Being able to make products using the whole spectrum of color is one of the advantages of plastics. But sorting those colorful products for recycling when their useful life has passed can require a spectrum of technologies.
NATIONAL RECOVERY TECHNOLOGIES LLC
In January, Nashville, Tenn.-based National Recovery Technologies LLC (NRT) introduced a new color sorter, the ColorPlus-R. It uses an image-processing system to detect and sort a wide variety of materials based on color analysis and object recognition, and is similar to the company's ColorPlus sorter. What distinguishes the ColorPlus-R is its ability to color analyze opaque objects, such as black plastics, the company says.
Black plastic is challenging to sort. "Historically, there has not been a reliable way to remove black polymers from a mixed stream," NRT President Matthias Erdmannsdoerfer said. "Black material absorbs light, making it impossible to identify with near infrared [NIR] detection." For a plastics recycling facility, the frequency of contamination can determine success.
The ColorPlus-R has a second LED light source above the material for reflective detection, in addition to the transmissive light source used for detection in the ColorPlus. NRT says the use of both reflective and transmissive detection is what makes color analysis possible.
The machine uses NRT's In-Flight Sorting technology, which detects and ejects material almost simultaneously after it has left the conveyor belt. A potential problem with equipment that detects the material on the conveyor belt and ejects it from the waste stream later is that bottles can move on the conveyor belt between the detection and ejection steps. Also, the conveyor belt itself can interfere with material detection. In-Flight Sorting uses a line-scan camera and proprietary software to process up to 50 million pixels per second.
All of NRT's optical sorters can identify a bottle's color when only a small portion of it is visible, Erdmannsdoerfer said. For example, ColorPlus machines can identify the color of a bottle, even if it has a label around it.
SESOTEC INC.
Customers are demanding more from their sorting equipment, said Tracey Hartje, North American sales manager for sorting and recycling for Sesotec Inc., Bartlett, Ill. They want their sorters to handle bottles that have differing sizes, resins, colors or labels. Customers want to boost throughputs and improve efficiency — and remove metal at the same time.
"What customers are looking for is if you can get one machine that can accomplish a few tasks," Hartje said. "In our case, it's polymer detection, color detection and metal detection. If you need all those technologies in one machine, it's less expensive."
At the K show, Sesotec introduced its Flake Purifier+ line of sorting systems. The compact machines use cameras and near-infrared spectroscopy with hyperspectral imaging technology to allow for shape, color and material sorting, as well as metal separation. The compact machines can handle a variety of materials, including PET, HDPE and mixed plastics, and are designed for easy maintenance.
Four machine sizes are available, with throughputs ranging from 3.3 tons per hour to 6.6 tons per hour. The Flake Purifier+ machines feature an optimized material infeed system for more evenly distributed material flow and increased throughput, Hartje said. The machines also have the new SesoDesk operating software. Their dust-proof design protects the sensors, lighting units and electronics, while integrated connections for dust and label extraction make the recycling process more efficient, he said.
Sesotec also upgraded its Varisort line of optical sorting systems last year with software improvements and bigger working widths of about 9 feet for greater throughputs. The machines' advanced sensor technologies can detect metal, color and polymer type. Hartje said Sesotec's sensors can be programmed to detect approximately 17 million colors.
TOMRA SORTING SOLUTIONS
At the K show, Tomra Sorting Solutions, Asker, Norway, exhibited its recently upgraded Autosort Flake sorting system, which sorts plastic flakes by color and material type while simultaneously detecting ferrous and nonferrous metals.
The company now is offering a new option for Autosort Flake; the new Reflect feature allows the user to sort opaque materials by color. Autosort Flake normally works in transmission mode, using a backlight, which means that the products to be sorted are on a chute between the camera and the light, said Alexander Wolf, sales engineer for Tomra. The Reflect option allows the machine to sort in reflection mode, in which the light and the camera are on the same side of the material to be sorted. This is useful for color sorting of opaque materials such as HDPE, Wolf said. Existing Autosort Flake systems can be upgraded with the new technology.
Tomra offers two other lines of equipment for color sortation: Autosort and Autosort Fines. Autosort is for bigger material, "basically you can sort anything that goes down to an inch by an inch," Wolf said. Autosort Fines is appropriate for somewhat smaller material, and the Autosort Flake is for material measuring about 0.5 inch or smaller.
All of the Autosort lines feature Tomra's Flying Beam technology, which incorporates energy-saving lighting and high-precision NIR sensors for better product recovery and stable performance at a wide temperature range. Continuous calibration of the sensors allows the user to monitor and optimize the sorter's performance.
Distributor Van Dyk Recycling Solutions, Stamford, Conn., represents Tomra in North America.
MSS INC.
MSS Inc., Nashville, Tenn., supplies optical sorting systems for a wide range of materials, including several systems for sorting plastic bottles or flakes. Its L-VIS flake sorter was recently upgraded with a high-resolution color camera system and performs separation based on color and shape for pellets and very small or thin particles, down to 1mm. It is suitable for PE, PP, PET and other resins.
The L-VIS accelerates the flakes or pellets to 500 feet per minute on a high-speed conveyor; they are analyzed as soon as they fly off the conveyor, MSS sales director Felix Hottenstein said. Nozzles emitting highly compressed air are used to separate the targeted materials.
The upgraded camera system allows the L-VIS to sort the particles in-flight over an illuminated reference background, the color of which is adjustable, for maximum contrast.
"So, for example, if we want to sort non-white HDPE flake from white or natural HDPE flake, we set the background to white and eject any particle that diverts from that white color. Or similarly, if we want to sort blue from red flake, we would set the background to a red color and eject any color that deviates from the red color above a certain threshold," he said.
Preparation of the material to be sorted is critical. "If the material's not prepared correctly, then your sorting's not going to work very well at all," he said. "If there's a possibility or an option to prepare the material better, then you'd always want to do that first before actually trying to sort it."
For example, fines should be removed, and a vibratory feeder should be used to spread out the resin flakes across the entire width of the machine as they enter the sorter.
The L-VIS can process 1 ton to 2.5 tons of plastic flake per hour with up to 98 percent accuracy.
Allan Gerlat, correspondent
Contact:
MSS Inc.,615-781-2669, www.magsep.com
National Recovery Technologies LLC, 615-734-6400, www.nrtsorters.com
Sesotec Inc., 224-208-1900, www.sesotec.us
Van Dyk Recycling Solutions, 203-967-1100 , www.tomra.com
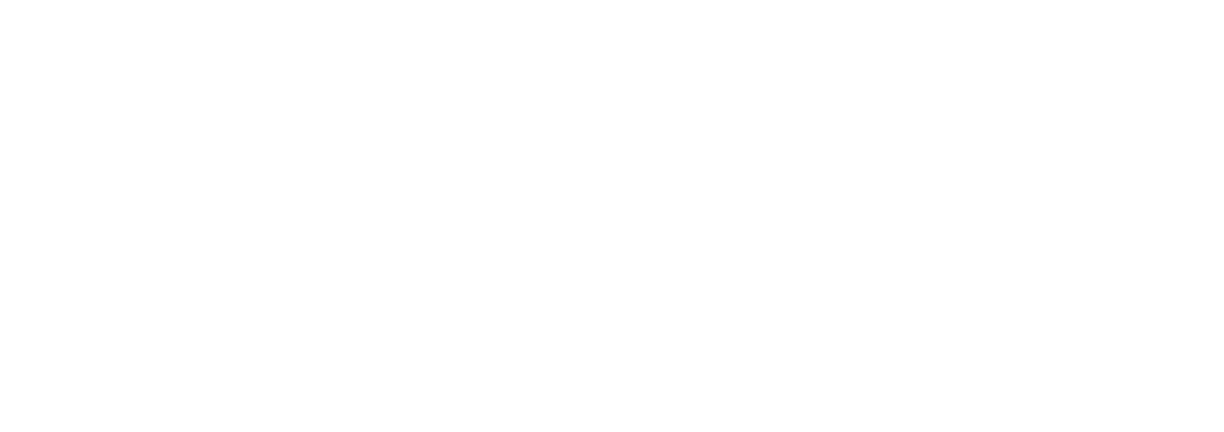