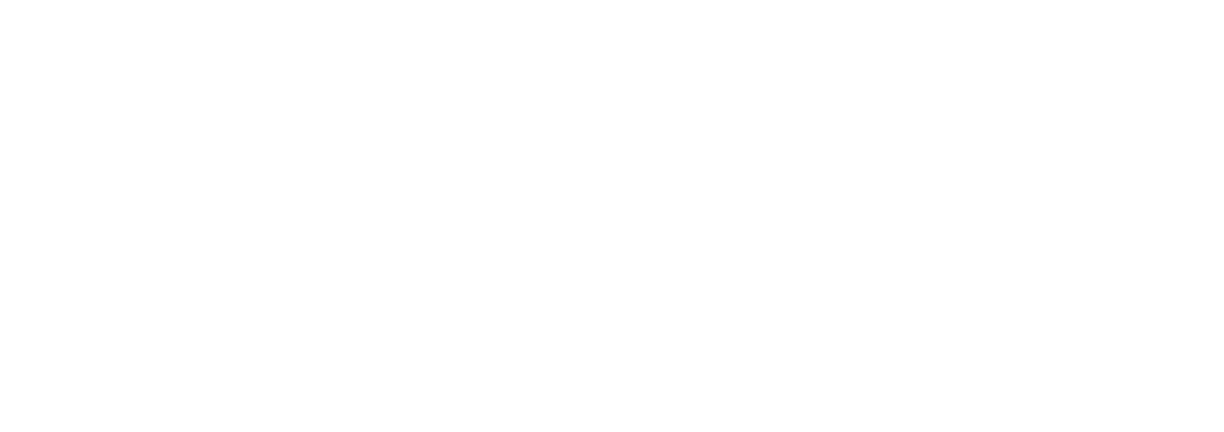