Special Report: Many drying technologies available to processors
Processors often need to dry resin to ensure quality end products, and there is an array of dryer technologies that can help them achieve that goal. Six major technologies are available: wheel desiccant dryers, twin-tower desiccant dryers, compressed air/membrane dryers, vacuum dryers, hot air dryers, and central drying systems.
Mark Haynie, dryer product manager for Novatec Inc., Baltimore, said the selection depends on a number of factors, including:
• What type of resins need to be dried, and are they hygroscopic or nonhygroscopic?
• How will the equipment fit in with existing plant equipment?
• If it is a dedicated dryer, should it be beside the machine or on the machine?
• Would it make sense, based on usage and available space, to invest in a central drying system?
HOT AIR DRYERS
Hot air dryers are primarily for nonhygroscopic materials. Unlike hygroscopic resins, nonhygroscopic resins — such as PP, PE and PVC — do not allow moisture to penetrate the surface of pellets. In these cases, drying resins is much simpler, and a hot air dryer may be sufficient to remove surface moisture. The dryers' performance varies depending on ambient relative humidity.
"They are great if you are just trying to remove surface moisture off things," Haynie said.
DESICCANT DRYERS — TWIN TOWER
Twin-tower dryers use beaded desiccant media, a composite of clay and a molecular sieve, to remove moisture from resin. Capacities range from 5 pounds to 5,000 pounds per hour. Twin-tower dryers may require additional cooling of the processing air when used with resins that must be dried at temperatures below 160 degrees Fahrenheit.
Twin-tower dryers have somewhat variable dew-point performance and may not be as energy efficient as wheel-type dryers when processing engineering resins.
DESICCANT DRYERS — WHEEL
Instead of using desiccant beads, the wheel dryer uses desiccant in a honeycomb form. Dew point and temperature stay constant and the dryers can dry both high-temperature and low-temperature resins.
The units are compact and sizes range from 5 pounds per hour to 5,000 pounds per hour. Variable speed drives can reduce energy use by reducing drying air to the minimal amount required.
COMPRESSED AIR AND MEMBRANE DRYERS
Typical compressed air dryers are less common than some other types, in part because without membranes, they are not able to reduce dew points as low as other technologies — especially during humid weather, Haynie said.
A plant compressor system starts with cool ambient air and compresses it, which causes water vapor to condense out of the air, lowering its dew point. That air is then supplied to the compressed air dryer.
However, membrane dryers are much more effective in lowering moisture levels. Membrane dryers also use compressed air and typically produce a dew point of minus 40 degree Fahrenheit by using hollow tube membranes to remove water vapor. Membrane dryers with a dual loop consume about as much energy as desiccant dryers.
VACUUM DRYERS
Vacuum dryers can be the most energy-efficient option for drying many types of resin pellets. The dryers have three basic operations: heating, vacuuming, and material discharge.
"Vacuum dryers work very well for pelletized engineering resins," Haynie said.
CENTRAL DRYING SYSTEMS
Processors who have sufficient demand to invest in a central drying system will benefit from several advantages, not the least of which is confining all material handling to one area of a plant, thus reducing labor requirements and making cleanup and material changes easier.
Installing a central system rather than stand-alone dryers frees up floor space for processing machines, and a central system might also use less energy.
INFRARED DRYERS
These dryers are less common because they have a higher cost than a typical desiccant dryer, but they are ideal for PET used in sheet, Haynie said. They are very competitive when doing both crystallizing and primary drying. The infrared heat penetrates well inside of the resin flake or pellet and drives the moisture out while crystallizing the resin at the same time.
Bruce Geiselman, correspondent
Bruce Geiselman
Senior Staff Reporter Bruce Geiselman covers extrusion, blow molding, additive manufacturing, automation and end markets including automotive and packaging. He also writes features, including In Other Words and Problem Solved, for Plastics Machinery & Manufacturing, Plastics Recycling and The Journal of Blow Molding. He has extensive experience in daily and magazine journalism.
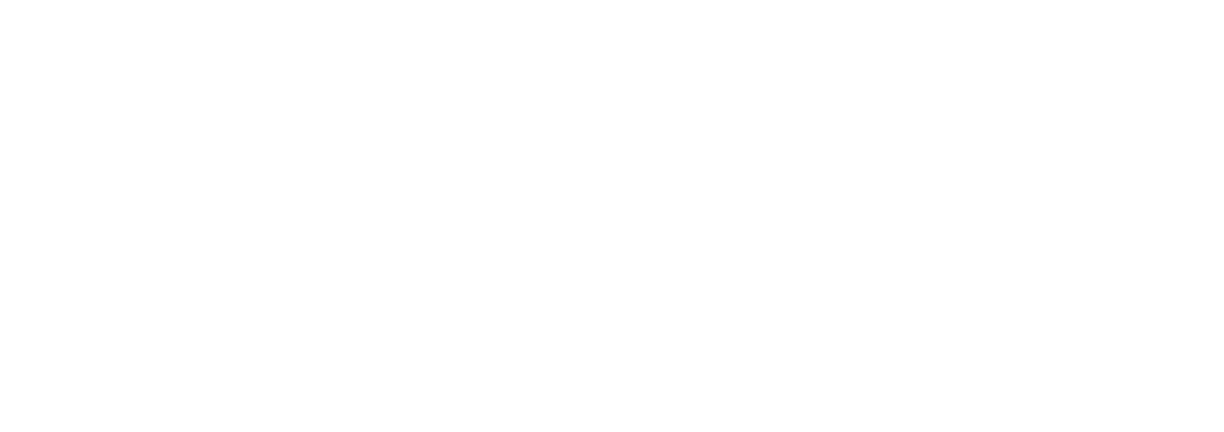