Processing Technologies International (PTi) is entering the high-speed sheet extruder market.
Last month, the company launched its Super-G high-speed extruders to process PP and high-impact PS (HIPS) for the packaging market.The line features two models — the SGHS3000-36D and the SGHS3000-42D.
The machine line furthers PTi's mission to differentiate itself, said PTi President Dana Hanson. "We advocate many different machines for different applications. So that's no different for our high-speed offering. While the competition pushes high speed for everything, high speed's going to become just another offering for us."
PTi is starting out in the high-speed extruder market with the two models, with barrel bores of 75mm, or about 3 inches. "We possibly can expand to a 90mm platform down the road," Hanson said. "But that'll be driven based on market demand."
A bigger machine, such as a 6-inch extruder, has greater throughput, but it runs more slowly. "It's not necessarily an advantage, it's a necessity to how you are going to get the rate out of a smaller machine — you run it faster," Hanson said. With such a small machine, the machine "takes a lot of little bites."
The 36D comes with a 500-hp motor and runs at a maximum speed of 1,000 rpm. The 42D operates with a 600-hp motor and can run at a maximum of 1,200 rpm. PTi established those maximum speeds based on an upper motor load threshold of 85 percent. The 36D can process about 3,000 pounds of PP per hour.
Hanson said the machines could go faster mechanically, perhaps to 1,500 rpm. "Practically, it'll probably run between 800 and 1,000 in a production environment."
One of the challenges with high-speed extruders is melt homogeneity. "Because the material's going through the machine so quickly there's very little residence time, and there's not a lot of time to homogenize the melt," Hanson said. "In our system, we're implementing our Super-G Lobe technology. It's a cam-style, distributive screw, so it's a low-intensity mixing screw, which gives us the ability to deliver a high-quality melt off the discharge end of the machine."
He said the machine's small footprint — 17.5 feet by 4.5 feet — makes it especially attractive to some customers. "They're small machines," he said. "To get 2,500-3,000 pounds an hour, which is comparable to a 6-inch extruder, the high-speed machine has a much smaller footprint." Floor space at plants operated by PTi's customers can be scarce.
In addition to the machines' small size and fast speeds, Hanson pointed to a number of other benefits that PTi offers to its customers. It provides U.S.-made machines with parts and service available in the States. "It's also not the only one-trick-pony offering that we have," he said. "You couple that with our variety of roll stands, and we do very thin-gauge sheet applications and also thicker, heavier-gauge applications."
The Super-G extruders include carbide-lined barrels and Colmonoy hard-faced screws. The screws use a powder metallurgy bonding process that involves physical welding of the material on to the flights of the feed screw. Then, the flights are ground down to the finished dimensions. "So you have a much deeper penetration of a much harder material. It should mean that the screws last longer. It's also a more expensive process," Hanson said.
The extruders feature an oversized feed section that can process material blends with scrap rates up to 70 percent. Hanson said PTi has a good deal of experience handling high volumes of regrind, and it incorporates that knowledge into the front end of the high-speed machines. The Super-G extruders also have streamlined feed hoppers with supports, delivery chutes and tramp metal protection.
Other features of the extruders include feed screw removal from the back of the unit, a vent chamber that is designed for easy cleaning and linear bearing barrel glide support, for which PTI has a patent pending. Another highlight is special air-cooled heater and blower assemblies that keep the exterior temperature below 110 degrees Fahrenheit for safety and efficiency, compared with competitive models that can reach 500 degrees Fahrenheit.
The extruders also boast energy efficiency — for PP for example, the line can process 6-7 pounds or more per hour per unit of horsepower.
Allan Gerlat, correspondent
Contact
PTi, Aurora, Ill., 630-585-5800, www.ptiextruders.com
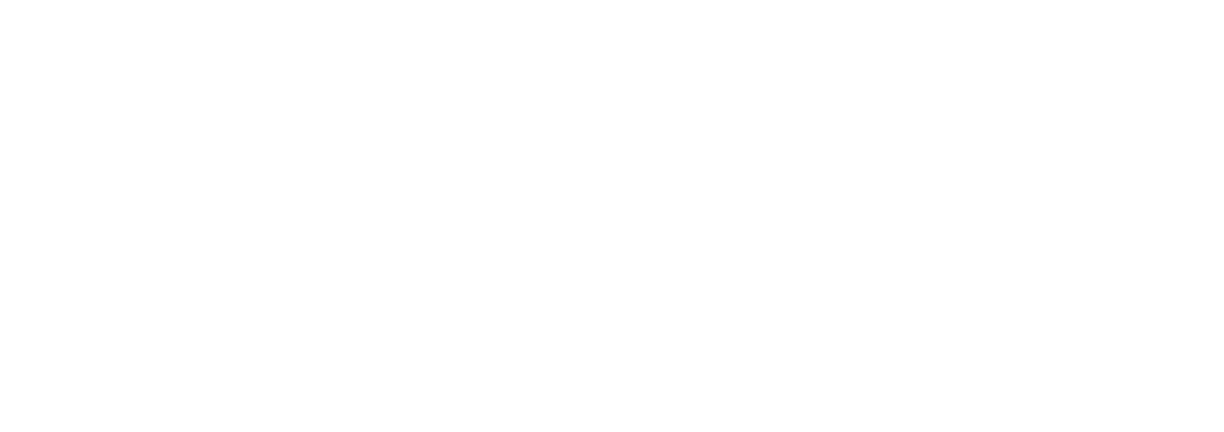