Stäubli Corp., Duncan, S.C., has demonstrated a new, fully automated quick-mold-change (QMC) system that ensures a safe mold exchange within minutes.
The system, which Stäubli exhibited at the K show, removes a mold from the injection press and replaces it with a preheated, production-ready tool. It lets processors with frequent mold changes prepare the next mold in parallel with ongoing production, in keeping with the single-minute-exchange-of-die (SMED) concept.
To create the system, Stäubli drew on its experience designing and manufacturing robotics, sensors, magnetic clamps, rapid-connection devices and tool-changing tables and trolleys. Networked communication between the QMC system and the injection molding machine enables processes to be coordinated and optimized.
The process starts with a station where the new mold is heated. The mold can be coupled to a preheating station manually or automatically via Stäubli's multicoupling technology, which allows all power and signal connections to be switched on from a single control.
Sensors integrated into the mold detect the condition of the mold. Monitoring the mold before it is inserted into the machine allows any faults — such as failure to reach the right operating temperature — to be corrected.
Stäubli's system includes a mold-loading table (MLT) that is on rails and is driven by a power roller system. It transfers the preheated mold from the preparatory station to the injection machine. Stäubli designed the MLT to support molds weighing up to 60 tons, for use with injection machines with clamping forces up to 4,000 tons, according to the company. The MLT is "smart," processing data it receives from both the mold and the injection machine to accurately adjust its height for mold transfer.
When the QMC system receives a signal to execute the tool change, a strapping system automatically locks and holds together both halves of the mold that is already in the machine. Fully automatic quick-coupling devices disconnect all electronic connections to the mold. Stäubli's Imag magnetic clamping system declamps the production mold. The QMC system uses a proprietary ejector system to separate the mold halves automatically prior to declamping.
A heavy-duty, electrically powered mold-handling mechanism pulls the mold from the platen to the MLT, then places the new mold into the press. Data from sensors on the MLT, the two molds being exchanged and the mechanisms on the MLT detect the position of the table and the molds to ensure accurate mold handling and positioning.
The injection molding machine and the MLT automatically coordinate their status at every step of the exchange. Stäubli's tool-centering ring ensures accurate mold positioning. When the mold is positioned, it is magnetically clamped. The entire mold change can occur in less than a minute due to the interplay of various quick-change components and networked communication. All measured values, including mold temperature, are communicated with the machine and logged with the history of that mold.
Mikell Knights, senior staff reporter
Contact:
Stäubli Corp., 864-433-1980, www.staubli.com
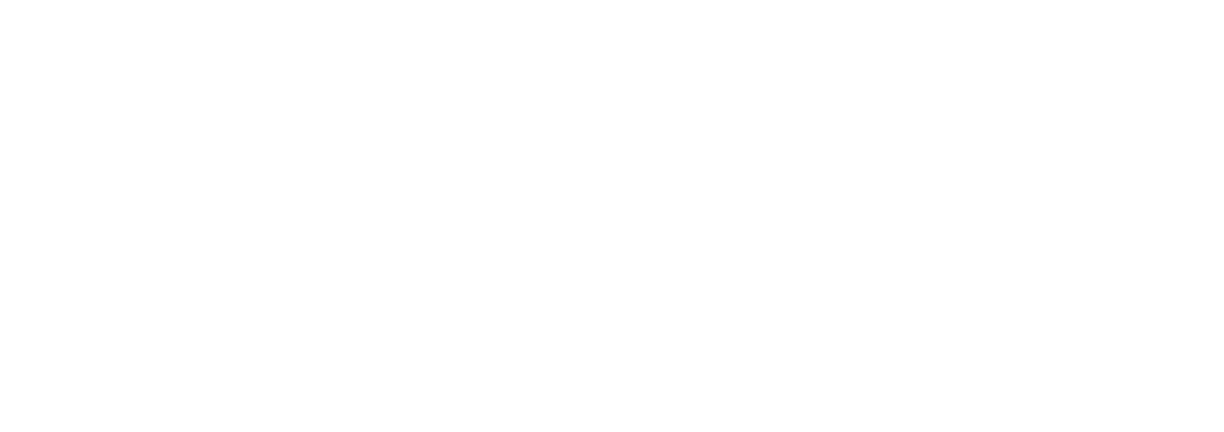