Davis-Standard recently finished merging its manufacturing facilities with those of the former Gloucester Engineering Co., Gloucester, Mass., which is expanding the company's offering of products, company officials said.
Davis-Standard bought Gloucester Engineering, also known as GEC, in September 2015 and completed the move April 1, said Carl Johnson, VP of Davis-Standard's blown film systems group.
Davis-Standard is in the process of adding more than 30 jobs to its Pawcatuck, Conn., headquarters, which already employed more than 400 people.
A 15,000-foot addition houses the manufacturing and machining of advanced multilayer film dies, and enabled Davis-Standard to move all manufacturing of blown film equipment for its Gloucester Engineering product line to the Davis-Standard headquarters.
"To do that, we built a brand-new die center where we make dies, up to 11 layers, as well as repair them," Johnson said. "It is totally dedicated to the manufacture and the upkeep of blown film dies. That was a big move for the company. That was a significant investment."
This isn't the first merger for Davis-Standard. The company previously bought Egan Machinery in 1994.
"Between the three companies, there is quite a bit of technology, and everybody had a different way of approaching the market, so it really has broadened our product portfolio," Johnson said.
Among the most significant improvements Davis-Standard has recently introduced are single- screw extruders with improved output rates.
The improved performance is due in large part to the introduction last year of the DSB3 feed screw, which is for use with LLDPE and LDPE used in blown film extrusion."We do an awful lot of work down in the lab at Pawcatuck," Johnson said. "They have done an incredible amount of work on single-screw extruder feed screws. They've really focused on output and energy. It sounds almost like a miracle machine. We are getting more rate with lower energy utilization at lower melt temperatures."
The output rates on single-screw extruders for blown film have increased by 20 to 25 percent, and the melt temperature has been reduced by 20 to 30 degrees Fahrenheit, resulting in a significant energy savings, Johnson said.
"You want to get as many pounds per hour of good quality melt out of the smallest extruder possible because it takes up the least amount of space, and it's the most energy efficient."
The company also recently introduced a new spiral blown film die design for temperature-sensitive materials, including ethylene vinyl alcohol and nylon. The company received a patent in 2015. The dies reduce the frequency of cleanings.
"We've been able to increase the uptime of processors between die cleanings significantly," Johnson said. "I've seen some dies go longer than a year before they have had to be cleaned, which is pretty darn good in the world of high-barrier resins. With a lot of work in computer-aided flow design, we came up with a different way of designing and cutting this spiral."
It can take as long as a week to clean a blown film die, so operators are anxious to extend their run times.
Another recent product addition involves a retrofit available to the owners of center winders previously sold by Gloucester Engineering.
"On the high-end center winders offered by the former GEC, there is now a retrofit available to add surface-drive capability," Johnson said. "Adding the surface drive makes the winder far more versatile as it goes from one mode of winding to three in that it can now run in center, surface or center/surface."
Davis-Standard has operated in southeastern Connecticut since 1848.
Bruce Geiselman, senior staff reporter
Contact:
Davis-Standard LLC,
Pawcatuck, Conn., 860-599-1010, www.davis-standard.com
Bruce Geiselman
Senior Staff Reporter Bruce Geiselman covers extrusion, blow molding, additive manufacturing, automation and end markets including automotive and packaging. He also writes features, including In Other Words and Problem Solved, for Plastics Machinery & Manufacturing, Plastics Recycling and The Journal of Blow Molding. He has extensive experience in daily and magazine journalism.
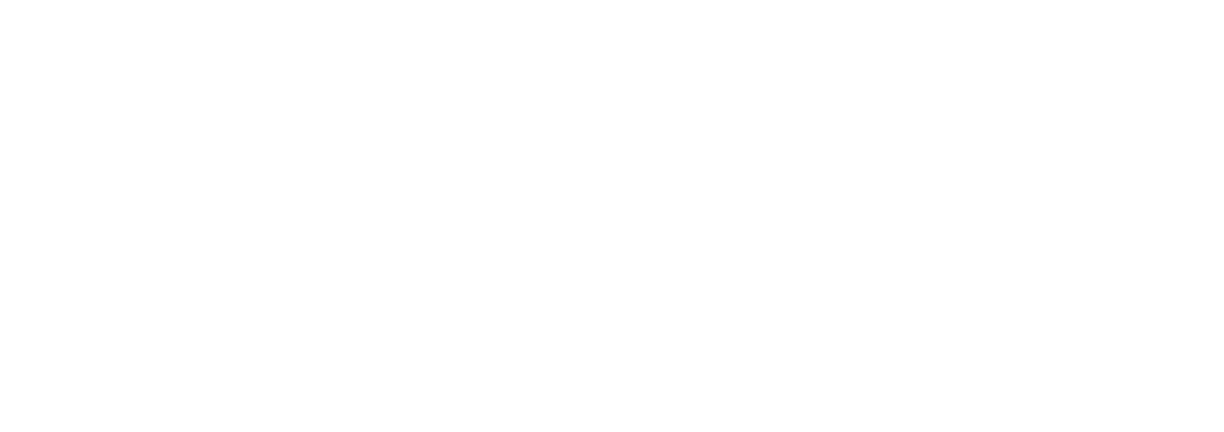