Compression molding has enjoyed strong and steady growth in recent years, and several equipment manufacturers that serve the sector have been improving their offerings to meet the growing demand.
Traditionally, the greatest interest for compression molding has come from aerospace and other specialized fields like R&D, but growth in composites material development has helped to drive demand from more consumer-focused sectors as well.
Wabash MPI and Carver
Demand for compression molding presses has been strong over the past few years, said Dave Singer, marketing manager for equipment manufacturers Wabash MPI and Carver.
Companies are adding capacity as the broader market continues to expand because many products that used to be made from steel, aluminum or some other alloy are now made from lighter, stronger composite materials. The growth in composites material development has, in turn, driven expansion in compression molding applications.
"The composite market as a whole continues to grow, although the stronger U.S. dollar and geopolitical uncertainty can make international projects a bit more daunting," Singer said.
He expects demand for compression equipment to continue its recent growth trend. "The new material development will continue to drive worldwide growth," he said. "The aerospace, recreational and automotive industry sectors are definitely growth areas. "With Wabash MPI being a custom builder, we see a continued increase in projects requiring automation to handle the parts in and out of the clamp. In addition, the need for faster and accurate control of heating, cooling and force cycles is becoming more important, especially within the composites molding industry."
Wabash has teamed up with a specialized process control and tooling company to integrate its custom induction heating and cooling system into Wabash's press. "We provided the proper control interface and mounting configuration to accept their tooling," Singer said, adding that the technology dramatically cuts the overall cycle time to a fraction of a traditional, electrically heated/water-cooled process.
"Many thermoplastic composite materials need to be compression molded to achieve the proper tolerances," Singer said. "Heating and cooling cycle times become critical, especially for high-volume products."
Wabash has worked with, and recently supplied equipment to, several universities, consortiums and R&D organizations that are developing the next generation of both thermoset and thermoplastic composite materials and applications.
Recently, it provided a custom composite molding press to a university program for development. The press was designed with 42-inch-by-42-inch heated and cooled multizone platens capable of heating up to 1,000 degrees Fahrenheit. It has a maximum clamping force of 250 tons.
Features include the ability to ramp up the temperature and force parameters. Also, the press included closed-loop control of the velocity and position of the moving bolster. All parameters are centrally controlled through the press PLC and accessed through the HMI. Additionally, the press was equipped with 12 mold thermocouple inputs to monitor and control the cycle from the mold temperature. Data are graphed on the HMI in real-time and can also be downloaded.
"As process and technology changes arise, we also have the ability to access the press control system remotely, allowing us to continually assist [customers] with future development," Singer said. "It is exciting to be involved with these ventures and see the growth potential within the market."
Surface Generation
"Regardless of whether you're talking about 3-D printing, casting, injection molding or compression molding, achieving a net-shape product in one hit is essentially the panacea of manufacturing," said Ben Halford, CEO of Surface Generation Ltd., Oakham, England. "So the challenge becomes, how efficient can we make that process?"
Compression molding can't quite solve all of manufacturing's problems, but it can get pretty close to providing near-net-shape, Halford said. Injection molding performs better when it comes to producing a virtually finished product in a single hit, but compression molding enables the use of a much broader range of materials and a variety of reinforcements.
With injection molding, reinforcement materials usually are limited to fibers that are no more than 0.5-inch long, and by the time they're in the part, they're probably broken and sheared to only a half or a third of their original size.
"Compression molding is an entirely different animal," Halford said. "You can use fibers that run the entire length of the part."Because both techniques have their advantages and disadvantages, the trend over the last two years or so is to hybridize injection and compression molding.
"It's the perfect solution for someone who wants, for example, continuous carbon fiber or glass fiber in their parts," Halford said. "Then they can compression mold a blank so the reinforcement runs throughout the part, and then injection mold over the top to get the net shape as close as possible. Creating a hybrid of the two saves time and money because you're changing a two-step process into something more like a 1.5-step process."
That significantly mitigates one of the biggest historical flaws with compression molding: the inability to do high-volume production. To streamline compression molding so it meets customer needs for greater throughput, Surface Generation moved the preheating and cooling processes offline to maximize the time the press can be in use.
That led to the development of the Multiplexing system, featuring Surface Generation's proprietary Production to Functional Specifications (PtFS) technology. PtFS provides multizonal temperature control by applying streams of hot or cold air to the back of the mold.
Mold faces are loaded into pressure-containment cassettes and passed through a series of stations for loading, preheating, molding, cooling and demolding, which control the temperature and pressure applied to the material to protect part quality until parts are sufficiently cooled to be removed from the mold.
Users that employ multiple cassettes and multiple stations for preheating and cooling can minimize the amount of time the press sits there, waiting for temperatures to change. Although upfront capital costs might be doubled due to the need for additional heating and cooling equipment, users can effectively quadruple their throughput, Halford said.
The ultimate goal is to maximize yields — even if that comes at the expense of cycle times, if necessary. Shorter cycle times might make more products in a shorter period of time, but the returns diminish rapidly if they also result in a 15 percent scrap rate.
"Even buyers are beginning to realize that the name of the game is achieving the lowest cost per finished component," Halford said.
The Sacmi Group
Compression molding equipment from Sacmi Group, Imola, Italy, is largely focused on the production of plastic caps and plastic containers. "It's a process of extrusion and compression, which is different from the compression molding of thermoset plastics," said Iacopo Bianconcini, marketing manager for the company's packaging division.
In thermoset compression molding, the material is placed in granules into an open mold, the mold closes and is heated to cure the material. With thermoplastic materials, like those used for bottle and caps, both in injection and Sacmi's compression processes, the material is melted in an extrusion process, then the molten plastic is placed in a mold, which is cold. "It's a very fast process," Bianconcini said.
Although Sacmi has seen an increase in sales of its compression molding machinery, the real story is the jump it's seen in installed capacity. "If we measure sales by installed capacity — how many caps and containers are introduced into the market by our new machines — then the number is significantly higher. Reasons include the machinery's greater efficiency and decreased cycle times, meaning higher output of the new compression molding for caps (CCM) and compression blow forming for containers (CBF) machines."
Bianconcini said that the macro factors for those trends, particularly in compression molding for caps, include not only growth in global populations, but also increasing income for the middle-class populations of emerging countries. Warmer weather also plays a part, since rising temperatures lead to greater fluid consumption, with increases in single-serving and on-the-go formats, and a corresponding need for more bottles and caps.
Sacmi has made several upgrades to its compression molding technologies, particularly in the areas of energy efficiency and reduced cycle times.
Developments include:
* H.E.R.E. Evolving with the changes brought about by Industry 4.0, Sacmi developed a scalable software platform known as H.E.R.E., which stands for Human Expertise for Reactive Engineering. H.E.R.E.'s range of software tools supports customers in production process management by monitoring and communicating with machinery inside the plant.
* COOL+. This is the name for Sacmi's in-mold liquid coolant circulation system, which ensures all parts in contact with the plastic are cooled (both the inner and outer punches) to reduce cooling times.
Recently, Sacmi supplied its 30th CCM machine to Alucaps, a cap producer with plants across the Americas. But the company is also seeing demand from the plastic container segments in both Asia and the Americas, mainly the pharmaceutical and dairy sectors, specifically liquid single-serving yogurt containers.
Finally, Sacmi is increasingly focused on its environmental impact, particularly by reducing the energy consumption of its equipment and lightweighting caps, preforms and containers. The company has also made changes to some of its equipment to mold those products from bio-based materials.
Beckwood
Beckwood has also seen significant growth in compression molding projects over the last few years. The demand traditionally came from the aerospace industry, but the company is starting to see increased activity in the automotive, medical, energy and R&D sectors as well.
"The compression molding industry as a whole is certainly on the rise, and we expect this trend to continue as lightweighting initiatives increase," said Josh Dixon, director of sales and marketing for Beckwood.
One trend he's noticed, from a machinery standpoint, is the requirement for very precise process control.
"Compression molding customers are trying to remove as many unknown variables as possible in order to streamline their operations and provide consistency from cycle to cycle," he said. "Whether that means controlling the heat to the platens, controlling ram parallelism, or controlling ram pressure/force, the increased need for higher-performing systems is noticeable. By purchasing a machine that is focused on consistency and process control, customers feel confident removing 'machine repeatability' from their list of unknown variables," Dixon said.
Two of Beckwood's top areas for development are automation and mold heating. Automation has been, and will continue to be, a hot topic in manufacturing.
"While many of the labor-intensive manufacturing processes have been outsourced to foreign countries, we have seen a concerted effort from U.S.-based customers to keep their compression molding processes in the States," Dixon said. "The most cost-efficient way for them to do this is via automation. Within the last year, we have built several compression molding presses that are loaded and unloaded via conveyor systems or industrial robots.
"By automating their processes, many of our customers have found that they can successfully manufacture their parts in the U.S. for less money than they otherwise could outside of the country," especially once you take into account associated costs such as scrap rates and shipping charges, Dixon said.
On the mold-heating front, the biggest trend Beckwood has seen is the end user's desire to have the press's control system regulate mold temperature in addition to the press parameters. "Keeping all of the process controls under one platform allows for a clean and accurate data-acquisition system, with part-to-part traceability," Dixon said.
One of the most encouraging signs is that the last few years of growth in compression molding have been spread across a variety of industries, not concentrated in one sector. "While the aerospace market continues rapid growth, we've also seen an increased demand in the automotive, medical and energy sectors," Dixon said.
Michael T. McCue, copy editor
For more information
Beckwood Corp.
Fenton, Mo., 636-343-4100,www.beckwoodpress.com
Carver Inc.
Wabash, Ind., 260-563-7577, www.carverpress.com
Sacmi USA Ltd.
Des Moines, Iowa, 515-276-2052, www.sacmiusa.com
Surface Generation America
Richardson, Texas, 972-699-9976, www.surface-generation.com
Wabash MPI
Wabash, Ind., 260-563-1184, www.wabashmpi.com
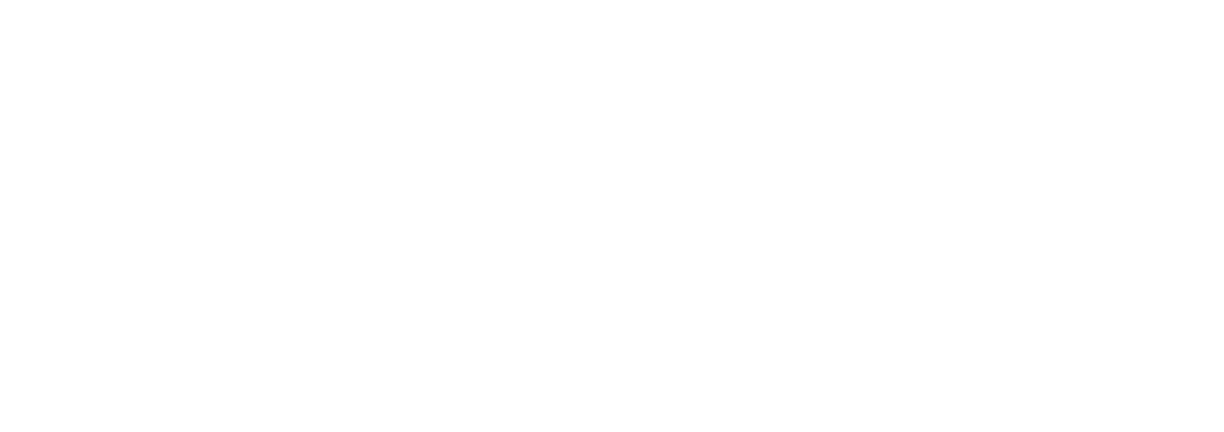