An Engel machine that's been modified to handle the higher temperatures required for metal forming is gaining traction. Now in its third generation, the modified Engel machine is the result of a partnership between Liquidmetal Technologies and the plastics processing machinery maker.
Those familiar with the process say that plastics press operators have the knowledge base to take on metals.
"The control technology is the same," said Paul Hauck, executive VP for Liquidmetal Technologies. "If you are a polymer processor and know how to run the e-motion machine, you can walk up and successfully produce a liquid metal part."
Using amorphous metal alloys composed of zirconium, copper, nickel, calcium and titanium, the one-step process produces finished parts that require no debinding, annealing, sintering, coating or polishing.
Molders are required to purchase a license from Liquidmetal for the process; at least one Italian facility with the license also performs injection molding with plastics.
Plastics machinerygets revamped for metal
Recast to handle very high temperatures, the all-electric e-motion model has 110 tons of clamping force.
Converting the Engel machine to process amorphous metals involved replacing its reciprocating screw and barrel with a Liquidmetal plunger-style injection and heat-induction system. Induction coils placed around the heat zone of the injection unit heat an ingot of material to 1,832 degrees Fahrenheit. An automated, machine-controlled feeder orients and delivers one ingot at a time to the machine.
To seal the system, O-rings must be placed between all the mold plates. "We draw a vacuum so that we can evacuate oxygen before we melt and inject the metal, to protect the alloy from oxidation," Hauck said. The ingot is fed through the fixed platen of the injection unit into the heating zone of the barrel. Once heated, the plunger pushes the molten metal under pressure directly into the cavity of the manifold of the tool. The system is designed without a hot runner, he said.
Currently, the modified Engel e-motion press can deliver a maximum shot size of 100 grams. The molding cycle takes 2 to 3 minutes, with approximately 80 percent of the cycle devoted to heating the ingot, about 15 percent dedicated to drawing the vacuum and the remaining amount used for injection and cooling. A complete molding cell is fitted with an Engel part-takeout robot and a conveyor system with overhead fans to cool the demolded parts.
All equipment in the molding cell is controlled through Engel's CC300 machine control, Hauck said. Engel developed control screens that provide the user with an indication of the heat cycle.
The entire cell would be familiar to operators at plastics injection molding plants. "A user sees the same outputs for the injection portion of the cycle as you would molding a plastic part," Hauck said.
PROCESS SHOWS ADVANTAGES OVER TRADITIONAL APPROACHES
According to Hauck, the process can be cheaper than making parts with a CNC machine, and it can compete — depending on part complexity, size and other factors — with more traditional metal injection molding or powder injection molding for making automotive, dental, electronics, medical and recreational equipment parts.
Unlike powder injection molding, which is a multistep process, the Liquidmetal process produces net-shape parts in a single step.
According to the company, the alloys solidify in a dense, noncrystalline atomic structure, and compare favorably in terms of strength, hardness and elasticity to powdered metals. Conventional metal alloys crystallize into geometric structures when they cool.
"The boundaries between the crystalline structures are weak regions. The crystalline metal part can permanently deform or break along those boundaries when under stress. Amorphous metals do not have grain boundaries that can create weak regions or break points," Hauck said.
By comparison, powder injection molding uses a feedstock of crystalline metal powder and a binder material that yields an intermediate part when molded. The molder must then remove the binder material from the intermediate part — done in a thermal or solvent debinding step, then, the part is placed into a sintering oven to achieve final density.
The Liquidmetal process can produce metal parts with complex shapes in less time and with less scrap than CNC machining, Hauck said. The gate and runner from a demolded metal part can be reused.
Tooling for use with amorphous metals has a mold life of 100,000 shots. Powder injection molding tools in comparison can be used for 1 million molding cycles, Hauck said.
Mikell Knights, senior staff reporter
For more information
Liquidmetal Technologies Inc.,
Rancho Santa Margarita, Calif., 949-635-2190, www.liquidmetal.com
Engel Machinery Inc.,
York, Pa., 717-764-6818, www.engelglobal.com
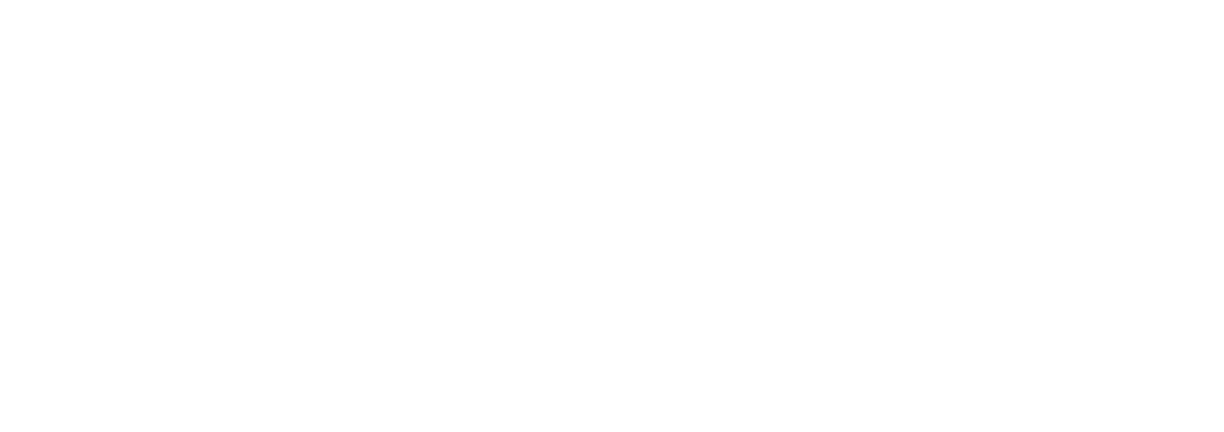